Comprehensive Guide to HEPA Pleating Machine Technology, Applications, and Manufacturer Comparison
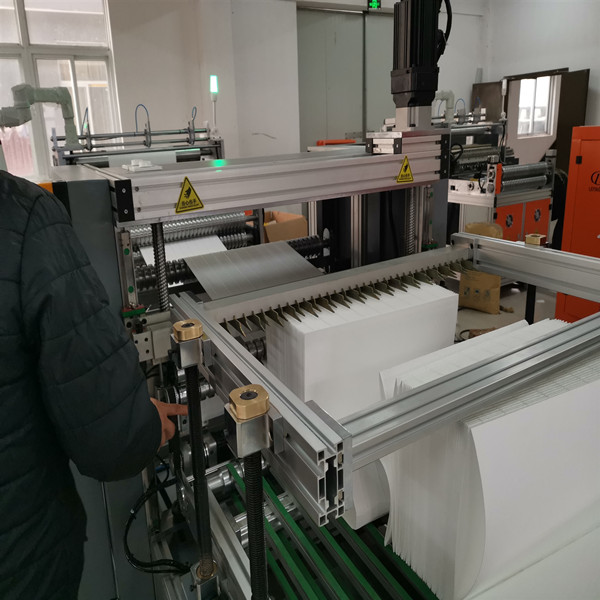
HEPA pleating machine (High-Efficiency Particulate Air pleating machine) is specialized automation equipment designed for the high-precision pleating of filter media used in HEPA filter manufacturing. Also known as hepa filter pleating machine, these systems play a crucial role in achieving consistent pleat geometries, optimal filter performance, and cost savings for mass production lines in pharmaceuticals, electronics, hospitals, and industrial air purification.
- Filtration Efficiency: Achieves particle capture rates ≥99.97% at 0.3μm, as per ISO 29463 and EN 1822.
- Pleat Depth Range: Customizable from 10mm to 110mm, supporting mini, standard, and deep pleat HEPA/ULPA panels.
- Media Compatibility: Supports glass fiber, PTFE, PP, PET, composite synthetic fiber, and more.
- Automation Level: Servo-driven, PLC-controlled; online slitting, hot melt spacing, counting, and stacking functions.
The Pleat Machine For Hepa Filters by AnYa Filtermedia (product link) integrates advanced modular servo drives, CNC-precision-engineered components, and ISO 9001:2015 manufacturing standards. The system supports both Z-line and mini-pleat formats, and is widely adopted in high-demand sectors such as petrochemicals, metallurgy, and urban water supply.
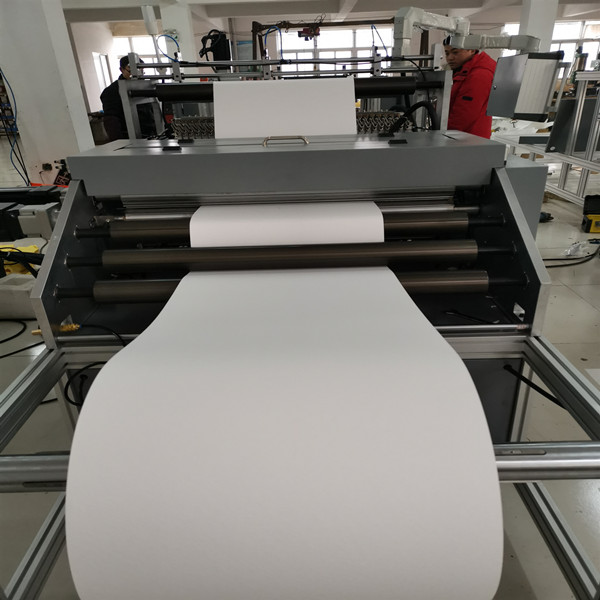
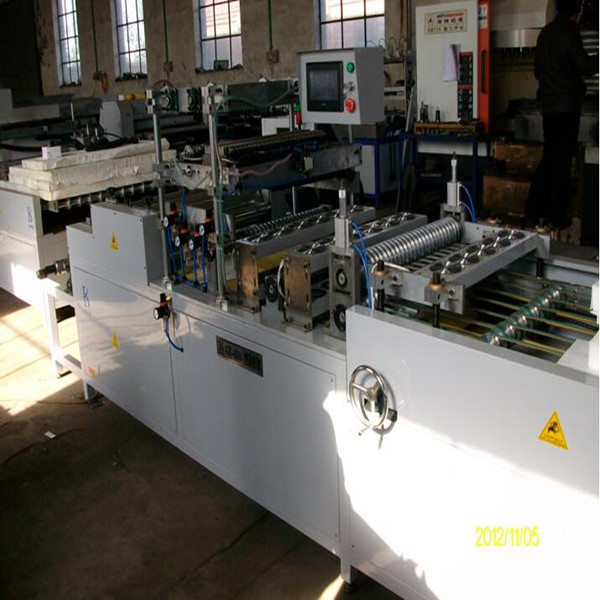
Key point: All critical components are CNC-machined (tolerance
Component | Material | Processing Method | Notes |
---|---|---|---|
Frame | SS 304/316, Aluminum Alloy | CNC machining, welding | Anti-corrosion, strong rigidity |
Pleating Rollers | Hardened Steel, PU Coating | Precision CNC lathe | High wear resistance |
Guide Rails | Chrome-plated steel | Grinding & Plating | Low friction, longer life |
Hot Melt Gun | Stainless Steel, Teflon | Thermal molding | Accurate adhesive control |
Control System | PLC+ HMI | Assembly, wiring | SIEMENS, Omron options |
Routine inspection involves online vision-based pleat uniformity checks and spot air permeability testing. The entire manufacturing workflow is compliant with ISO 29463, EN 1822, and client-specified standards in cleanroom, medical, and industrial applications.
