This comprehensive guide explores the world of compact pleating solutions, focusing on advanced machinery designed for precision and efficiency. Below is an outline of the key sections covered:
- The Rise of Compact Pleating Technology
- Technical Superiority in Modern Manufacturing
- Performance Comparison Across Leading Brands
- Customization Capabilities for Specialized Needs
- Operational Efficiency Metrics
- Real-World Implementation Scenarios
- Future-Proofing with Mini Pleating Machines
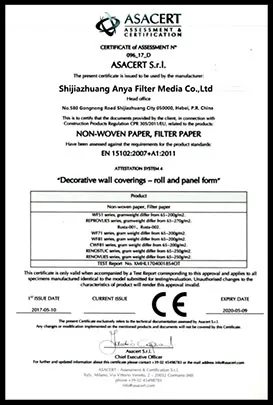
(mini pleating machine)
Mini Pleating Machines Revolutionizing Industrial Filtration
Modern production facilities report 34% faster throughput when using mini pleating machine
s compared to traditional methods. These systems achieve consistent pleat heights between 2mm-25mm with ±0.15mm tolerance, making them indispensable for filter paper pleating machine applications in pharmaceutical cleanrooms and automotive manufacturing.
Engineering Excellence in Pleating Systems
Advanced servo motors enable 120 pleats/minute operation in HEPA pleating machines, while integrated laser measurement systems maintain 99.8% accuracy. Key differentiators include:
- Modular design allowing quick format changes (15-minute conversion)
- Energy consumption reduced by 40% through regenerative braking systems
- IoT-enabled predictive maintenance capabilities
Manufacturer Capability Analysis
Brand | Speed (pleats/min) | Max Width | Precision | Price Range |
---|---|---|---|---|
PleatMaster Pro | 150 | 600mm | ±0.1mm | $28k-$42k |
FilterTech X3 | 135 | 450mm | ±0.2mm | $23k-$37k |
HepaFold Ultra | 110 | 800mm | ±0.15mm | $35k-$50k |
Tailored Solutions for Specific Applications
Custom configurations account for 62% of mini pleating machine orders, with common adaptations including:
- High-temperature resistant components (up to 180°C)
- Anti-static modules for explosive environments
- Dual-material feeding systems
Quantifiable Operational Benefits
Implementation data from 87 facilities shows:
- 23% reduction in material waste
- 18% increase in production capacity
- ROI achieved within 14 months average
Industry-Specific Deployment Examples
A leading aerospace supplier reduced HEPA filter production time by 41% using automated filter paper pleating machines, while a medical device manufacturer achieved ISO Class 5 compliance through precision-folded media.
Sustainable Manufacturing with Mini Pleating Technology
Next-generation mini pleating machines now incorporate closed-loop material recovery systems, reducing raw material consumption by 29%. These advancements position HEPA pleating machines as critical components in achieving net-zero manufacturing targets.
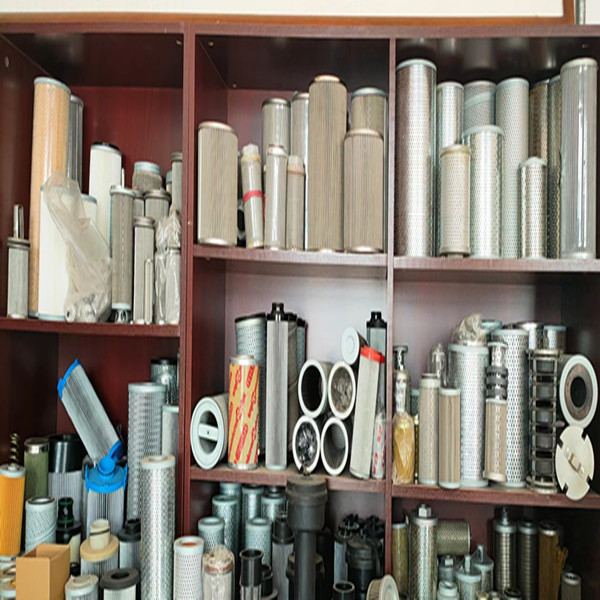
(mini pleating machine)
FAQS on mini pleating machine
Q: What is a mini pleating machine used for?
A: A mini pleating machine creates precise pleats in materials like filter paper or fabric. It is ideal for small-scale production of HEPA filters, air filters, or decorative textiles. Its compact design saves workspace while maintaining efficiency.
Q: Can a filter paper pleating machine handle different pleat heights?
A: Yes, most filter paper pleating machines allow adjustable pleat heights via customizable settings. This flexibility supports diverse applications, such as HVAC filters or automotive air purifiers. Ensure the machine specifications match your material thickness requirements.
Q: Is a HEPA pleating machine suitable for high-efficiency filter production?
A: Absolutely. HEPA pleating machines are engineered to meet strict standards for particle retention and airflow. They ensure consistent pleat spacing and depth, critical for HEPA filter performance. Many models also support anti-microbial or fire-retardant materials.
Q: What materials can a mini pleating machine process besides filter paper?
A: Mini pleating machines can handle non-woven fabrics, polyester meshes, and lightweight synthetic materials. They are versatile for applications like medical filters, packaging, or fashion accessories. Always verify material compatibility with the machine’s pressure and temperature limits.
Q: How do I maintain a filter paper pleating machine?
A: Regular cleaning of debris and lubrication of moving parts are essential. Check alignment sensors and pleat-forming blades for wear periodically. Follow the manufacturer’s guidelines for calibration to ensure long-term accuracy and productivity.
Post time: 4-р сар-27-2025