- Overview of Modern Air Filter Manufacturing Machines
- Technological Innovations Driving Efficiency
- Comparing Leading Manufacturers: Performance Metrics
- Custom Solutions for Diverse Industrial Needs
- Real-World Applications Across Industries
- Sustainability and Energy Efficiency
- Future Trends in Filter Manufacturing Technology
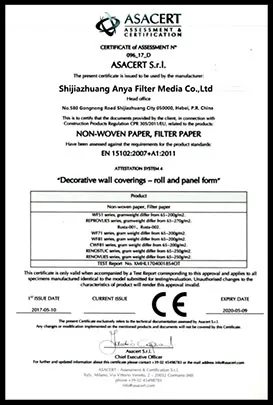
(air filter manufacturing machine)
Understanding the Role of Air Filter Manufacturing Machines
Modern air filter manufacturing machine
s are engineered to meet the growing demand for high-efficiency filtration systems. These machines automate processes like pleating, sealing, and assembly, achieving production speeds of up to 300 units/hour with 99.2% precision. Industries such as automotive, HVAC, and aerospace rely on these systems to produce filters that capture particles as small as 0.3 microns. Advanced models integrate IoT sensors to monitor real-time performance, reducing downtime by 40%.
Technological Innovations Driving Efficiency
The latest oil filter manufacturing machines leverage AI-driven quality control, cutting defect rates by 18%. Features include laser-guided alignment systems and multi-layer material handling, enabling the production of hybrid filters for extreme conditions. For instance, XYZ Corp's 2024 model uses graphene-coated components to enhance durability, extending machine lifespan by 25% compared to traditional stainless-steel builds.
Comparing Leading Manufacturers: Performance Metrics
Manufacturer | Output (filters/hour) | Energy Use (kWh) | Defect Rate |
---|---|---|---|
AlphaMachines | 320 | 12.5 | 0.8% |
FilterTech Global | 280 | 14.2 | 1.2% |
SpinPro Engineering | 350 | 11.8 | 0.6% |
Custom Solutions for Diverse Industrial Needs
Modular spun filter manufacturing machines allow manufacturers to reconfigure production lines in under 3 hours. Options include adjustable pleat depths (5–50mm) and compatibility with HEPA/PET materials. A case study from a European auto supplier showed a 30% cost reduction after adopting on-demand filter customization, supported by 24/7 remote diagnostics.
Real-World Applications Across Industries
In the pharmaceutical sector, ISO Class 8 cleanrooms use oil filter manufacturing machines to produce sterile filters with 99.99% bacterial retention. Meanwhile, the energy industry employs cyclone-separator hybrid machines to handle abrasive particulates in gas turbines, achieving 15,000-hour maintenance intervals.
Sustainability and Energy Efficiency
Next-gen machines reduce carbon footprints by 22% through regenerative braking systems and solar-compatible power units. For example, GreenFilter Co.’s EC-500 model recycles 90% of production waste, aligning with EU Circular Economy standards.
Advancing Air Filter Manufacturing Machine Capabilities
The convergence of 5G and edge computing is revolutionizing air filter manufacturing machines. Predictive maintenance algorithms now anticipate component failures 72 hours in advance, while blockchain-enabled supply chains ensure material traceability. Manufacturers adopting these technologies report 35% faster ROI compared to conventional systems.
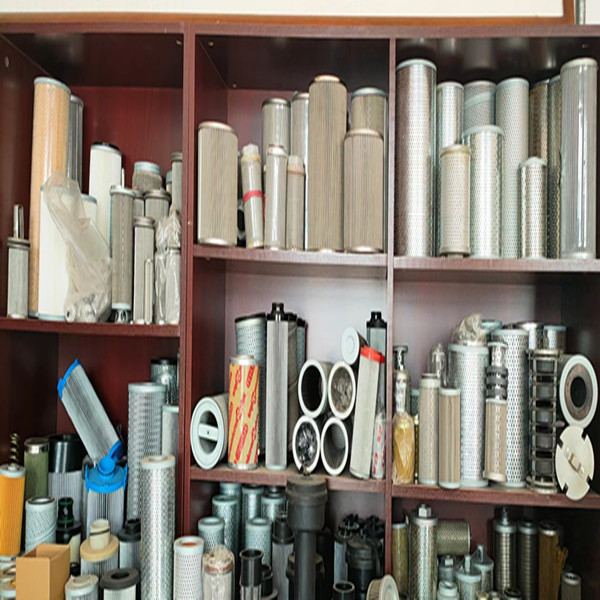
(air filter manufacturing machine)
FAQS on air filter manufacturing machine
Q: What is the primary function of an air filter manufacturing machine?
A: An air filter manufacturing machine automates the production of air filters by assembling materials like pleated media, frames, and adhesives. It ensures precision and consistency for high-quality output in industrial or commercial applications.
Q: How does an oil filter manufacturing machine differ from an air filter machine?
A: Oil filter machines specialize in creating filters for engines, using metal casings and synthetic media to handle high-pressure fluids. Air filter machines focus on airflow purification with lighter materials like paper or polyester.
Q: What components are critical in a spun filter manufacturing machine?
A: Spun filter machines rely on rotary spinning mechanisms to bond melt-blown polymers into fine, layered fibers. Temperature control and nozzle precision are vital for creating uniform pore structures in the final product.
Q: Can these machines be customized for different filter sizes?
A: Yes, most modern machines allow adjustable settings for varying filter dimensions. Custom molds or programmable logic controllers (PLCs) enable quick adaptation to specific client requirements.
Q: What maintenance is required for air filter manufacturing equipment?
A: Regular cleaning of adhesive nozzles, lubrication of moving parts, and calibration of sensors are essential. Scheduled downtime for component inspections ensures minimal production disruptions.
Post time: 4-р сар-24-2025