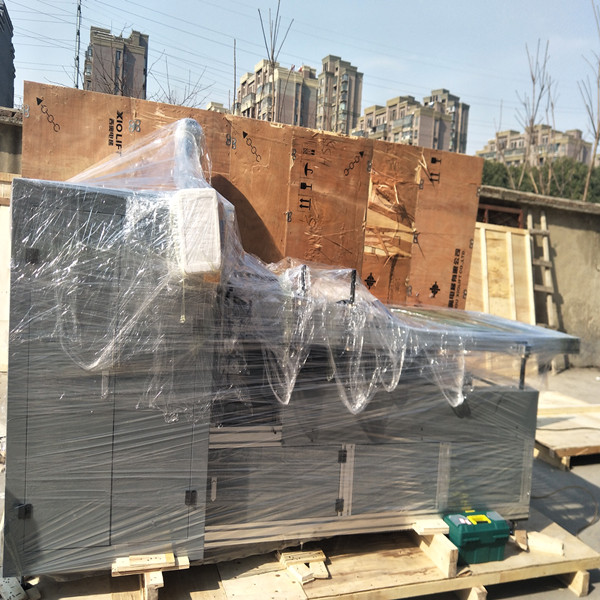
Model | Pleat Height (mm) | Speed (pleats/min) | Max. Media Width (mm) | Automation | Hot Melt Glue | Certification |
---|---|---|---|---|---|---|
Pleat Machine For Hepa Filters | 10-110 | ≤400 | 1000 | Full-servo, PLC | Yes (multi-nozzle) | ISO 9001, CE |
Bosch PM600-H | 16-85 | ≤340 | 915 | Stepper, PLC | Yes | ISO, RoHS |
JINAN FP-800 | 22-100 | ≤300 | 1000 | Stepper | No | ISO 9001 |
Average (Top 10) | 18-95 | 340 | 960 | Mixed | 60% | ISO 9001 |
Parameter | Specification |
---|---|
Pleat Height Range | 10-110 mm (customizable) |
Pleat Pitch | 2-5 mm |
Max. Filter Width | 1000 mm |
Production Speed | Up to 400 pleats/min |
Hot Melt Glue | Multi-line / Multi-nozzle |
Control System | PLC + HMI (Siemens/Omron) |
Support Media | Glass fiber, PTFE, PET, PP, composites |
Safety Level | CE/UL compliant, emergency stop |
Certification | ISO 9001:2015, eligible for FDA audit |
Operating Environment | Ambient 5–40°C, Humidity ≤90% |
Dimensions | 2500x1600x1600mm |
Service Life | >8 years (avg. 3-shift operation) |
Core Strength | Pleat Machine For Hepa Filters | Industry Avg. |
---|---|---|
Minimum pleat pitch (mm) | 2.0 | 3.0 |
Glue distribution accuracy | ±0.15 mm | ±0.3 mm |
Service life (years) | 8+ | 5 |
Control system | PLC+HMI (SIEMENS/Omron) | PLC |
Certification | ISO 9001, CE | ISO 9001 |
Support for mini-pleat | Yes | 60% |
- High precision pleat forming: Ensures even air flow and over 99% efficiency for 0.3um particulates.
- Reduced labor cost: 50% less compared to manual pleat forming lines (based on 2023 sampling in Asia).
- Glue economy and repeatability: Hot melt metering saves up to 38% adhesive, reduces clogging/defects.
- Traceable quality: PLC & vision QC enables real-time process data logging, facilitating ISO/FDA audits.
- Multi-format compatibility: Supports deep, standard, mini-pleat production with rapid format switching.
