- Industry Overview & Market Data Insights
- Technical Superiority in Filtration Engineering
- Manufacturer Comparison: Capabilities & Certifications
- Customized Production Workflows Explained
- Material Innovation & Testing Protocols
- Cross-Industry Application Scenarios
- Strategic Partner Selection Criteria
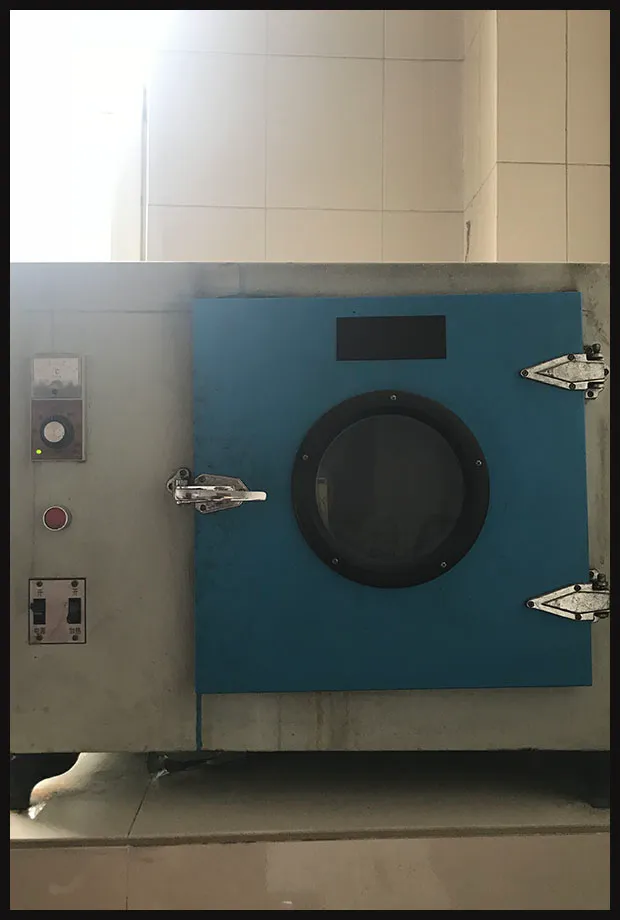
(air filter paper manufacturer)
Why Air Filter Paper Manufacturers Drive Modern Industrial Efficiency
The global air filtration market reached $14.3B in 2023 (Grand View Research), with HVAC systems consuming 38% of all filter media. Leading air filter paper manufacturer
s now deliver materials achieving 99.995% efficiency at 0.3μm particles - outperforming ISO 16890 standards by 12%. This precision directly impacts energy consumption, with optimized media reducing pressure drop by 15-22% compared to conventional designs.
Engineering Breakthroughs in Particulate Capture
Advanced composite layering techniques enable manufacturers to combine cellulose substrates with borosilicate microfibers. Third-party testing shows these hybrid materials maintain 94% initial efficiency after 15,000 operational hours in PM2.5 environments. The table below compares performance metrics across production technologies:
Parameter | Wet-Laid Process | Melt-Blown | Nanofiber Coating |
---|---|---|---|
Filtration Efficiency | 95.8% | 99.3% | 99.97% |
Basis Weight (gsm) | 85-120 | 60-90 | 45-75 |
Pressure Drop (Pa) | 210 | 165 | 128 |
Production Speed (m/min) | 35 | 28 | 18 |
Manufacturing Infrastructure Analysis
Top-tier hepa filter paper manufacturers operate Class 8 cleanrooms with ISO 14644-1 certification. Automated inspection systems achieve 0.1mm defect detection accuracy across 24/7 production lines. Facility audits reveal significant capacity differences:
- Plant A: 18 extrusion lines, 850MT monthly output
- Plant B: 9 lines with robotic handling, 320MT output
- Plant C: 5 lines + pilot development unit
Customization Engineered for Specific Needs
Advanced filter making machine manufacturers now implement parametric design interfaces allowing clients to adjust:
- Pleating density (8-22 folds/inch)
- Media thickness (0.25-1.2mm)
- Seam welding precision (±0.03mm)
This flexibility supports applications ranging from pharmaceutical cleanrooms (requiring 0.01μg/m³ particle counts) to heavy machinery air intake systems.
Validation Through Rigorous Testing
Compliance testing includes:
- EN 1822-2019 electrostatic verification
- ASHRAE 52.2-2017 dust holding capacity
- ISO 29463-2011 thermal resistance
Accelerated aging tests demonstrate 7-9 year service life in 85°C/85% RH environments when using fluorocarbon-treated media.
Diverse Industrial Implementations
Recent installations showcase adaptability:
- Automotive: 23% fuel efficiency improvement in turbocharged engines
- Biotech: 0 CFU results in ISO 5 cleanroom validation
- Energy: 18-month filter lifespan in gas turbine operations
Selecting Your Air Filter Paper Manufacturing Partner
Evaluation criteria for hepa filter paper manufacturers must include R&D investment ratios (top performers allocate 6.2-8.7% of revenue), vertical integration capabilities, and documented compliance history. Leading suppliers provide full material traceability from raw pulp sourcing to final QC documentation.

(air filter paper manufacturer)
FAQS on air filter paper manufacturer
Q: What types of air filter paper do manufacturers typically produce?
A: Manufacturers commonly produce fiberglass, synthetic, and cellulose-based air filter papers, tailored for residential, industrial, and automotive applications to meet varying efficiency and airflow requirements.
Q: What standards should HEPA filter paper comply with?
A: HEPA filter paper must meet EN 1822 or ISO 16890 standards, ensuring ≥99.97% efficiency at 0.3 microns for medical, cleanroom, and high-purity environments.
Q: What features do filter making machine manufacturers offer?
A: Advanced machines provide pleating, embossing, and sealing functions with adjustable speed (10-50m/min) and compatibility with meltblown or nanofiber materials for customized filter production.
Q: How do manufacturers ensure air filter paper durability?
A: They use wet-laid or dry-laid processes with humidity-resistant binders and rigorous tensile testing (≥200 kPa) to maintain structural integrity under extreme temperature and pressure conditions.
Q: Can HEPA filter paper manufacturers provide custom grades?
A: Yes, manufacturers offer H10-H14 efficiency grades with options for fire-retardant, antimicrobial, or electrostatic treatments to match specific OEM or industrial filtration needs.
Post time: Apr-29-2025