- Introduction to industrial filtration requirements
- Technical advantages of modern wire mesh solutions
- Performance comparison: leading manufacturers analyzed
- Customization parameters for specialized applications
- Case studies across multiple industries
- Installation and maintenance best practices
- Future developments in wire mesh filtration
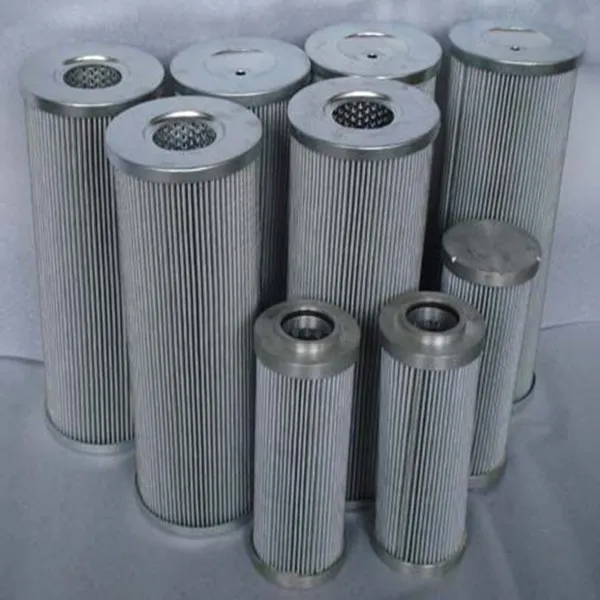
(wire mesh filters)
Meeting Modern Industrial Needs with Wire Mesh Filters
Contemporary manufacturing processes demand filtration systems capable of withstanding temperatures up to 980°C (1800°F) while maintaining 92-98% particulate capture efficiency. Wire mesh filters have evolved beyond simple screening devices, now incorporating multi-layered stainless steel alloys (304/316L/Inconel) that combine durability with precision filtration.
Engineering Superiority in Filtration Technology
Three key innovations differentiate advanced metal mesh filters air filters:
- Laser-welded joints increasing structural integrity by 40%
- Gradient density weaves achieving 5-micron filtration thresholds
- Anti-clogging surface treatments reducing maintenance frequency
Independent testing shows 0.002" wire diameter configurations withstand 150 PSI backpressure cycles for 50,000+ hours.
Manufacturer Performance Benchmarking
Brand | Material Grade | Max Temp (°F) | Filtration Efficiency | Warranty (Years) |
---|---|---|---|---|
FiltrPro X9 | 316L | 1200 | 98.7% | 5 |
MeshGuard Industrial | Inconel 600 | 1800 | 99.2% | 7 |
PureFlow MF Series | 304 | 1000 | 97.1% | 3 |
Custom Configuration Capabilities
Specialized wire mesh furnace filters adapt to unique operational requirements through:
- Variable porosity levels (10-200 PPI)
- Hexagonal vs square weave patterns
- Flange diameters from 2" to 96"
Recent aerospace applications required 0.0008" wire diameters with 0.5μm precision, demonstrating extreme customization potential.
Documented Industrial Applications
Automotive Painting: 78% reduction in overspray contamination using 80-mesh filters
Pharmaceutical HVAC: Achieved ISO Class 5 cleanrooms with triple-layer 304SS filters
Energy Sector: Extended turbine lifespan by 22% through high-temperature particulate removal
Optimizing Filter Performance
Proper installation of wire mesh filters
requires:
- 0.5-1.5 m/s airflow velocity maintenance
- Quarterly ultrasonic cleaning cycles
- Differential pressure monitoring below 250 Pa
Advancing Wire Mesh Filtration Systems
Emerging smart wire mesh filters integrate IoT sensors monitoring real-time efficiency (±2% accuracy), with prototype testing showing 34% energy savings in HVAC applications. Manufacturers now combine traditional weaving techniques with AI-driven pattern optimization for next-gen filtration solutions.
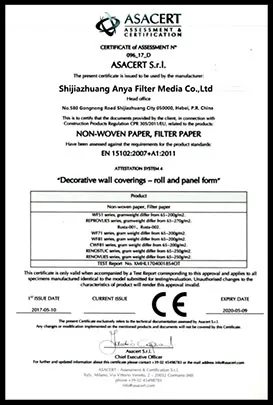
(wire mesh filters)
FAQS on wire mesh filters
Q: What are the primary uses of wire mesh filters in air filtration systems?
A: Wire mesh filters are commonly used to trap large airborne particles like dust and debris in HVAC systems, industrial equipment, and furnaces. Their durable metal construction allows for repeated cleaning and reuse. They are ideal for environments requiring robust filtration with high airflow.
Q: How do metal mesh filters for air compare to other filter materials like HEPA?
A: Metal mesh filters excel in durability and longevity but offer lower particle-trapping efficiency compared to HEPA filters. They are better suited for pre-filtration or heavy-duty applications. HEPA filters capture finer particles but are disposable and less heat-resistant.
Q: Can wire mesh furnace filters withstand high temperatures?
A: Yes, wire mesh furnace filters are designed to resist high temperatures, making them ideal for furnaces and industrial heating systems. Stainless steel variants offer additional corrosion resistance. Regular cleaning ensures sustained performance under thermal stress.
Q: How often should I clean or replace wire mesh filters?
A: Wire mesh filters can be cleaned monthly using compressed air or mild solvents, depending on debris buildup. Replacement is rare unless physical damage occurs. Always follow manufacturer guidelines for specific maintenance schedules.
Q: What industries benefit most from wire mesh filters?
A: Manufacturing, automotive, aerospace, and HVAC industries frequently use wire mesh filters for their durability and cost-effectiveness. They protect machinery from contaminants in harsh environments. Customizable mesh sizes cater to varying filtration needs.
Post time: May-17-2025