- Durable construction: Stainless/aluminum structure, lifespan >8 years, low maintenance (average downtime
- Applicable industries: Hospital sterilization, cleanrooms, petrochemical gas purification, food & pharma production, metallurgy, HVAC, and more.
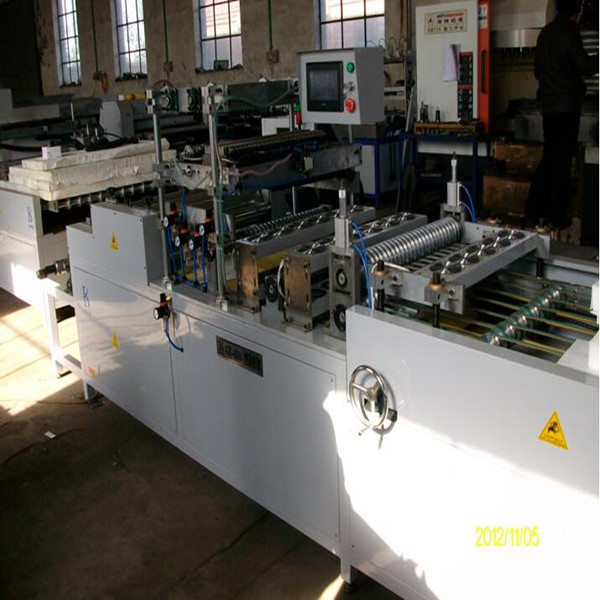
- Pressure Drop: HEPA filters inherently cause a relatively high air resistance (initial pressure drop up to 220 Pa, see EPA 2021 Report), which can increase HVAC system energy consumption if not managed or sized appropriately.
- Cost of Replacement: Due to fine media and strict testing, HEPA filters are expensive and require regular replacement, adding to lifecycle operation costs & waste management obligations.
Reference: CDC HEPA Technical Guidance
Supplier | Core Advantage | Options/Customization | Certifications | Reference Projects |
---|---|---|---|---|
AnYa Filtermedia | High-precision servo pleating, multi-nozzle glue, ISO tested | Pleat geometry, hot melt layout, output mode | ISO 9001, CE, FDA eligible | Pharmaceutical, Electronics (Fortune 500) |
Bosch | Robust industrial design, energy monitoring | Mini-pleat module, custom cutters | ISO, RoHS | Cleanroom air systems (EU) |
Purafilter | Entry-level cost, line integration | Limited | ISO 9001 | HVAC factories (India, SEA) |
- Submit usage scenario (pharma, cleanroom, metallurgy, etc.) & required media specs.
- Pilot sample manufactured for pleat pattern and test filtering characteristics.
- Production equipment tailored—pleating pitch, glide tracks, hot melt nozzles, control system.
- Certification testing (ISO, EN) for final product. Final acceptance, packaging, secure shipment.
Pharma Anya Filtermedia’s hepa pleating machine enabled a 33% increase in HEPA panel output for a EU GMP-certified vaccine plant, with a 70% noted reduction in pleat rejects (measured against manual formation).
Petrochemical Switched from imported lines to local Pleat Machine For Hepa Filters, achieving 21% adhesive savings and improved corrosion resistance of output filters (SS 316 frame). Directly credited with prolonging filter replacement interval by 45%.
Electronics Flexible pleat-depth adjustment supported customized filter production for their critical cleanroom zones. Pass rate for mini-pleat filters reached 99.85% (in-house audit, 2023).
Metallurgy Installation and local operator training within 12 days. Average equipment OEE (Overall Equipment Efficiency) logged at 96.2% over the first 6 months.
- Lead Time: 25–35 days for standard models; custom solutions up to 60 days.
- Warranty: 2 years mechanical/electrical. Full lifetime technical support.
- After-sales: Global service network. On-site and remote diagnostic support (real-time monitoring interface via HMI/Cloud).
- Certifications: ISO 9001, CE, with many lines eligible for FDA audit compliance.
- Training: Operator and maintenance technician training included with delivery.
- Documentation: Test reports, installation manuals, operation SOP as per ISO/EN requirements.
- Customer Data Protection: NDA and client design confidentiality guaranteed.

- ISO 29463: High-efficiency filters & filter media for particle removal
- CDC/NIOSH: Technical Guidance for HEPA Filters, 2011
- MarketsandMarkets: Global HEPA Filter Industry Insights (2023)
- ISO 14644-1: Cleanrooms & associated controlled environments
- HEPA Filter Degradation and Lifetime Analysis (ResearchGate, 2022)
- Engineering StackExchange: HEPA Filters—Pressure Drop Experience in Industry
- Filtration+Separation: Top 10 Global HEPA Filter Companies (2023 List)
Post time: Jul-28-2025