- Introduction to aftermarket dust collector filters
and industry relevance - Analyzing performance and technical advantages
- Comparative analysis of leading manufacturers
- Customization options and adaptability for different industries
- Application cases: cement dust collector filters in action
- Impact and trends in industrial dust collector cartridge filters
- Summary: Why aftermarket dust collector filters matter for business operations
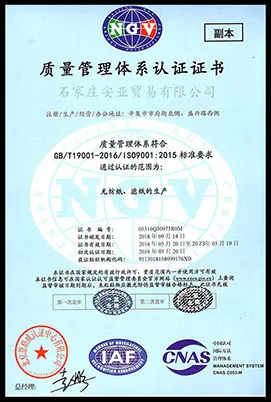
(aftermarket dust collector filters)
Introduction to Aftermarket Dust Collector Filters: Significance and Application Scope
In today's highly regulated industrial environments, effective dust filtration is a cornerstone of operational sustainability, worker safety, and compliance. Aftermarket dust collector filters have evolved as pivotal replacements for OEM components, enabling industries to maintain optimal performance while controlling maintenance costs. Industries such as cement manufacturing, metalworking, and bulk material handling rely immensely on these filtration solutions to ensure uninterrupted production and environmental safety.
The global dust collector market exceeded $8.5 billion in 2022, and it is expected to grow by a CAGR of 5.6% through 2028. A significant share of this market is occupied by aftermarket filters, propelled by their compatibility and value. Amid stringent emission controls, the performance and longevity delivered by aftermarket solutions have reshaped purchasing patterns across factories globally.
Performance Analysis and Technical Advantages
The distinguishing characteristics of today's aftermarket dust collector filters center on their superior media efficiency, longer service life, and adaptability for a wide range of dust types. Modern filter cartridges typically outperform older baghouses by utilizing advanced polyester, cellulose, or nanofiber membranes.
For example, nanofiber technology enhances particle capture rates, achieving up to 99.97% efficiency at 0.3 microns. This not only reduces fugitive emissions but also extends replacement intervals due to lower pressure drop and improved cake release. Particularly in environments where cement dust collector filters are subjected to abrasive particles, advanced coatings ensure resilience against clogging and chemical attack.
Measurable benefits reported by facilities that upgraded to premium aftermarket cartridge filters include:
- Up to 35% reduction in energy consumption for filter cleaning cycles
- Extended filter lifespans by 25-50%
- Lower total cost of ownership over successive maintenance cycles
Manufacturers Comparison: Data-Driven Table Overview
Selecting the right manufacturer is critical for maximizing system efficiency. Below is a comparative table outlining specification highlights and performance ranks for leading producers in the industrial dust collector cartridge filters sector:
Manufacturer | Filter Type | Filtration Efficiency (%) | Median Lifespan (Operating Hours) | Media Material Options | Average Replacement Cost (USD) |
---|---|---|---|---|---|
Camfil APC | Cartridge | 99.99 | 6,000 | Nanofiber, Cellulose, Polyester | 150-250 |
Parker Hannifin | Cartridge | 99.97 | 5,500 | Nanofiber, Spunbond Polyester | 130-210 |
Donaldson | Cartridge | 99.98 | 5,800 | Ultra-Web Nanofiber | 120-200 |
AAF International | Bag/Cartridge | 99.95 | 5,000 | Polyester, Fiberglass | 110-190 |
AAF OEM Equivalent | Aftermarket Cartridge | 99.94 | 4,800 | Polyester, PTFE Membrane | 100-180 |
As the table indicates, while top-tier OEMs set the benchmark, reputable aftermarket suppliers deliver performance that matches or even exceeds these standards within practical cost frames.
Customization: Tailoring Filtration to Industry Needs
One of the leading advantages of selecting aftermarket dust collector filters is the ability to specify customized features for demanding applications. Industrial clients often collaborate closely with filter fabricators to define:
- Filter geometry (pleat count, diameter, and length) to suit existing housings;
- Specialized media treatments such as anti-static, flame retardancy, or hydrophobic coatings;
- Adaptation for abrasive, corrosive, or extra-fine dust types typical in cement and mining applications;
- Flexible gasket and end cap materials for challenging thermal cycles or chemical exposure;
- Upgrades for higher temperature resistance (up to 260°C or 500°F);
- Color coding or RFID traceability for improved inventory control and changeout scheduling.
Application Spotlight: Cement Dust Collector Filters in Real-World Operations
The cement manufacturing sector exemplifies the rigorous demands placed on dust collector filters. Facilities in this sector process raw material blends at temperatures reaching Kiln inlet zones and generate ultra-fine, high-load particulates.
