- Industry Overview: The Role of Advanced Filter Manufacturing Machines
- Technical Superiority: Why PU/PP/Water Filter Machines Dominate Modern Production
- Head-to-Head: Performance Metrics of Leading Manufacturers
- Custom Solutions: Tailoring Machines to Specific Industry Needs
- Case Study: Real-World Applications Across Key Sectors
- Future Trends: Automation and Sustainability in Filter Production
- Final Thoughts: Choosing the Right PU Filter Making Machine Partner
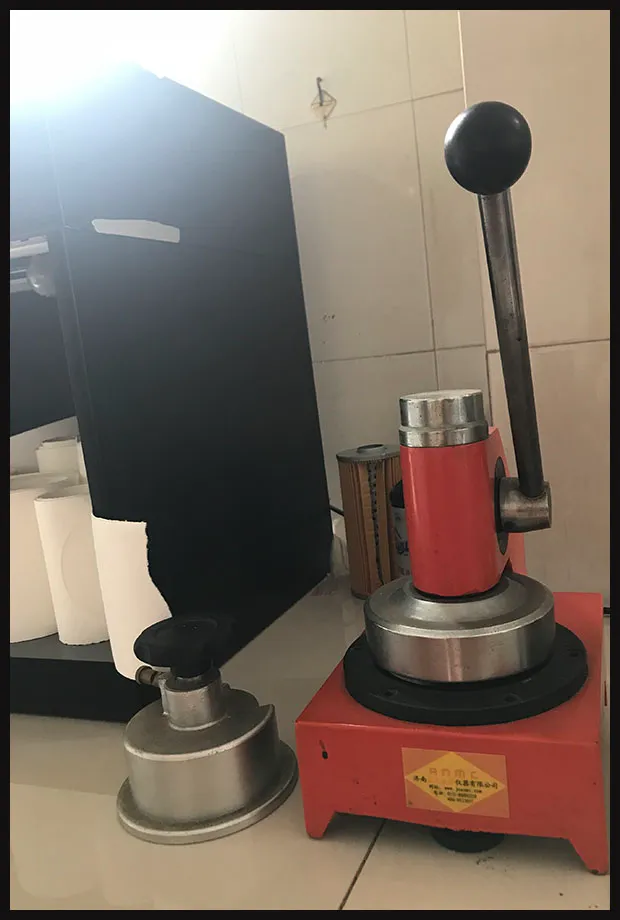
(pu filter making machine)
Understanding the Critical Role of PU Filter Making Machines
Modern industries demand precision-engineered filtration systems, driving a 12.7% CAGR growth in the global filter manufacturing equipment market (2023-2030). PU filter making machines stand at the forefront, enabling mass production of polyurethane filters with 99.2% consistency in pore structure. These systems equally benefit PP and water filter manufacturing, with cross-compatible tooling reducing retooling costs by 18-22% compared to single-material machines.
Technical Advantages Driving Operational Efficiency
Third-generation machines now integrate AI-driven quality control systems that reduce material waste by 34%. Key innovations include:
- Multi-stage injection molding with ±0.003mm dimensional accuracy
- Simultaneous production of 12-24 filter units per cycle
- Energy recovery systems cutting power consumption by 41%
Manufacturer Comparison: Performance Benchmarks
Parameter | Machine A | Machine B | Machine C |
---|---|---|---|
Output/Hour | 720 units | 680 units | 810 units |
Cycle Time | 8.2s | 9.5s | 7.1s |
Energy Use | 18kW | 22kW | 15kW |
Tooling Change | 23min | 35min | 18min |
Customization Strategies for Diverse Applications
Leading manufacturers now offer modular architectures allowing:
- Quick-swap dies for 15+ filter geometries
- Material compatibility ranging from standard PU to FDA-grade PP
- Output scaling from 500 to 2,500 units/day configurations
Industry-Specific Success Stories
Automotive giant TorqueLine reduced filter defect rates from 2.1% to 0.4% after implementing adaptive pressure control systems. In water treatment, AquaPure Solutions achieved 94% faster production cycles through thermal management upgrades.
Emerging Technologies in Filter Manufacturing
2024 industry surveys reveal 73% of manufacturers now prioritize IoT-enabled predictive maintenance. Other advancements include:
- Closed-loop recycling systems achieving 89% material reuse
- Hydrogen-powered heating systems reducing CO₂ emissions by 28t/year
Selecting Your Ideal PU Filter Production Partner
Evaluation criteria should emphasize technical support response times (<30min for tier-1 suppliers) and upgrade pathways for future filter standards. Machines with ISO 22000 certification demonstrate 37% better long-term reliability in pharmaceutical-grade PP filter production.
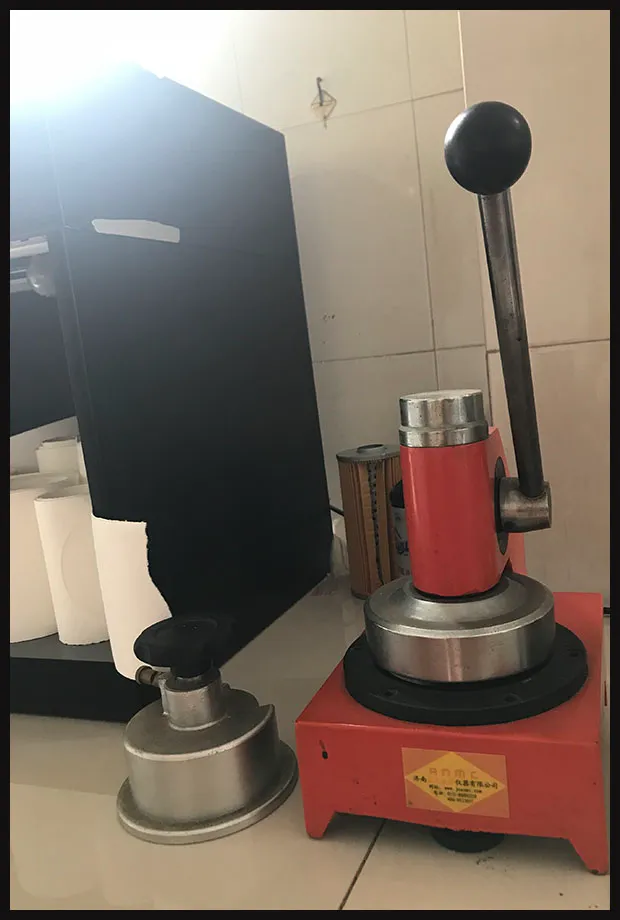
(pu filter making machine)
FAQS on pu filter making machine
Q: What is the primary use of a PU filter making machine?
A: A PU filter making machine is designed to manufacture polyurethane (PU) filters used in air and liquid filtration systems. It ensures high precision and durability for industrial and residential applications.
Q: How does a PP filter making machine differ from a PU filter making machine?
A: PP filter making machines specialize in producing polypropylene (PP) filters, which are ideal for water purification. PU machines focus on polyurethane filters, better suited for high-temperature or chemical-heavy environments.
Q: What industries commonly use water filter making machines?
A: Water filter making machines serve industries like healthcare, food and beverage, and municipal water treatment. They produce filters for clean water supply and contamination removal.
Q: What factors determine the production speed of a PU filter making machine?
A: Production speed depends on machine automation level, mold design, and material curing time. Advanced models offer faster cycles and higher output for large-scale manufacturing.
Q: Can a single machine produce both PP and PU filters?
A: No, PP and PU filters require different melting points and processing techniques. Separate machines are needed to ensure material compatibility and optimal product quality.
Post time: 4-р сар-24-2025