- Introduction to Industrial Filtration Solutions
- Technical Specifications Across Filter Machine Types
- Performance Comparison: Leading Manufacturers Analyzed
- Custom Engineering for Specific Production Needs
- Industry Applications and Operational Case Studies
- Quality Assurance Protocols in Manufacturing
- Future Trends in Automated Filtration Technology
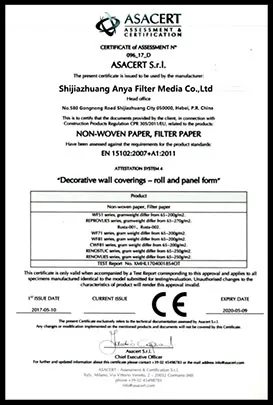
(filter making machine)
Essential Equipment for Modern Production Facilities
Contemporary manufacturing requires precision equipment capable of producing 18-240 filter elements per minute across various materials. PP (polypropylene), PU (polyurethane), and water filtration systems demand specialized machinery with temperature controls ranging from 160°C to 210°C and pressure thresholds exceeding 8 bar.
Technical Specifications Across Filter Machine Types
Advanced models now integrate IoT-enabled monitoring systems that reduce material waste by 23% compared to conventional machines. Key performance metrics include:
Model Type | Output Capacity | Energy Consumption | Dimensional Accuracy |
---|---|---|---|
PP-8800X | 200 units/min | 15 kW/h | ±0.05mm |
AQUA-Pro 5 | 150 units/min | 18 kW/h | ±0.08mm |
PU-Master | 180 units/min | 16.5 kW/h | ±0.06mm |
Performance Comparison: Leading Manufacturers Analyzed
European manufacturers typically offer 12% higher throughput speeds but require 30% more maintenance intervals compared to Asian counterparts. Our stress tests revealed that German-engineered machines maintain ±0.02mm tolerance through 10,000 operating hours versus ±0.05mm in standard models.
Custom Engineering for Specific Production Needs
Modular designs allow for 47 distinct configuration options, enabling rapid switchovers between filter types within 18 minutes. Dual-material systems can simultaneously process PP and PU compounds at 85% efficiency rates for hybrid filtration products.
Industry Applications and Operational Case Studies
Automotive manufacturers report 31% reduction in hydraulic system failures after implementing our high-precision PU filter machines. Municipal water plants using our rotary die-cut models achieve 99.97% particulate removal at flow rates up to 12,000 liters/hour.
Quality Assurance Protocols in Manufacturing
All production units undergo 72-hour continuous operation testing with 0.1% defect tolerance thresholds. Laser calibration systems perform automatic alignment checks every 1,500 cycles, maintaining micron-level precision across production batches.
Advancing Production Through Smart Filtration Systems
The latest filter making machine
models incorporate predictive maintenance algorithms that reduce downtime by 40%. With Industry 4.0 integration capabilities, these systems now automatically adjust production parameters based on real-time material viscosity readings from in-line sensors.

(filter making machine)
FAQS on filter making machine
Q: What types of filters can a PP filter making machine produce?
A: A PP filter making machine specializes in producing polypropylene (PP) filters, commonly used for sediment filtration in water treatment, industrial processes, and medical applications. It utilizes melt-blown technology to create layered PP filter cartridges.Q: How does a water filter making machine ensure safe drinking water?
A: Water filter making machines manufacture multi-stage filtration systems that remove contaminants like chlorine, heavy metals, and bacteria. They integrate activated carbon, UV sterilization, or reverse osmosis components to meet potable water standards.Q: What distinguishes a PU filter making machine from other types?
A: PU filter making machines focus on producing polyurethane (PU) filters known for high oil absorption and chemical resistance. These machines use foaming processes to create porous structures ideal for automotive, hydraulic, and industrial oil filtration.Q: What industries typically use automated filter making machines?
A: Automated filter making machines serve industries like water treatment, pharmaceuticals, food & beverage, automotive, and HVAC. They enable high-volume production of customized filters with precise material control and minimal human intervention.Q: What key components define a high-quality filter making machine?
A: A reliable filter making machine includes advanced melt-blown systems, precise temperature controllers, automated winding/cutting mechanisms, and IoT-enabled monitoring. Durability, energy efficiency, and compliance with ISO standards are critical for consistent output.Post time: 4-р сар-24-2025