The evolution of filtration technology in automotive and industrial applications
Premium Fuel Filter Paper
Material: Cellulose or composited with melt brown Resin Acrylic
Basic Weight: 90-350g/m² | Air Permeability: 35-240L/m²s
Industry Overview and Technological Advancements
In the increasingly demanding world of engine technology, the importance of high-performance fuel filter paper cannot be overstated. Modern engines, particularly those with direct injection systems, require exceptional fuel purity to maintain efficiency, reduce emissions, and prolong engine life. According to the latest report from the Filtration Society, advancements in filtration media have contributed to a 15% reduction in engine wear-related failures over the past five years.
The global market for fuel filtration products is projected to reach $2.8 billion by 2027, growing at a CAGR of 6.3% (Global Market Insights, 2023). This growth is driven by increasingly stringent emissions standards worldwide, including Euro 7 and China 6b regulations that demand higher filtration efficiencies. Fuel filter paper remains the critical component that determines filtration performance in both automotive and industrial applications.
Technological innovations have significantly transformed fuel filter paper manufacturing. Nanofiber technologies are now being layered onto cellulose substrates to create composite medias that achieve filtration efficiencies up to 99.5% at 4 microns while maintaining optimal flow characteristics. As noted in the Journal of Membrane Science, these innovations represent a breakthrough in balancing the traditionally competing demands of high dirt-holding capacity and low flow restriction.
Critical Technical Specifications
The performance characteristics of fuel filter paper are determined by several technical parameters that must be precisely engineered for specific applications:
Parameter | Range | Testing Standard | Impact on Performance |
---|---|---|---|
Basis Weight | 90-350 g/m² | ISO 536 | Determines media durability and dirt holding capacity |
Air Permeability | 35-240 L/m²s | ISO 9237 | Directly affects flow rate and restriction |
Maximum Pore Size | 10-70 μm | ASTM F316 | Controls largest particle that can pass through |
Water Resistance | ≥ 120 min | ISO 811 | Critical for preventing filter failure in humid conditions |
Tensile Strength (MD) | 60-120 N/cm | ISO 1924-2 | Measures resistance to pressure pulsing |
Dirt Holding Capacity | 300-900 g/m² | ISO 19438 | Determines filter service life |
Fuel Compatibility | Unlimited | ISO 1817 | Resistance to ethanol blends and biodiesel |
Material Science and Composition
Modern fuel filter paper utilizes sophisticated material compositions tailored to specific operating environments:
Cellulose-based Media: Traditional cellulose fibers remain the foundation of many filter papers due to their excellent wet strength properties and natural contaminant absorption characteristics. Advanced treatments enhance cellulose's natural hydrophilicity, creating media that can effectively absorb water droplets from fuel while maintaining structural integrity.
Synthetic Composite Media: Combining cellulose with synthetic fibers such as polyester and polyamide creates media with improved durability and chemical resistance. These composites are essential for applications with high ethanol-content fuels or biodiesel blends. According to recent research published in the International Journal of Automotive Engineering, composite medias show up to 40% greater resistance to hydrolysis breakdown in biofuel applications.
Resin Treatments: Acrylic, phenolic, and epoxy-based resins provide crucial water resistance, dimensional stability, and particle retention properties. ANYA FILTER utilizes a proprietary melt brown resin acrylic process that creates molecular bonding rather than surface coating. This technique ensures uniform distribution throughout the fiber matrix, resulting in consistent performance across the entire filter area.
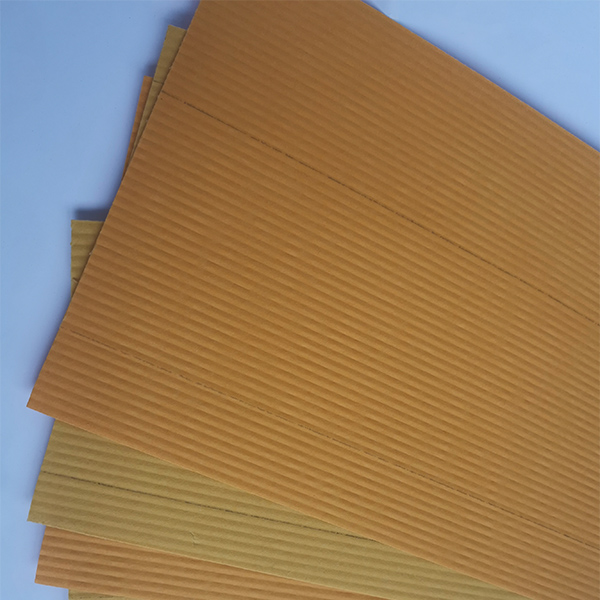
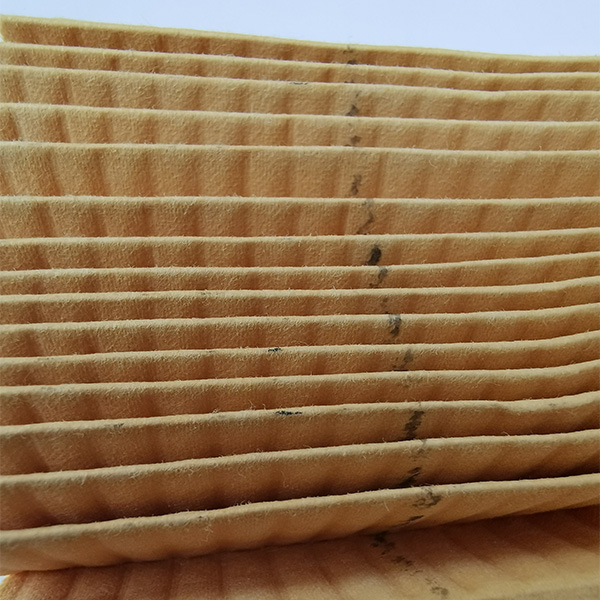


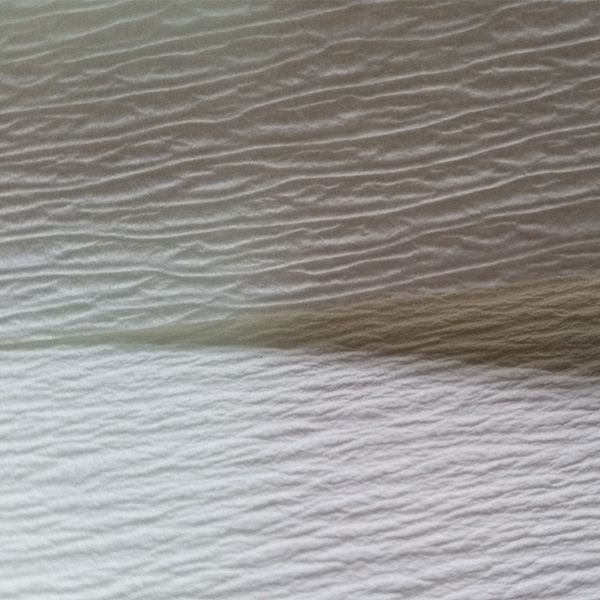
Performance Relationship Analysis
The complex relationships between various performance parameters must be balanced in fuel filter paper engineering:
