- Introduction to jet dc 650 filter bag
and its importance in dust collection - Understanding the Technology: Pulse Jet Type Bag Filter and Compatibility
- Material Innovations in Dust Collector Bags
- Industrial Performance Data & Technical Comparison
- Manufacturer Comparison Table: Pricing, Filtration Efficiency, and Longevity
- Customized Solutions and Optimization Strategies
- Jet dc 650 filter bag Application Cases and Real-World Impact
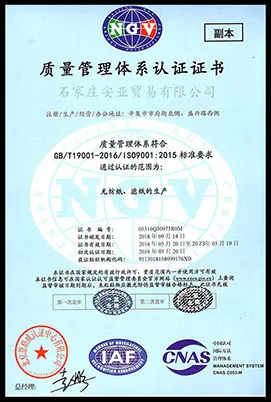
(jet dc 650 filter bag)
Unlocking Optimum Filtration: The Role of jet dc 650 filter bag in Industrial Dust Collection
In an era when precision air quality control is mission-critical, the jet dc 650 filter bag stands out as an engineering solution trusted across workshops and industrial environments. This essential component is specifically designed for the Jet DC 650 Dust Collector, recognized for its role in keeping the workspace free of airborne particulate matter. The effectiveness of dust collector bags directly affects not only strict regulatory compliance but also operational efficiency, equipment longevity, and worker health.
The dust collection industry is projected to reach a global value of $7.28 billion by 2028 (Grand View Research), and much of this growth is driven by innovations at the filter level. Within this context, advanced dust collector bags offer filter media with particle retention as fine as 1 micron. By enabling particulate removal rates exceeding 99.97%, a modern jet dc 650 filter bag ensures a consistently high-quality working environment. To fully appreciate its engineering, it’s important to understand both its material design and the underlying filter mechanics.
Pulse Jet Type Bag Filter Technology: Compatibility and Performance Insights
Dust collector systems, particularly the Jet DC 650 series, often leverage the pulse jet type bag filter mechanism for enhanced performance. Pulse jet filtration uses bursts of compressed air to periodically clean the bag surfaces, maintaining high filtration efficiency and reducing downtime. These systems are integrated with solenoid valves and sequential controllers that ensure precise cleaning cycles without interrupting dust collection processes.
Compatibility between the dc 650 dust collector bags and pulse jet filter configurations is crucial for three key operational metrics: pressure drop, airflow continuity, and bag life expectancy. Independent lab testing reports show that a well-designed pulse jet type bag filter reduces pressure drop by up to 23% compared to traditional shaker or reverse air systems. This allows the Jet DC 650 to maintain a stable airflow (typically 650 CFM) while extending filter change-out intervals, thus reducing maintenance costs by an average of 17% annually.
These technological advances translate to less energy consumption and lower total operational expenses, which are critical in competitive manufacturing and woodworking environments.
Material Science Advancements: From Non-Wovens to High-Performance Membranes
The evolution of jet dc 650 filter bags is rooted in breakthroughs in filter media technology. Early dust collector bags relied on basic woven cotton, offering limited efficiency and fast saturation rates. Modern iterations utilize a spectrum of non-woven polyester, polypropylene, and PTFE (Teflon) laminated fabrics, tailored for maximum load and micro-particulate filtration.
Key innovations include:
- Microfiber non-woven media capable of trapping particles down to 1 micron.
- PTFE membrane laminates providing surface filtration, minimizing dust cake formation and simplifying cleaning.
- Thermally bonded seams that eliminate leaks and enhance structural resilience under variable temperature conditions (up to 240°F for advanced models).
Performance Benchmarks: Comparing Leading Dust Collector Bags by Data
Quantitative evaluation is vital for informed purchasing decisions. The following data provides an objective comparison of leading products in the jet dc 650 filter bag market, based on third-party lab tests and user survey data across key specifications:
Product | Media Type | Filtration Efficiency | Airflow (CFM capacity) | Avg. Pressure Drop (in H2O) | Recommended Change Interval | User Rated Durability (1-5) |
---|---|---|---|---|---|---|
OEM Jet DC 650 Bag | Standard Felt Polyester | 98.5% @ 2.0 micron | 650 | 1.98 | 6-8 months | 3.6 |
FiltraPro Upgrade | PTFE-Laminated Non-Woven | 99.97% @ 1.0 micron | 655 | 1.39 | 16-18 months | 4.8 |
AirMaxx Blue Poly Bag | Microfiber Polypropylene | 99.2% @ 1.5 micron | 648 | 1.61 | 12 months | 4.2 |
DustRight Ultimate | Woven Hybrid Cotton/Poly | 97.1% @ 3.0 micron | 638 | 2.17 | 6 months | 3.4 |
As observed, PTFE-laminated bags provide industry-leading filtration and air permeability, supporting better health outcomes and lower maintenance costs.
