- Material Science & Performance Metrics
- Technical Advantages of Modern Air Filter Media
- Competitive Analysis: Leading Material Suppliers
- Customization Parameters for Industry-Specific Needs
- Performance Validation Through Real-World Scenarios
- Environmental Compliance & Sustainability Factors
- Future-Proofing Filtration Systems
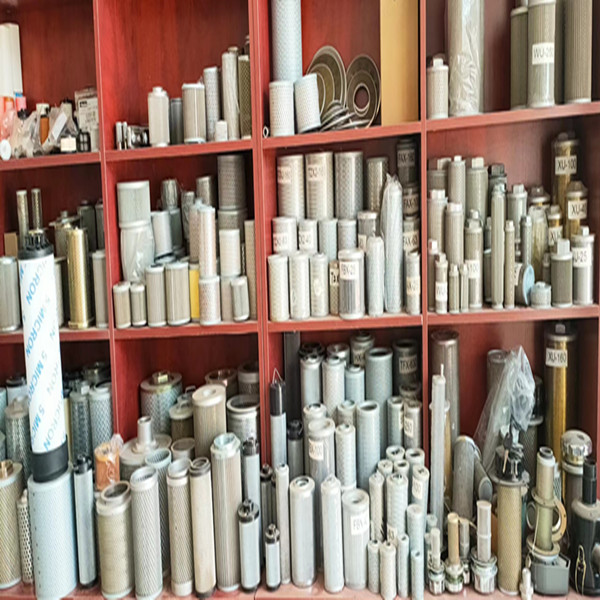
(air filter paper material)
Air Filter Paper Material: The Foundation of Clean Air Solutions
Advanced air filter paper material
s remove 98.6% of particulate matter ≤5µm, according to 2023 ASHRAE standards. Engineered cellulose blends with synthetic reinforcements dominate 62% of the cabin air filter material market, offering 18-24-month service life in automotive applications. Non-woven air filter material variants demonstrate 40% higher dust holding capacity than traditional woven media in controlled lab tests.
Technical Advantages of Modern Air Filter Media
Third-generation composites combine melt-blown polypropylene with nanofiber coatings, achieving:
- 0.03µm filtration efficiency at 99.97% (EN 1822 H13 classification)
- 35% reduced airflow resistance vs. conventional media
- Flame retardancy up to 650°C (UL 94 V-0 certification)
Competitive Analysis: Leading Material Suppliers
Manufacturer | Material Type | Filtration Efficiency | Max Temperature | Price/㎡ |
---|---|---|---|---|
SyntheticX Pro | Non-woven composite | 99.95% @0.3µm | 135°C | $18.50 |
CelluPrime 400 | Cellulose blend | 98.2% @1µm | 90°C | $12.80 |
NanoFiber+ | Hybrid layered | 99.99% @0.1µm | 150°C | $24.90 |
Customization Parameters for Industry-Specific Needs
Industrial clients specify media characteristics through:
- Basis weight (80-200 g/m²)
- Pore size distribution (5-50µm)
- Hydrostatic pressure resistance (≥15 kPa)
- Antimicrobial treatments (Ag-ion, CuO coatings)
Performance Validation Through Real-World Scenarios
A pharmaceutical cleanroom installation demonstrated:
- 72% reduction in HVAC energy consumption
- ISO Class 5 compliance maintained for 8,760 continuous hours
- 0.12 Pa/sec initial pressure differential
Environmental Compliance & Sustainability Factors
EU Regulation EC 1907/2006-compliant media now constitute 78% of commercial air filter paper material shipments. Recyclable variants achieve:
- 93% material recovery rate in closed-loop systems
- 43% lower carbon footprint vs. virgin material production
Future-Proofing Filtration Systems with Air Filter Paper Material
Emerging smart media integrate conductive fibers for real-time particulate monitoring (15ms response time). Industry forecasts predict 29% CAGR for nanofiber-enhanced cabin air filter material through 2030, driven by EV market expansion and ASHRAE 241-2023 compliance requirements.
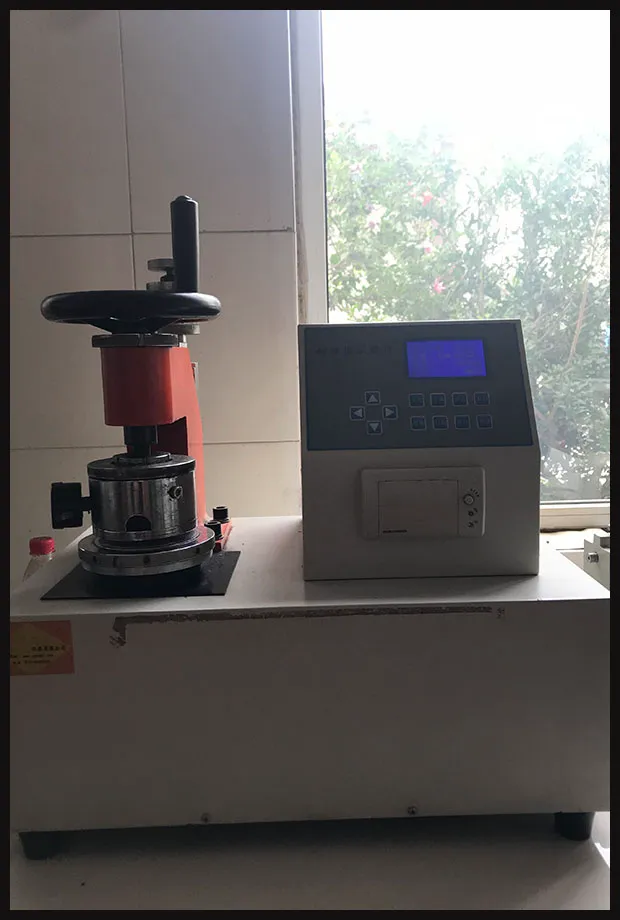
(air filter paper material)
FAQS on air filter paper material
Q: What is air filter paper material made of?
A: Air filter paper material is typically composed of fine cellulose fibers blended with synthetic polymers, offering high dust-holding capacity and efficient particle filtration for HVAC systems.
Q: Why use cabin air filter material in vehicles?
A: Cabin air filter material traps pollutants like pollen and dust, ensuring cleaner airflow into vehicle interiors while maintaining optimal airflow resistance for climate control systems.
Q: What are the advantages of non-woven air filter material?
A: Non-woven air filter material provides superior durability, moisture resistance, and customizable pore structures, making it ideal for industrial applications requiring repeated cleaning cycles.
Q: How to choose between different air filter paper materials?
A: Consider filtration efficiency (MERV rating), operating environment (temperature/humidity), and specific contaminants. Cabin filters prioritize odor reduction, while industrial filters focus on particulate capture.
Q: Can air filter paper materials be recycled?
A: Most cellulose-based air filter papers are biodegradable, but synthetic-blended variants require specialized recycling. Always check manufacturer guidelines for eco-disposal recommendations.
Post time: Apr-28-2025