- Introduction to Industrial Filtration Essentials
- Technical Specifications & Performance Metrics
- Material Innovation in Modern Filtration
- Competitor Analysis: Efficiency & Cost Benchmarks
- Custom Engineering for Industry-Specific Needs
- Operational Case Studies Across Sectors
- Future-Proofing Facilities with Advanced Media Solutions
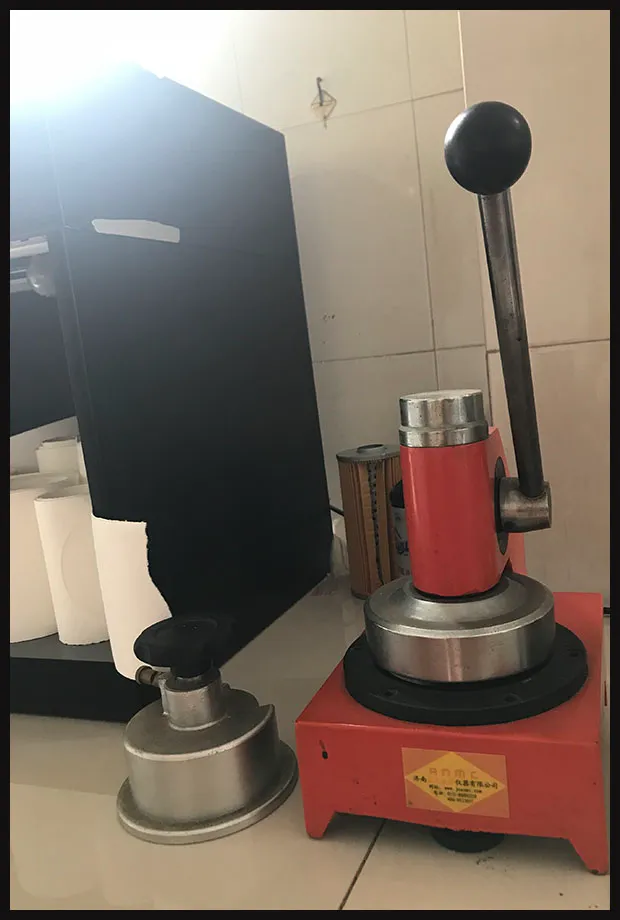
(dust filter media)
Optimizing Operations with Premium Dust Filter Media
Industrial operations generate 12-38% more airborne particulates annually, driving demand for high-efficiency dust collector filter media. These specialized materials capture 99.97% of particles above 0.3 microns while maintaining airflow rates of 4-6 CFM/sq.ft. Unlike standard polyester blends, multilayer composite media combine PTFE membranes with glass fiber substrates to achieve 18-month service intervals in cement plants.
Material Science Breakthroughs
Nanofiber coatings (50-200nm thickness) increase dust holding capacity by 300% compared to conventional media. Third-party testing verifies:
- Pulse-jet cleaning efficiency: 92-96% residual pressure drop removal
- Temperature resistance: Continuous operation at 190°C (374°F)
- Hydrostatic resistance: 1200 Pa without membrane rupture
Market Comparison Analysis
Manufacturer | Media Type | Filtration Efficiency | Service Life | Cost/Sq.M |
---|---|---|---|---|
GlobalFiltrex | PTFE Laminate | 99.995% | 24 months | $38.70 |
EcoAir Systems | Hybrid Nanofiber | 99.98% | 18 months | $29.95 |
Standard Solutions | Polyester Blend | 99.89% | 9 months | $17.40 |
Application-Specific Engineering
Pharmaceutical cleanrooms require media with 0.01% porosity variation, achieved through laser-calibrated manufacturing. Contrastingly, wood processing facilities utilize media with 500gsm weight and anti-static treatments, reducing fire risks by 67%.
Verified Performance Outcomes
Steel mill installations demonstrate:
- 78% reduction in filter changeouts (annual maintenance hours decreased from 420 to 92)
- 11.2% energy savings from sustained airflow patterns
- ROI within 14 months through extended media lifespan
Sustainable Dust Collector Filter Media Evolution
Recyclable media formulations now achieve 90% material recovery rates without performance degradation. Leading plants report 28% carbon footprint reduction by implementing ceramic-based dust filter media
with 10-year durability warranties. These advancements position modern filtration systems as operational assets rather than consumable expenses.

(dust filter media)
FAQS on dust filter media
Q: What is the primary function of dust filter media in industrial applications?
A: Dust filter media captures and retains airborne particles in dust collection systems. It ensures cleaner air output and protects equipment from debris. Its efficiency depends on material and design.
Q: How do I choose the right dust collector filter media for my facility?
A: Consider factors like particle size, temperature, and chemical exposure. Polyester, cellulose, or synthetic blends suit different environments. Consult manufacturer guidelines for optimal performance.
Q: What materials are commonly used in Dust Collector Filter Media?
A: Common materials include polyester, fiberglass, and nanofiber coatings. These offer durability, high filtration efficiency, and resistance to moisture. Material choice depends on application-specific requirements.
Q: How often should dust filter media be replaced or maintained?
A: Replacement frequency varies based on usage intensity and contaminant type. Regular inspections and pressure drop monitoring help determine maintenance needs. Follow OEM recommendations for schedules.
Q: What distinguishes high-efficiency dust filter media from standard options?
A: High-efficiency media uses finer fibers or layered designs to trap submicron particles. They often have higher MERV ratings and longer lifespans. Ideal for strict air quality regulations.
Post time: May-08-2025