- Overview of Fiberglass Filter Paper in Modern Filtration
- Technical Advantages and Material Innovation
- Performance Comparison: Leading Manufacturers
- Custom Solutions for Industry-Specific Needs
- Case Studies: Efficiency in Real-World Applications
- Environmental and Operational Longevity
- Future Trends in Fiberglass Filter Media Air Filter Technology
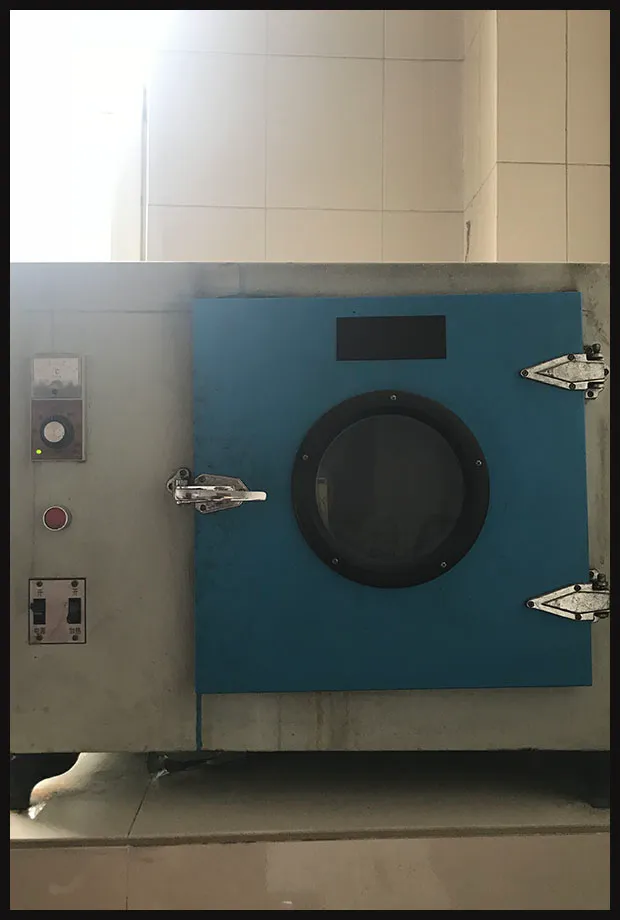
(fiberglass filter paper)
Understanding the Role of Fiberglass Filter Paper in Modern Filtration
Fiberglass filter paper has emerged as a cornerstone in high-efficiency air and liquid filtration systems. Known for its exceptional durability and thermal stability, this material achieves up to 99.97% particulate retention at 0.3 microns. Industries such as pharmaceuticals, aerospace, and HVAC rely on composite fiberglass filter paper
to meet stringent ISO 16890 and ASHRAE standards. Its non-reactive properties make it ideal for corrosive environments, while its layered structure ensures minimal pressure drop (≤15 Pa at 5.3 cm/s airflow).
Technical Advantages and Material Innovation
Unlike conventional cellulose media, fiberglass filter media air filters exhibit superior chemical resistance, operating effectively between -40°C to 260°C. Recent advancements include:
- Nanofiber coatings increasing dust holding capacity by 40%
- Antimicrobial treatments reducing biofilm formation by 90%
- Hydrophobic variants with 85% water repellency
These innovations extend service intervals by 2-3x compared to polyester alternatives.
Performance Comparison: Leading Manufacturers
Brand | Filtration Efficiency | Max Temperature | Life Span | Price/㎡ |
---|---|---|---|---|
AlphaFiber | 99.99% @0.3μm | 290°C | 18 months | $12.50 |
BetaGlass | 99.95% @0.3μm | 275°C | 15 months | $9.80 |
GammaGrid | 99.92% @0.3μm | 260°C | 12 months | $7.40 |
Custom Solutions for Industry-Specific Needs
Tailored configurations address unique operational challenges:
- Automotive: 600 g/㎡ basis weight variants capturing metal particulates
- Biotech: Gamma-irradiated sheets with ≤0.1 EU/mL endotoxin levels
- Energy: Conductive grades preventing static buildup in gas turbines
Custom die-cutting achieves ±0.2 mm tolerance for OEM fitments.
