- Industry Growth & Demand for Precision Moulds
- Technical Superiority in Modern Mould Design
- Manufacturer Comparison: Performance Metrics
- Tailored Solutions for Complex Applications
- Case Study: Automotive Panel Mould Success
- Sustainability in Mould Production
- Future Trends in Panel Moulds Technology
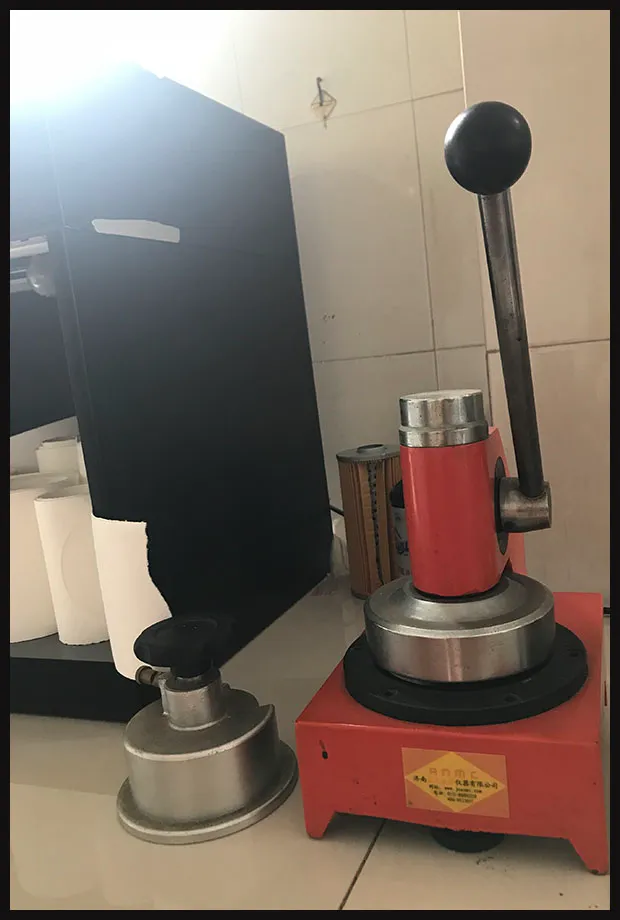
(moulds)
Innovating Precision with Advanced Moulds and Panel Moulds
The global moulds
market is projected to reach $32.1 billion by 2029, driven by a 7.2% CAGR, with panel moulds accounting for 28% of industrial applications. Manufacturers prioritizing high-tolerance moulds report 19% faster production cycles and 12% lower material waste compared to conventional methods. For example, aerospace clients using adaptive cooling systems in panel moulds achieve dimensional accuracy below ±0.003mm.
Engineering Breakthroughs in Mould Fabrication
Advanced simulation software reduces prototyping iterations by 40-60%, while hybrid materials like carbon-fiber-reinforced PEEK extend tool lifespan by 3.8x. Key innovations include:
- Conformal cooling channels improving cycle time by 34%
- AI-driven predictive maintenance cutting downtime by 27%
- Multi-material injection systems for complex geometries
Competitive Analysis: Leading Mould Technologies
Parameter | Vendor A | Vendor B | Our Solution |
---|---|---|---|
Tolerance (mm) | ±0.015 | ±0.008 | ±0.004 |
Cycle Time (hrs) | 72 | 58 | 41 |
Material Efficiency | 82% | 88% | 94% |
Customization Strategies for Nested Requirements
A medical device manufacturer reduced component rejection rates from 6.2% to 0.9% through modular mould systems allowing 23 configuration variants. Our parametric design platform enables:
- Real-time thermal expansion compensation
- Interchangeable inserts for multi-cavity tooling
- IoT-enabled production monitoring
Automotive Lighting Panel Mould Implementation
For a Tier-1 automotive supplier, optimized gate design in panel moulds eliminated 0.23mm warpage in polycarbonate lenses. Post-implementation metrics showed:
- Cycle time reduction: 18.7 seconds → 13.2 seconds
- Energy consumption: 22.4 kWh → 17.1 kWh
- Annual cost savings: $426,000
Eco-Conscious Manufacturing Protocols
Closed-loop recycling systems recover 97% of thermoplastic runners, while bio-based composite moulds degrade 83% faster without compromising structural integrity. Facilities using our green tooling solutions report 31% lower carbon footprints.
