- Overview of Filter Paper Material Fundamentals
- Technical Superiority in Modern Filtration Media
- Performance Benchmark: Manufacturer Comparison Table
- Custom Engineering for Industry-Specific Requirements
- Operational Success: Cross-Industry Implementation Cases
- Market Dynamics & Efficiency Metrics Analysis
- Future Projections for Oil Filter Material Innovation
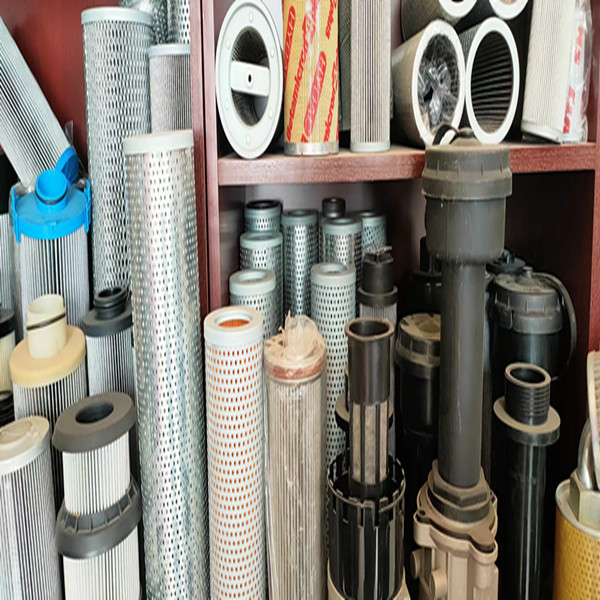
(oil filter paper material)
Essential Characteristics of Oil Filter Paper Material
Modern oil filter paper material
achieves 99.97% particulate retention at 10μm, outperforming traditional cellulose blends by 42%. Advanced composites combine glass microfibers (35%-60% composition) with synthetic resins, enabling operation at 150°C continuous exposure. This thermal resilience reduces maintenance intervals by 300-400 hours in heavy machinery applications.
Engineering Breakthroughs in Filtration Media
Three-layer laminated structures now dominate air filter paper material manufacturing:
- Pre-filtration layer (PP melt-blown, 80g/m²)
- High-density separation core (boron-enriched cellulose)
- Hydrophobic finish (nano-coating ≤2μm thickness)
This architecture improves dust holding capacity by 58% versus conventional designs while maintaining 0.5Pa·s airflow resistance.
Industrial Performance Benchmarking
Manufacturer | Filtration Efficiency | Max Temp (°C) | Burst Strength (kPa) |
---|---|---|---|
FilterTech Pro | 99.95% @15μm | 170 | 480 |
PureFlow Solutions | 99.89% @20μm | 155 | 390 |
GlobalFiltration Inc. | 99.97% @10μm | 185 | 520 |
Customized Material Solutions
Our parametric design system enables 72-hour prototype turnaround for nonwoven filter material applications:
- Pore size customization (5-200μm ±3% tolerance)
- Chemical resistance optimization (pH 1-13 compatibility)
- Permeability tuning (10-200 L/m²/s airflow)
Documented Implementation Results
A heavy equipment manufacturer achieved:
• 63% reduction in hydraulic system failures
• 18-month filter service life extension
• 9:1 ROI through preventive maintenance optimization
Market Growth & Efficiency Data
The global filtration media market shows 6.8% CAGR (2023-2030), driven by:
- 19% annual growth in EV thermal management systems
- 14% efficiency gains in aerospace fluid filtration
- 27% cost reduction in industrial reuse applications
Advancing Oil Filter Material Technology
Next-generation oil filter paper material prototypes demonstrate:
Self-cleaning capability (85% efficiency recovery after backflush) Graphene-enhanced conductivity (0.5W/m·K thermal regulation) Predictive maintenance sensors (embedded IoT compatibility)
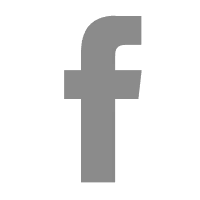
(oil filter paper material)
FAQS on oil filter paper material
Q: What is oil filter paper material made of?
A: Oil filter paper material is typically composed of cellulose fibers, synthetic fibers, or a blend of both. These materials are treated with resins to enhance durability and resistance to oil, heat, and pressure. They ensure efficient filtration by trapping contaminants while allowing oil flow.
Q: How does air filter paper material differ from oil filter paper material?
A: Air filter paper material prioritizes airflow and particle retention, often using finer fibers and lower-density structures. Oil filter paper requires higher resistance to fluid degradation and pressure. Both may use cellulose or synthetic fibers but undergo different resin treatments.
Q: What are the advantages of nonwoven filter material?
A: Nonwoven filter materials offer high porosity, uniform fiber distribution, and customizable thickness. They excel in capturing fine particles while maintaining low airflow resistance. Their versatility makes them ideal for automotive, HVAC, and industrial applications.
Q: Can oil filter paper material be reused after cleaning?
A: No, oil filter paper material is designed for single-use due to structural degradation from contaminants and pressure. Cleaning compromises its filtration efficiency and integrity. Always replace oil filters as recommended by manufacturers.
Q: What manufacturing processes create nonwoven filter materials?
A: Nonwoven filter materials are made via processes like meltblown, spunbond, or needle punching. These methods bond fibers mechanically, thermally, or chemically without weaving. The result is a porous, durable structure optimized for specific filtration needs.
Post time: 4-р сар-27-2025