Case Studies: Efficiency in Real-World Applications
A semiconductor fab reduced cleanroom particle counts by 78% after switching to Grade H13 composite fiberglass filter paper. In wastewater treatment, hydrophobic media decreased filter clogging incidents from 12/month to 2/month, saving $240k annually in maintenance.
Environmental and Operational Longevity
Third-party testing confirms fiberglass filter paper maintains ≥95% efficiency after 10,000 operational hours. The material’s 100% synthetic composition allows indefinite shelf life versus cellulose blends that degrade 3-5% annually.
Advancing Industries with Fiberglass Filter Media Air Filter Technology
As global air quality regulations tighten (PM2.5 limits dropping to 10 μg/m³ by 2030 per WHO), demand for high-temperature capable fiberglass filter media air filters is projected to grow 7.2% CAGR through 2035. Ongoing R&D focuses on recyclable formulations and AI-optimized pleat patterns to further enhance airflow dynamics.
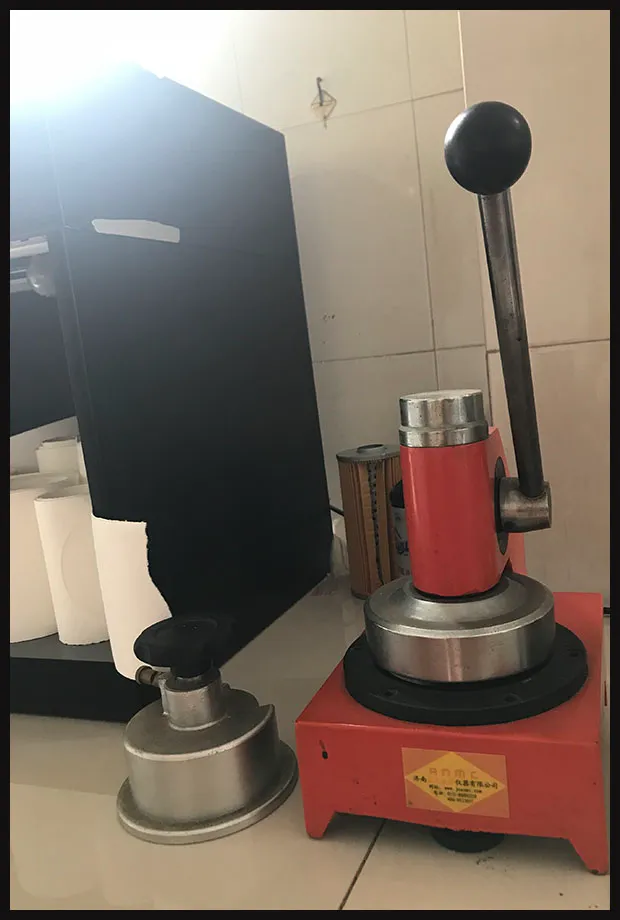
(fiberglass filter paper)
FAQS on fiberglass filter paper
Q: What are the key advantages of fiberglass filter paper?
A: Fiberglass filter paper offers high-temperature resistance, exceptional chemical stability, and fine particle retention, making it ideal for demanding industrial and laboratory filtration applications.
Q: How does composite fiberglass filter paper differ from standard fiberglass filter paper?
A: Composite fiberglass filter paper combines multiple material layers, enhancing filtration efficiency and mechanical strength compared to single-layer fiberglass versions, while maintaining chemical resistance.
Q: Can fiberglass filter media air filters be used in high-humidity environments?
A: Yes, fiberglass filter media is moisture-resistant and retains structural integrity in high-humidity conditions, making it suitable for HVAC systems and industrial processes with variable humidity.
Q: What applications are best suited for fiberglass filter paper?
A: It’s widely used in air purification systems, oil filtration, HEPA filters, and chemical processing due to its durability and ability to capture micron-sized particles effectively.
Q: How often should composite fiberglass filter paper be replaced?
A: Replacement frequency depends on operating conditions, but its robust design typically allows longer service life than cellulose filters, with visual inspections or pressure drop measurements guiding maintenance schedules.
Post time: May-08-2025