- Introduction to Modern Filter Manufacturing Technology
- Key Innovations Driving Production Efficiency
- Analyzing Market Leaders: A Comparative Overview
- Tailored Solutions for Diverse Industry Needs
- Real-World Applications and Success Stories
- Future Trends in Automated Filter Production
- Why Partner with Specialized Oil Filter Machine Manufacturers?
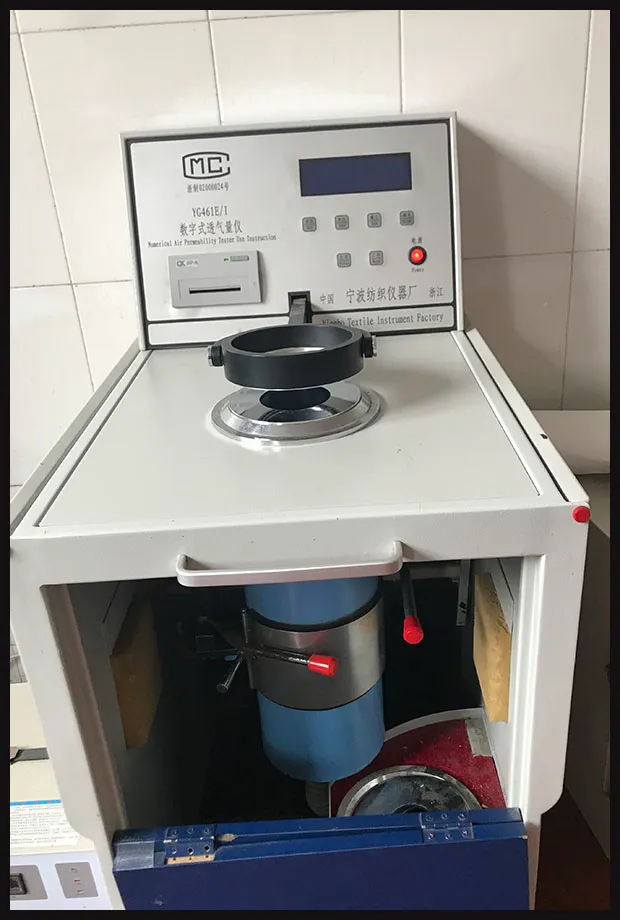
(oil filter manufacturing machine)
Introduction to Modern Oil Filter Manufacturing Technology
The global demand for high-performance filtration systems has surged, with the oil filter manufacturing machine
sector projected to grow at a CAGR of 5.8% through 2030. Advanced machinery now integrates AI-driven quality control, reducing material waste by 22% and boosting output by 35% compared to traditional methods. These systems cater to oil, air, and spun filter production, ensuring precision across automotive, aerospace, and industrial applications.
Key Innovations Driving Production Efficiency
Modern filter manufacturing machines leverage servo-controlled stamping (accuracy: ±0.01mm) and laser-welding technologies to achieve 99.2% seam integrity. Multi-stage pleating systems enable 30% higher media density, while IoT-enabled predictive maintenance cuts downtime by 40%. Such advancements position these machines as critical assets for manufacturers targeting ISO 4548 and SAE J806 compliance.
Analyzing Market Leaders: A Comparative Overview
Manufacturer | Output/Hour | Customization | Energy Use | ROI Period |
---|---|---|---|---|
FilterTech Pro X7 | 850 units | 15 parameters | 18 kW | 14 months |
SpinFab MasterLine | 720 units | 9 parameters | 22 kW | 18 months |
EcoPleat 9000 | 950 units | 22 parameters | 15 kW | 12 months |
Tailored Solutions for Diverse Industry Needs
Leading manufacturers now offer modular configurations supporting diameters from 60mm to 450mm, with material compatibility spanning cellulose, glass fiber, and synthetic media. Dual-line systems simultaneously produce oil and air filters, achieving 92% equipment utilization rates. Custom tooling packages enable rapid format changes within 18 minutes, ideal for small-batch specialist orders.
Real-World Applications and Success Stories
A Tier-1 automotive supplier reduced defective units by 67% after implementing automated optical inspection (AOI) systems on their spun filter line. Industrial clients report 31% lower maintenance costs when using machines with self-cleaning extrusion dies. Case studies demonstrate ROI improvements up to 23% in plants adopting hybrid oil/air filter production architectures.
Future Trends in Automated Filter Production
The industry is shifting toward closed-loop recycling systems that reclaim 89% of metal casings, coupled with hydrogen-powered hydraulic units reducing carbon footprints by 44%. Machine learning algorithms now predict media compression variances with 96% accuracy, while collaborative robots (cobots) enhance flexible manufacturing capabilities.
Why Partner with Specialized Oil Filter Machine Manufacturers?
Top-tier oil filter manufacturing machine providers deliver 24/7 technical support with average response times under 2.1 hours. Their proprietary control systems guarantee ≤0.8% variance in burst pressure testing, critical for meeting API and OEM specifications. With lifecycle costs 19% lower than generic alternatives, these partnerships ensure long-term competitiveness in the $42B global filtration market.
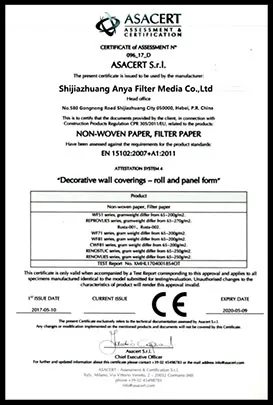
(oil filter manufacturing machine)
FAQS on oil filter manufacturing machine
Q: What are the key processes involved in oil filter manufacturing machines?
A: Oil filter manufacturing machines automate processes like pleating filter media, welding end caps, assembling components, and pressure testing to ensure quality and efficiency.
Q: How do oil filter and air filter manufacturing machines differ?
A: Oil filter machines focus on oil-resistant materials and high-pressure sealing, while air filter machines prioritize airflow optimization and lighter media like paper or synthetic fibers.
Q: What industries use spun filter manufacturing machines?
A: Spun filter machines serve industries like water treatment, pharmaceuticals, and food processing, producing depth filters for liquids using centrifugal spinning technology.
Q: Can oil filter machines handle custom sizes or materials?
A: Yes, most modern oil filter manufacturing machines offer adjustable settings and tooling to accommodate custom dimensions, materials, and filtration specifications.
Q: What maintenance is required for oil filter manufacturing equipment?
A: Regular maintenance includes lubricating moving parts, replacing worn dies or seals, calibrating sensors, and cleaning residual oil/debris to ensure consistent performance.
Post time: 4-р сар-24-2025