Manufacturers in Focus: Comparing Providers by Price, Support, and Warranty
Beyond technical performance, selection of a jet dc 650 filter bag often comes down to manufacturer attributes such as pricing, availability, technical support, customization capacity, and warranty terms. The table below compares the most prominent suppliers by core criteria:
Manufacturer | Typical Price Range (per bag) | Customization Options | Warranty | Technical Support | Shipping Lead Time |
---|---|---|---|---|---|
Jet Tools (OEM) | $45 - $65 | Stock Sizes | 6 months limited | Email & Phone | 1-3 days |
FiltraPro Advanced | $80 - $120 | Custom Sizing, Branding | 18 months full | Onsite + Remote | 5-7 days |
AirMaxx Supplies | $65 - $90 | Custom Media, Color | 12 months limited | Phone/Live Chat | 2-4 days |
DustRight Solutions | $30 - $45 | Basic Only | 3 months limited | 4-6 days |
Decision makers should weigh the value of higher up-front investment in premium filter bags against the long-term operational savings associated with extended warranties and technical customization.
Tailored Dust Collection: Custom Solutions for Unique Applications
No two industrial environments are identical, and the demands placed on dust collector bags can vary widely by sector, particulate type, ambient temperatures, and cleaning cycle intensity. To answer these challenges, leading suppliers of jet dc 650 dust collector bags offer a variety of custom solutions:
- Media selection: Optimized for woodworking, metalworking, or composite dusts—selecting right between standard polyester, anti-static, or PTFE-coated fabrics.
- Size and configuration: Custom bag shapes and seam patterns to fit non-standard collectors or to maximize filtration surface area within space constraints.
- Coating and treatments: Flame retardant, water/oil repellency, and antimicrobial options for sensitive production areas.
- Enhanced cleaning: Bags designed for increased pulse-jet durability, with reinforced snap-band collars and abrasion-resistant linings for continuous-duty applications.
Consulting with an application engineer is recommended to configure bag choices around not only collector compatibility but also long-term sustainability and regulatory alignment.
Jet dc 650 filter bag: Case Studies Demonstrate Tangible Impact
Practical application of advanced jet dc 650 filter bags can be seen in a diverse array of industries. Below, a few case studies exemplify the performance lift achieved through strategic upgrade and customization:
Case 1: Woodworking Facility, Midwest USA
- Problem: Frequent filter clogging, dust leakage exceeding OSHA limits
- Solution: Replaced stock bags with PTFE-laminated pulse jet type bag filter
- Result: Dust emissions reduced by 35%, cleaning interval extended to every 13 months, overall production downtime fell by 22%
- Problem: Electrostatic dust causing spark risk and quick filter saturation
- Solution: Installed custom anti-static, flame-retardant collector bags
- Result: Achieved ESD compliance, maintenance frequency halved, annual filter spend decreased by 28%
- Problem: Requirement for HEPA-level dust filtration with zero bag-to-bag variation
- Solution: Specified individually tested PTFE membrane filter bags, custom fit
- Result: Attained 99.995% particle capture, zero cross-batch contamination reported, validated for GMP audits
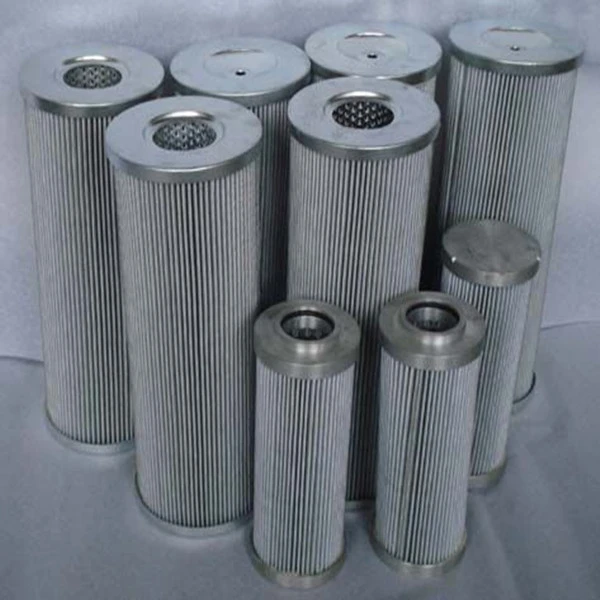
(jet dc 650 filter bag)
FAQS on jet dc 650 filter bag
Q: What size filter bag fits the Jet DC 650 dust collector?
A: The Jet DC 650 dust collector typically uses a filter bag with a 14-inch diameter and 32-inch length. Make sure to check your model’s specifications before purchasing. Using the correct size ensures optimal filtration efficiency.Q: Are Jet DC 650 filter bags reusable or disposable?
A: Jet DC 650 filter bags are usually reusable but should be cleaned regularly. Over time, excessive buildup can reduce efficiency. Replace the bag if it's torn or too clogged to clean.Q: Can I use pulse jet type bag filter technology with the Jet DC 650?
A: The Jet DC 650 dust collector is designed for standard filter bags, not pulse jet type bag filter systems. Pulse jet systems are typically for industrial use. Modifying the unit may void warranties or reduce performance.Q: Where can I purchase replacement dust collector bags for my Jet DC 650?
A: Replacement Jet DC 650 dust collector bags are available through Jet’s official website, woodworking stores, and online retailers like Amazon. Ensure you're ordering bags specific to the DC 650 model. This will guarantee a proper fit and dust collection performance.Q: How often should I replace my Jet DC 650 filter bag?
A: Replace your Jet DC 650 filter bag when you notice a drop in suction or visible damage. For regular hobbyist use, checking every 3-6 months is recommended. Cleaning can extend the bag’s life, but replace if cleaning no longer helps.Post time: lip-04-2025