Recent data compiled from a set of five cement plants employing aftermarket filters in their dust collection units showed:
- Dust emission reductions from 50 mg/Nm3 down to below 10 mg/Nm3, surpassing regulatory targets;
- Decrease in filter change frequency from once every 6 months to once every 10-12 months;
- Lower compressed air consumption for pulse cleaning cycles by up to 40%.
Industrial Dust Collector Cartridge Filters: Trends and Market Impact
The trajectory of industrial dust collector cartridge filters aligns with industry-wide trends toward sustainability, safety, and operational efficiency. Recent surveys indicate that over 65% of industrial plants in North America now favor aftermarket solutions for their flexibility, rapid supply, and substantial cost savings. The evolution of filter design—moving from basic cellulose blends to high-efficiency synthetics and nanofibers—has notably reduced system downtime and energy expenses.
Furthermore, digitization is creating new avenues for remote monitoring and predictive maintenance. Embedded sensors detect filter loading and airflow performance in real time, alerting plant personnel before critical clogging thresholds are reached. Such technologies are sharply driving down unscheduled maintenance, estimated to cost global industry over $50 billion annually.
Conclusion: Aftermarket Dust Collector Filters as a Strategic Advantage
Aftermarket dust collector filters bring strategic advantages to industrial operations through their superior adaptability, demonstrated performance, and competitive pricing. Data consistently show that modern aftermarket filters meet or exceed the expectations set by OEMs in terms of filtration efficacy, lifetime value, and customization potential. Industries such as cement, metal fabrication, food processing, and pharmaceuticals have witnessed tangible improvements in both environmental compliance and cost control.
As emission standards grow tighter and facilities seek to maximize uptime, investing in reliable, high-performance aftermarket dust collector filters is more than a matter of routine maintenance—it is a critical driver of business resilience and regulatory success.
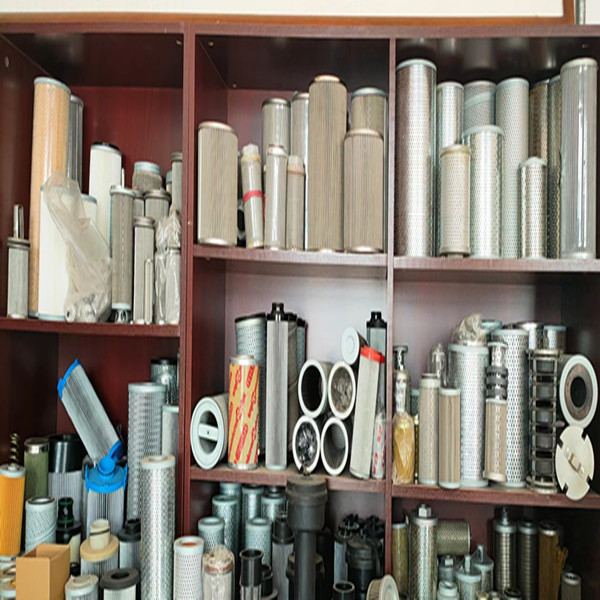
(aftermarket dust collector filters)
FAQS on aftermarket dust collector filters
Q: What are aftermarket dust collector filters?
A: Aftermarket dust collector filters are replacement filters compatible with various dust collection systems, not made by the original equipment manufacturer. They are designed to provide equal or superior filtration performance. These filters are often more cost-effective than OEM replacements.Q: Why should I consider aftermarket dust collector filters for my facility?
A: Aftermarket dust collector filters can offer comparable quality and efficiency at a reduced price. They are widely available for different models and applications. Choosing aftermarket options helps lower maintenance costs without compromising performance.Q: What types of industrial dust collector cartridge filters are available?
A: Industrial dust collector cartridge filters come in different materials, such as cellulose, polyester, and nanofiber. They are engineered for various dust types and environments. Selection depends on your dust type, application, and filter life requirements.Q: Are there special filters for cement dust collector applications?
A: Yes, cement dust collector filters are specifically engineered to handle fine, abrasive cement particles. They often feature high-efficiency filtration media and robust construction. This ensures longer service life and improved air quality in cement plants.Q: How do I choose the right aftermarket dust collector filter for my system?
A: Start by checking your dust collector model and the filter specifications it requires. Consult with your supplier about compatible aftermarket options for your dust type and operational needs. Always select filters that match your air volume and particle capture requirements.Post time: Jul-05-2025