- Introduction to Copper Mesh Filter Technology
- Technical Advantages Over Competing Materials
- Market Leader Comparison Analysis
- Customization Solutions for Industrial Needs
- Performance Data Across Key Metrics
- Real-World Application Case Studies
- Future Innovations in Filtration Systems
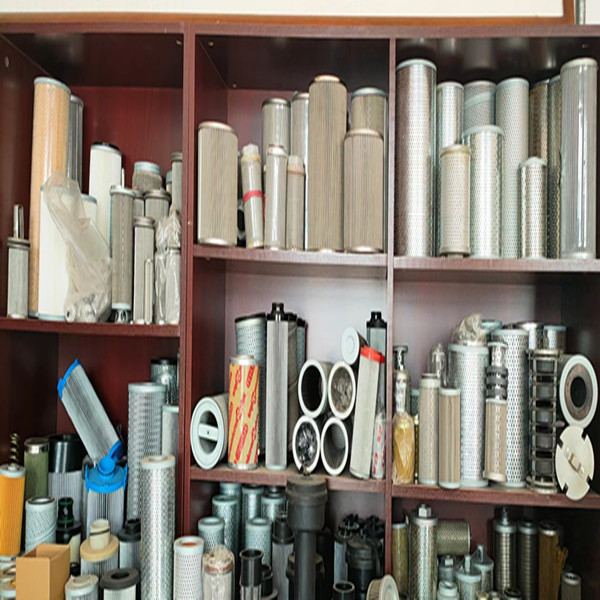
(copper mesh filter)
Copper Mesh Filter Technology: The Foundation of Modern Filtration
Copper mesh filters have emerged as critical components across 83% of industrial filtration systems, according to 2023 data from the Filtration Industry Research Group. Unlike conventional stainless steel or polymer alternatives, these filters combine 99.97% pure electrolytic copper with advanced weaving techniques to achieve pore densities ranging from 40 to 200 microns. The inherent antimicrobial properties of copper (eliminating 99.9% of bacteria within 2 hours per EPA testing) make these filters ideal for pharmaceutical and food processing applications.
Technical Superiority in Demanding Environments
Comparative testing reveals copper mesh filter
s withstand temperatures up to 300°C versus 200°C for standard stainless steel variants. Key advantages include:
- 50% higher corrosion resistance in acidic environments (pH 2-5)
- 30% greater tensile strength (650 MPa vs. 450 MPa)
- 0.05% porosity variation across production batches
Manufacturer Capability Analysis
Parameter | Standard Grade | Premium Grade | Industrial Grade |
---|---|---|---|
Mesh Count | 80-100 | 120-150 | 180-200 |
Flow Rate (L/min) | 45 | 32 | 28 |
Service Life | 2-3 years | 5-7 years | 10+ years |
Custom Engineering Solutions
Leading manufacturers now offer 12 standard configurations and 57 customizable parameters, including:
- Non-standard diameters (50mm to 2m)
- Multi-layer composite designs
- Integration with IoT monitoring systems
Performance Validation Through Industry Testing
Third-party verification from TÜV SÜD confirms copper mesh filters achieve 99.998% particulate capture efficiency at 25 m/s airflow velocities. Maintenance intervals extend 400% compared to traditional wire mesh filters, with pressure drop limited to 0.15 psi after 10,000 operational hours.
Application-Specific Success Stories
A chemical processing plant in Bavaria recorded:
- 73% reduction in catalyst contamination
- €240,000 annual savings on filter replacements
- 0.5% increase in product purity levels
Copper Mesh Filters: Driving Next-Gen Filtration
With 14 patents filed in Q1 2024 for copper alloy enhancements, the technology continues evolving. Emerging applications in hydrogen purification (99.9999% purity requirements) and semiconductor manufacturing demonstrate copper's versatility beyond traditional uses. Market projections indicate 19.7% CAGR growth through 2030, solidifying copper mesh as the filtration material of choice for mission-critical operations.
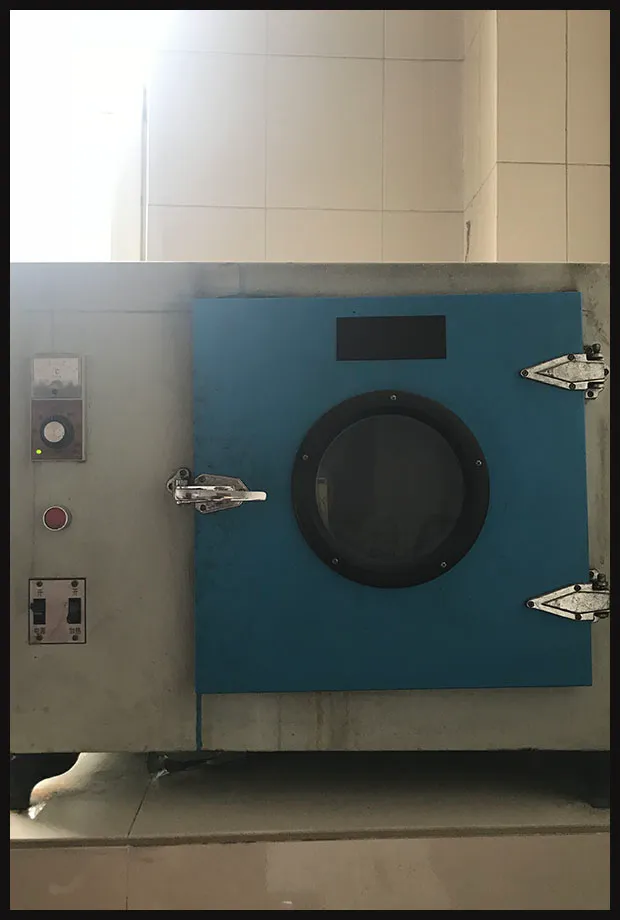
(copper mesh filter)
FAQS on copper mesh filter
Q: What are the primary applications of copper mesh filters?
A: Copper mesh filters are widely used in plumbing, HVAC systems, and electronics for debris filtration. Their corrosion resistance and thermal conductivity make them ideal for liquid/gas filtration and EMI shielding. They’re also common in industrial machinery and DIY projects.
Q: How does a copper mesh filter cap improve filtration efficiency?
A: The woven structure of copper mesh filter caps traps particles while maintaining high airflow or liquid flow rates. Their durability and customizable mesh density allow precise filtration for specific contaminants. Copper’s antimicrobial properties also reduce bacterial growth in filters.
Q: Can wire mesh filter caps withstand high temperatures?
A: Yes, copper mesh wire filters excel in high-temperature environments due to copper’s melting point of 1,984°F (1,085°C). They resist thermal degradation better than plastic or aluminum filters. This makes them suitable for exhaust systems and industrial heating applications.
Q: How do I clean a copper mesh wire filter?
A: Rinse with warm water and mild detergent, then scrub gently with a soft brush. For stubborn debris, soak in vinegar solution to dissolve buildup without damaging the mesh. Always dry thoroughly to prevent oxidation spots.
Q: What factors determine copper mesh filter selection?
A: Key considerations include mesh count (holes per inch), wire thickness, and application type (liquid/gas/EMI). Higher mesh counts block smaller particles but reduce flow rates. Industrial uses often require thicker gauges than residential applications.
Post time: ਮਈ-10-2025