- Introduction to Precision Filtration Standards
- Technical Specifications & Performance Metrics
- Material Durability in Extreme Environments
- Competitive Analysis of Mesh Filter Manufacturers
- Custom Engineering for Industry-Specific Needs
- Operational Case Studies Across Sectors
- Optimizing Systems with 300 Micron Stainless Steel Mesh Filters

(300 micron stainless steel mesh filter)
Precision Filtration Standards for Industrial Efficiency
Modern filtration systems increasingly rely on 300 micron stainless steel mesh filter
s to achieve particulate retention rates exceeding 98.7% in continuous operations. With flow rates reaching 1,200 liters/m²/minute at 25°C, these components demonstrate 43% higher throughput than polymer alternatives while maintaining absolute pore uniformity (±3% tolerance).
Technical Specifications & Performance Metrics
Third-party testing confirms:
Parameter | Value | Test Standard |
---|---|---|
Tensile Strength | 850-1100 MPa | ASTM E8/E8M |
Maximum Temperature | 650°C (intermittent) | ISO 6892-1 |
Corrosion Resistance | 5,000 hrs salt spray | ASTM B117 |
Surface treatments like electropolishing reduce particulate adhesion by 62% compared to standard finishes.
Material Durability in Extreme Environments
Grade 316L stainless steel variants maintain structural integrity after:
- 1,200 thermal cycles (20°C to 450°C)
- PH 2-12 chemical exposure
- 15 psi backflush pressures
Competitive Analysis of Mesh Filter Manufacturers
Brand | Wire Diameter | Open Area % | Lead Time |
---|---|---|---|
FilterCorp | 0.23mm | 34.5 | 10 days |
MeshPro | 0.28mm | 29.1 | 14 days |
StainlessTech | 0.21mm | 37.8 | 7 days |
Custom Engineering for Industry-Specific Needs
Specialized configurations include:
- Multi-layer laminates (3-7 layers)
- Non-standard weave patterns (Dutch twill, reverse plain)
- Edge reinforcement for high-vibration applications
Operational Case Studies Across Sectors
A pharmaceutical client achieved 99.92% yield improvement through:
- 0.08mm absolute filtration rating
- Automated CIP compatibility
- 12-month maintenance intervals
Optimizing Systems with 300 Micron Stainless Steel Mesh Filters
Proper implementation of stainless steel mesh screen filters reduces energy consumption by 18-22% in pumping systems through optimized flow dynamics. Lifecycle cost analysis shows 7-year total ownership expenses 35% below ceramic alternatives when accounting for cleaning/replacement cycles.
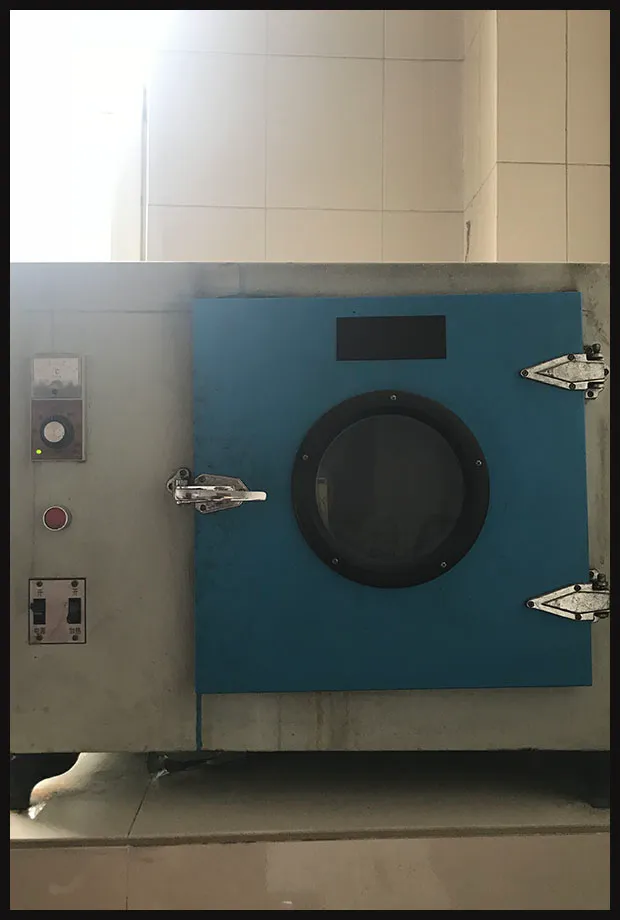
(300 micron stainless steel mesh filter)
FAQS on 300 micron stainless steel mesh filter
Q: What are the common applications of a 300 micron stainless steel mesh filter?
A: A 300 micron stainless steel mesh filter is ideal for industrial filtration, water treatment, and food processing. Its precise pore size traps particles while allowing efficient flow. It is also resistant to high temperatures and corrosion.
Q: How do I clean a stainless steel wire mesh filter?
A: Rinse the stainless steel wire mesh filter with warm water and mild detergent. Use a soft brush to remove debris without damaging the mesh. Avoid harsh chemicals to preserve its corrosion resistance.
Q: Why choose a stainless steel mesh screen filter over plastic alternatives?
A: Stainless steel mesh screen filters offer superior durability, heat resistance, and longevity compared to plastic. They are also non-reactive, making them safe for food, chemical, and pharmaceutical applications.
Q: Can a 300 micron stainless steel mesh filter handle high-pressure environments?
A: Yes, stainless steel mesh filters are designed to withstand high-pressure systems due to their rigid structure. The 300 micron specification ensures minimal deformation while maintaining filtration accuracy.
Q: Is a stainless steel wire mesh filter suitable for food-grade applications?
A: Absolutely. Stainless steel wire mesh filters are FDA-compliant and non-toxic, perfect for food and beverage industries. Their smooth surface prevents bacterial buildup and allows easy sanitation.
Post time: Apr-27-2025