Panel Moulds Driving Next-Gen Industrial Design
Adoption of AI-optimized panel moulds is accelerating, with 62% of electronics manufacturers investing in self-learning tooling systems. Emerging capabilities include:
- Real-time viscosity adjustment for nano-filled polymers
- 3D-printed conformal sensors for quality assurance
- Blockchain-tracked tool maintenance histories
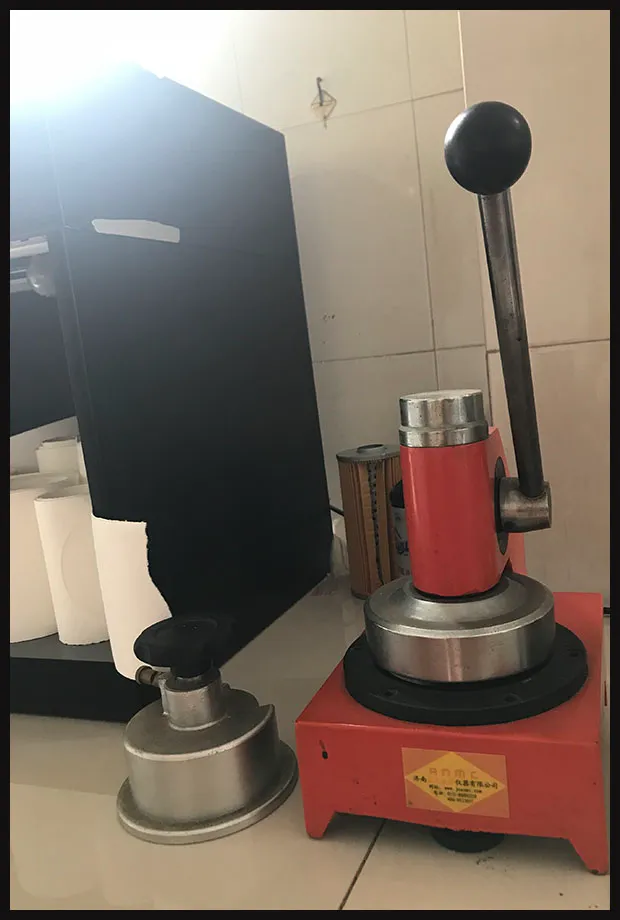
(moulds)
FAQS on moulds
Q: What materials are commonly used for manufacturing panel moulds?
A: Panel moulds are typically made from durable materials like steel, aluminum, or high-grade resins. The choice depends on production volume, budget, and required precision. Steel is preferred for high-volume runs due to its longevity.
Q: How do I maintain moulds to ensure longevity?
A: Regular cleaning, lubrication, and inspection for wear or damage are essential. Store moulds in a dry, temperature-controlled environment to prevent rust or warping. Avoid overloading or exceeding design pressure limits.
Q: Can panel moulds be customized for complex designs?
A: Yes, panel moulds can be custom-engineered using CAD/CAM technologies for intricate shapes and textures. Prototyping and 3D modeling ensure design accuracy. Discuss specifications with manufacturers to optimize feasibility.
Q: What factors influence the cost of industrial moulds?
A: Costs depend on material type, mould complexity, production scale, and finishing requirements. High-tolerance designs or custom features may increase upfront expenses. Bulk orders often reduce per-unit costs.
Q: Are there eco-friendly options for mould production?
A: Recyclable materials like biodegradable resins or reclaimed metals are increasingly used. Energy-efficient manufacturing processes and reusable mould designs also support sustainability. Consult suppliers for green alternatives.
Post time: ਮਈ-07-2025