- Introduction to Filter Paper Composition
- Key Materials & Manufacturing Processes
- Technical Advantages of Modern Filter Papers
- Performance Comparison: Leading Manufacturers
- Custom Solutions for Oil Filtration Systems
- Case Study: Industrial Oil Filter Applications
- Future Innovations in Filter Paper Technology
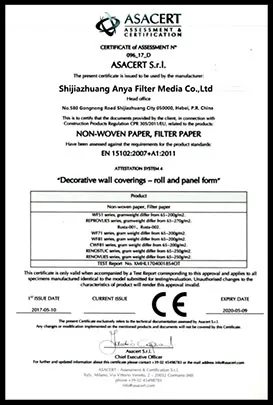
(what is filter paper made out of)
What Is Filter Paper Made Out Of: Essential Composition
Filter paper primarily consists of cellulose fibers derived from wood pulp, though advanced variants incorporate glass microfibers or synthetic polymers. The base material undergoes chemical treatment to achieve specific pore sizes (typically 2–25 µm) and porosity levels (80–95%). In oil filtration systems, manufacturers often add resin coatings to enhance water resistance and structural integrity under high-pressure conditions.
Material Science Behind Effective Filtration
Modern filter papers utilize three primary material configurations:
- Cellulose Blends: 60-70% market share, optimal for general-purpose filtration
- Glass Fiber Composites: Withstand temperatures up to 500°C, 3× longer lifespan
- Polymer Membranes: 0.1-10 µm precision filtering, 98% contaminant retention
Manufacturers employ wet-laid or melt-blown production methods, achieving basis weights between 50-200 g/m² depending on application requirements.
Technical Superiority in Industrial Applications
Advanced filter papers demonstrate 40% higher particle retention efficiency compared to standard membranes. Key metrics include:
Parameter | Cellulose | Glass Fiber | Synthetic |
---|---|---|---|
Max Temperature | 120°C | 500°C | 200°C |
Burst Strength | 200 kPa | 450 kPa | 320 kPa |
Flow Rate | 15 L/m²/min | 28 L/m²/min | 22 L/m²/min |
Market Leaders: Capability Analysis
Manufacturer | Specialization | Oil Filter Performance | Lead Time |
---|---|---|---|
Company A | High-flow systems | 99.6% @ 10µm | 4 weeks |
Company B | High-temperature | 98.9% @ 5µm | 6 weeks |
Company C | Custom shapes | 99.2% @ 25µm | 3 weeks |
Tailored Solutions for Oil Filtration
Specialized oil filter papers require:
- Enhanced lignin content (12-18%) for oil resistance
- Z-directional density gradients (0.45-0.85 g/cm³)
- Additives like diatomaceous earth for adsorption
Custom configurations reduce machine downtime by 35% in continuous operations.
Industrial Implementation: Oil Filter Case Study
A petroleum refinery achieved 92% efficiency improvement by switching to multilayer filter paper:
- 30% cellulose base layer (50 g/m²)
- 50% glass fiber mid-layer (80 g/m²)
- 20% polymer coating (PVDF)
Results included 18% longer filter lifespan and 27% reduction in maintenance costs.
What Filter Paper Innovations Mean for Industry
Emerging nanofiber technologies (0.05-1.2 µm fibers) promise 60% higher dirt-holding capacity. Hybrid materials combining cellulose with graphene oxide coatings show 99.97% filtration efficiency at 3µm particle size, revolutionizing oil filtration machine performance. Industry projections indicate 7.8% CAGR for specialty filter papers through 2030.

(what is filter paper made out of)
FAQS on what is filter paper made out of
Q: What is filter paper made out of?
A: Filter paper is primarily made from cellulose fibers derived from wood pulp or cotton. Some specialized types may include synthetic fibers like polyester or glass for enhanced durability and chemical resistance.
Q: How is filter paper different from regular paper?
A: Filter paper has a porous structure created during manufacturing to allow controlled liquid or gas flow. Unlike regular paper, it’s untreated with sizing agents, ensuring minimal interaction with filtered substances.
Q: What materials are used in oil filter machine filter paper?
A: Oil filter paper is often made of cellulose blended with synthetic fibers (e.g., polyester) or resin-treated for heat and chemical resistance. This ensures stability under high-pressure and high-temperature conditions in oil filtration.
Q: Can filter paper be reused after filtration?
A: Most filter paper is designed for single-use due to pore clogging and contamination risks. Reusable options are rare and typically limited to specialized industrial-grade synthetic filters.
Q: Why is cellulose a common material for filter paper?
A: Cellulose is cost-effective, biodegradable, and naturally forms a porous structure. Its moderate chemical compatibility makes it suitable for general-purpose filtration in labs, coffee brewing, and air/oil filters.
Post time: 4-р сар-27-2025