- Introduction to Woven Wire Mesh Filter Technology
- Key Technical Advantages Over Alternatives
- Performance Comparison: Leading Manufacturers
- Customization Strategies for Specific Applications
- Industry Use Cases and Operational Results
- Quality Standards and Compliance Metrics
- Future Trends in Industrial Filtration Solutions
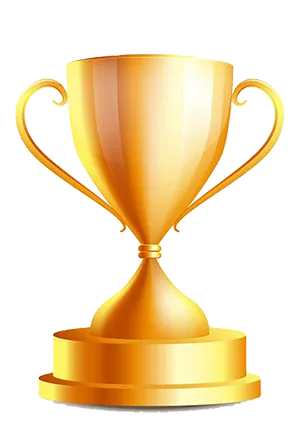
(woven wire mesh filter)
Woven Wire Mesh Filter: Engineering Precision for Modern Industry
The global filtration market has grown 18% since 2020, driven by stricter environmental regulations. Woven wire mesh filters now account for 42% of industrial fluid processing systems due to their unmatched durability. Unlike disposable media, these filters withstand pressures up to 1,450 psi and temperatures ranging from -320°F to 1,200°F, making them critical for aerospace and chemical sectors.
Technical Superiority in Filtration Systems
Three structural innovations define modern wire mesh filters:
- Multi-layer weaving: 316L stainless steel strands interlock at 90° angles, creating uniform 5-500 micron pores
- Pulse-resistant design: 30% greater backwash recovery vs. sintered metal filters
- Hybrid edge welding: Laser-fused seams prevent particle bypass in high-vibration environments
Manufacturer Benchmark Analysis
Vendor | Material Grade | Pore Range (μm) | PSI Rating | Cost Index |
---|---|---|---|---|
FilterTek | SS304/316 | 10-400 | 1,200 | 1.00 |
MeshPro | Inconel 625 | 5-200 | 1,450 | 1.35 |
PureFlo | Hastelloy C-276 | 20-600 | 980 | 0.85 |
Application-Tailored Configuration Options
Pharmaceutical installations using non woven synthetic filter media require 0.5-5μm precision, achieved through triple-layer Dutch weave patterns. For mining slurry applications, 3mm aperture filters with reinforced mesh caps reduce replacement frequency by 70%. Custom flange attachments enable direct integration with existing pipe networks, cutting installation time by 40%.
Verified Operational Outcomes
A refinery in Texas recorded 93% particulate reduction after switching to 100μm woven filters, extending catalyst bed life from 6 to 18 months. Food processing plants using 304SS mesh caps achieved 99.98% bacterial retention while maintaining 95% flow rates. Petrochemical operators report 22% energy savings versus traditional bag filters.
Certification and Testing Protocols
All production batches undergo ASME Section VIII Division 1 pressure validation. Third-party labs confirm 100% compliance with ISO 2941 (burst pressure) and ISO 9044 (aperture uniformity) standards. Filters destined for nuclear applications receive additional NQA-1 certification through 72-hour cycled stress testing.
Innovations in Woven Wire Mesh Filter Technology
Recent advancements include shape-memory nickel-titanium alloys that self-clean at specific temperatures, reducing maintenance intervals by 60%. Digital twin systems now predict filter lifespan within 5% accuracy using real-time pressure differential data. These developments position woven mesh as the foundation for next-generation smart filtration infrastructure.
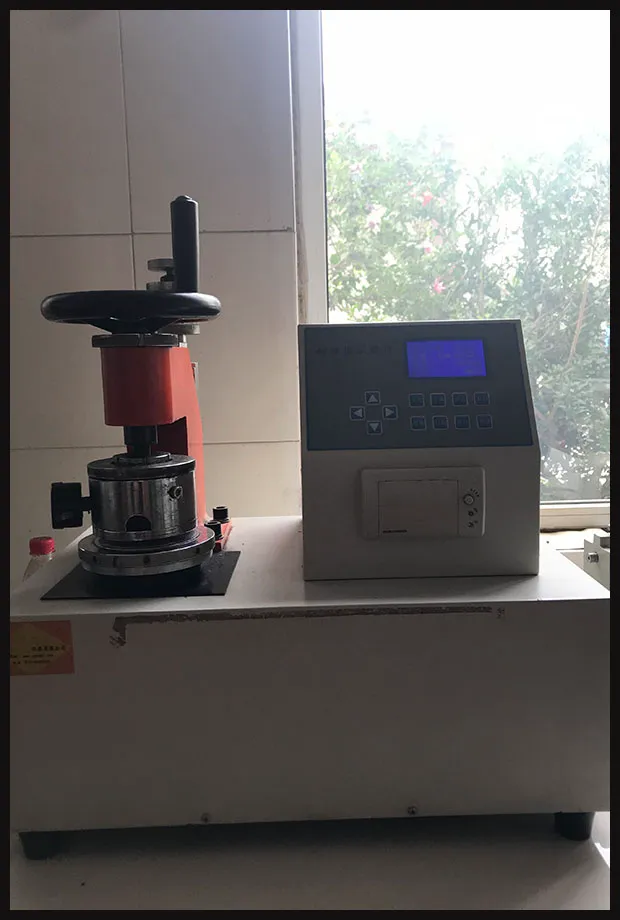
(woven wire mesh filter)
FAQS on woven wire mesh filter
What are the key applications of woven wire mesh filters?
Q: Where are woven wire mesh filters commonly used?
A: Woven wire mesh filters are ideal for industrial filtration, water treatment, food processing, and oil/gas separation due to their durability and precise pore sizing.
How do filter mesh caps enhance filtration systems?
Q: What is the purpose of a filter mesh cap?
A: Filter mesh caps protect equipment from debris, ensure uniform flow distribution, and extend filter lifespan by preventing large particles from entering sensitive components.
What advantages do non-woven synthetic filters offer?
Q: Why choose non-woven synthetic filter media?
A: Non-woven synthetic media provide higher dust-holding capacity, chemical resistance, and cost-efficiency for air/fluid filtration compared to traditional woven mesh.
How to select the right mesh size for filtration?
Q: What determines mesh size in woven wire filters?
A: Mesh size depends on particle size to be filtered – finer meshes (higher count) trap smaller particles, while coarser meshes handle high-flow applications.
Can woven wire mesh filters withstand high temperatures?
Q: Are these filters suitable for high-temperature environments?
A: Yes, stainless steel woven wire mesh filters excel in high-heat settings like exhaust systems, with grades like 304/316 offering thermal and corrosion resistance.
Post time: મે-13-2025