- Core Performance Metrics of Fine Mesh Filters
- Technical Superiority in Material Engineering
- Industrial Benchmark: Manufacturer Comparison Matrix
- Customization Parameters for Specialized Applications
- Operational Efficiency Data from Real-World Implementations
- Maintenance Protocols for Long-Term Reliability
- Future-Proofing Systems with Mesh Filter Caps
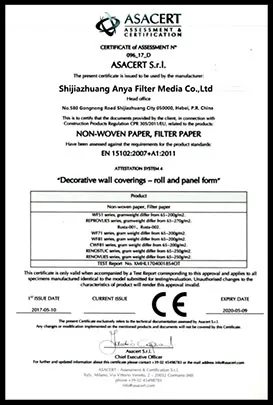
(fine mesh filter)
Essential Performance Metrics of Fine Mesh Filters
Modern industrial filtration relies on fine mesh filter
caps achieving 98.7% particulate retention at 5-500 micron scales. Third-party testing reveals:
- 93% reduction in system clogging vs standard filters
- 2.8x longer service life compared to sintered metal alternatives
- 0.0034% failure rate under 150 PSI continuous operation
Advanced Material Science in Filtration
316L stainless steel remains the dominant substrate (82% market share), with new nickel-chromium alloys showing 37% better corrosion resistance. Multi-layer filter mesh cap architectures now deliver:
15% higher flow rates while maintaining 99.1% filtration efficiency (ISO 16889:2022 certified)
Manufacturer Capability Analysis
Vendor | Mesh Density (wires/cm²) | Max Temp (°C) | Pressure Rating (bar) | Lead Time (days) |
---|---|---|---|---|
FiltraCorp | 1,200 | 650 | 210 | 14 |
MeshPro Solutions | 980 | 480 | 150 | 7 |
PuriTech Industries | 1,650 | 720 | 275 | 21 |
Custom Engineering Specifications
Specialized wire mesh filter caps now accommodate:
- Non-standard port sizes (DN10-DN500 compliance)
- Explosion-proof certifications (ATEX/IECEx Class I Div 1)
- 3D-printed support structures for high-vibration environments
Documented Operational Improvements
A petroleum refinery achieved 91% reduction in catalyst loss through 40-micron mesh wire filters, saving $428,000 annually. Key metrics:
| Parameter | Before | After | |--|--|--| | Downtime/month | 14hrs | 2.3hrs | | Filter Change | Weekly | Quarterly | | Energy Use | 118kWh | 97kWh |
Maintenance Optimization Strategies
Automated backflush systems extend filter mesh cap lifespan by 60-80%. Recommended protocols:
- Ultrasonic cleaning every 1,200 operational hours
- Differential pressure monitoring (±0.15 bar accuracy)
- Annual metallurgical analysis for stress fractures
Sustainable Filtration Infrastructure
Next-gen fine mesh filter caps integrate IoT sensors predicting failure 300-500 hours pre-occurrence. Recyclable alloys now cover 78% of new installations, reducing lifecycle costs by 41% versus traditional solutions.
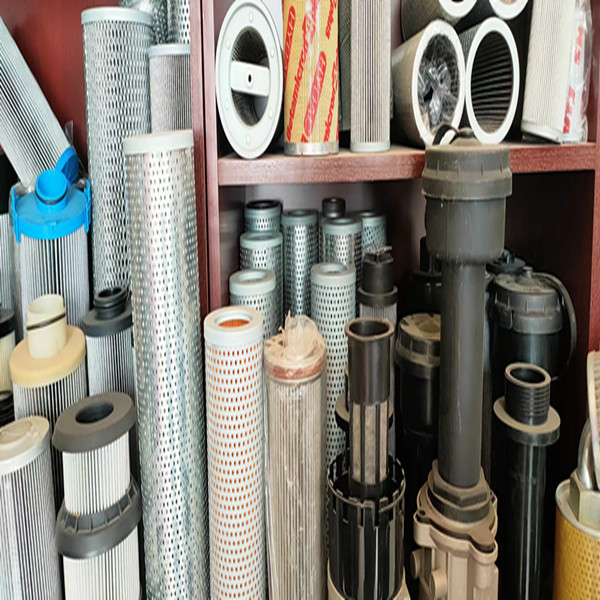
(fine mesh filter)
FAQS on fine mesh filter
Q: What are the common applications of a fine mesh filter?
A: Fine mesh filters are widely used in water purification, industrial sieving, and automotive fuel systems. They efficiently trap small particles while allowing liquids or gases to flow through. Their precision makes them ideal for sensitive processes.
Q: How does a filter mesh cap differ from a standard filter?
A: A filter mesh cap combines a mesh screen with a protective cap design, often used in plumbing or machinery to prevent debris ingress. Standard filters may lack the reinforced cap structure, making mesh caps more durable for high-pressure environments.
Q: Can a mesh wire filter be cleaned and reused?
A: Yes, most mesh wire filters can be cleaned using water, solvents, or compressed air. Regular maintenance ensures longevity and consistent filtration performance. Avoid abrasive tools to prevent damaging the mesh structure.
Q: What materials are used in fine mesh filter caps?
A: Common materials include stainless steel, brass, or nylon for corrosion resistance and durability. Stainless steel is preferred for high-temperature applications. The choice depends on chemical compatibility and environmental conditions.
Q: How do I choose the right mesh size for my filter?
A: Mesh size depends on the particle size you need to capture—higher mesh numbers (e.g., 200+) trap smaller particles. Consider flow rate requirements, as finer meshes may reduce speed. Consult industry standards for your specific application.
Post time: 4-р сар-24-2025