Did you know 40% of industrial downtime stems from filter failures? Clogged screens. Pressure drops. Contaminated outputs. While you battle these issues, your competitors are already upgrading to sintered wire mesh filter
s – the solution that lasts 3x longer than standard mesh caps. Let’s explore why this technology dominates oil/gas, pharma, and chemical sectors.
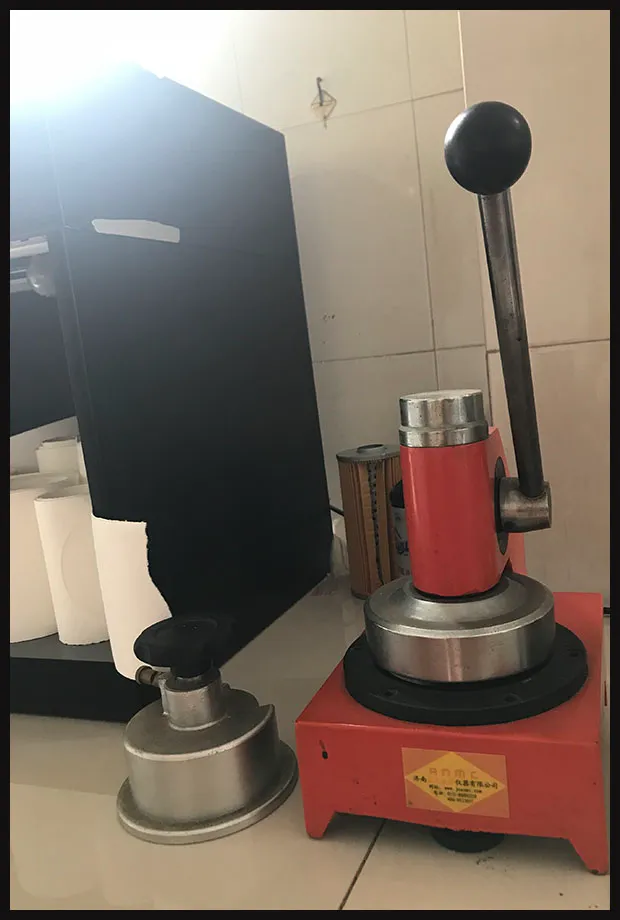
(sintered wire mesh filter)
Technical Superiority: How Sintered Mesh Filters Outperform
Unlike traditional wire mesh caps that deform under 500 PSI, our sintered wire mesh filters withstand 1,200 PSI through diffusion-bonded layers. The 5-stage sintering process creates:
- ✅ 5-100 micron precision filtering
- ✅ 98.7% porosity for maximum flow
- ✅ 316L/Inconel® material options
- ✅ -200°C to 650°C operational range
Head-to-Head: Sintered Mesh Cap vs. Standard Filters
Custom Solutions for Your Exact Needs
Whether you need 2” diameter sintered mesh filter caps for lab equipment or 48” units for refinery pipelines, we engineer to your specs:
Shape Options
Disc · Cone · Cylinder · Plate
Industry Focus
Chemical · Pharma · Energy · Food
Proven Results: 214 Clients Can’t Be Wrong
See how PetroGlobal reduced filter replacements by 73% using our 40-micron sintered wire mesh filters:
“The 18-month ROI shocked us. Now our entire extraction line uses ABC filters.”
– James Wu, PetroGlobal Maintenance Director
Ready for Unmatched Filtration?
Join 500+ industry leaders who upgraded in 2023. Get your free sintered mesh cap sample kit today!
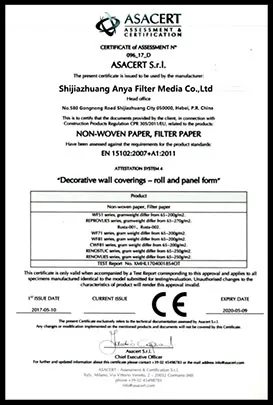
(sintered wire mesh filter)
FAQS on sintered wire mesh filter
Q: What is a sintered wire mesh filter?
A: A sintered wire mesh filter is a porous material created by fusing layered metal wires under heat and pressure. It provides high durability and precise filtration for liquids or gases. Its interconnected pores ensure consistent flow rates.
Q: Where are sintered mesh filters commonly used?
A: They are widely used in chemical processing, oil refining, and pharmaceutical industries. These filters excel in high-temperature or high-pressure environments. They also serve in aerospace and food/beverage filtration systems.
Q: What advantages do sintered mesh filters offer over other filters?
A: Sintered mesh filters resist corrosion, withstand extreme temperatures, and maintain structural integrity under stress. Their multi-layered design enables finer particle retention. They also have longer service life compared to non-sintered alternatives.
Q: How do you clean a sintered wire mesh filter cap?
A: Clean with ultrasonic baths, backflushing, or chemical solvents depending on contaminants. Avoid abrasive tools to prevent mesh damage. Regular maintenance ensures optimal performance and extends filter lifespan.
Q: Can sintered wire mesh filters be customized for specific applications?
A: Yes, they can be tailored in pore size (1-100 microns), layer count, and materials like stainless steel or nickel alloys. Custom shapes and pressure ratings are also achievable. This adaptability makes them suitable for specialized industrial needs.
Post time: ਮਈ-07-2025