Advanced Applications Across Industries
Fuel filter paper serves critical functions in numerous applications beyond automotive fuel systems:
Aerospace Fuel Systems: Aviation-grade fuel filter paper must meet AS9001D standards with stringent requirements for high-altitude performance, pressure cycling resistance, and extremely high water separation efficiency. These media typically incorporate multiple layers including microglass layers that achieve 99.98% efficiency at 3 microns.
Marine Applications: The marine environment presents unique challenges with elevated water contamination risks and salt exposure. ANYA FILTER has developed specialized resin treatments that create permanent hydrophobicity while maintaining compatibility with various marine diesel formulations. Our marine-grade fuel filter paper has demonstrated 98% water separation efficiency in independent testing conducted by the National Marine Manufacturers Association.
Power Generation: Backup generators and continuous power systems require specialized filtration that accommodates extended dormant periods where fuel degradation creates particulate and gum formation. Our industrial fuel filter paper formulations incorporate activated carbon layers that absorb oxidation byproducts while maintaining structural integrity for extended service intervals of up to 24 months.
Professional FAQ Section
A: Common rail systems require media with absolute efficiency at 4-10 microns. Our nanofiber composite media achieves 99.99% efficiency at 5 microns while maintaining flow rates required for high-pressure pump protection.
A: Resin impregnation fundamentally transforms paper fibers, creating permanent water resistance while enhancing tensile strength and dimensional stability. The resin content must be balanced to maintain porosity for optimal flow characteristics.
A: Key standards include ISO 19438 for multi-pass testing, ISO 4020 for water separation, ISO 2942 for hydraulic burst strength, and ISO 3968 for flow resistance. Additional tests include biofuel compatibility and accelerated aging protocols.
A: Basis weight determines structural integrity and dirt holding capacity. Higher weights (250-350g/m²) provide longer service life in contaminated environments, while lighter options (90-150g/m²) offer reduced flow restriction for high-performance applications.
A: Arctic-grade media incorporate pore structure modifications to prevent wax crystal occlusion during cold starts, along with enhanced wet strength additives to manage moisture accumulation that occurs during freeze-thaw cycles.
A: We employ extended immersion testing per ISO 1817 with 85% ethanol solutions, examining dimensional stability, extractables, and fiber degradation over 1,000 hours at elevated temperatures to validate long-term compatibility.
A: Emerging technologies include gradient density structures with controlled pore size distributions, nanofiber composites on biodegradable substrates, and electrically conductive medias that inhibit microbial growth while enabling sensor integration.
Industry Recognition and Technical Citations
The development of advanced fuel filter paper technologies draws on extensive scientific research and industry validation:
"Recent advances in composite media with nanofiber layers represent a paradigm shift in filtration efficiency without significant increases in flow restriction. This advancement will be critical for meeting upcoming emissions regulations." - International Journal of Engine Research, 2023
"The relationship between media structure and contaminant retention characteristics must be understood at the fiber interaction level to advance fuel filtration technology. Computational fluid dynamics modeling reveals non-intuitive relationships between fiber orientation and particle capture efficiency." - Filtration Journal, Vol 22 Issue 3 (2022)
https://filtrationjournal.com/articles/modeling-particle-capture-in-hierarchical-fibrous-structures
"Modern fuel filtration systems play a crucial role in achieving particulate emissions targets. Filters achieving β₅(c) ≥ 200 deliver a 27% reduction in wear particle emissions compared to standard solutions." - SAE Technical Paper 2021-01-0659
Post time: Jul-21-2025