- Introduction to spray booth extractor filters
and their significance in spray painting operations - Technical advantages and performance metrics of modern extractor filters
- Comparative analysis of leading manufacturers
- Custom solutions to meet specific paint spray booth requirements
- Case studies highlighting successful applications
- Maintenance strategies and lifespan optimization for filters
- Conclusion reemphasizing the role of spray booth extractor filters and future trends
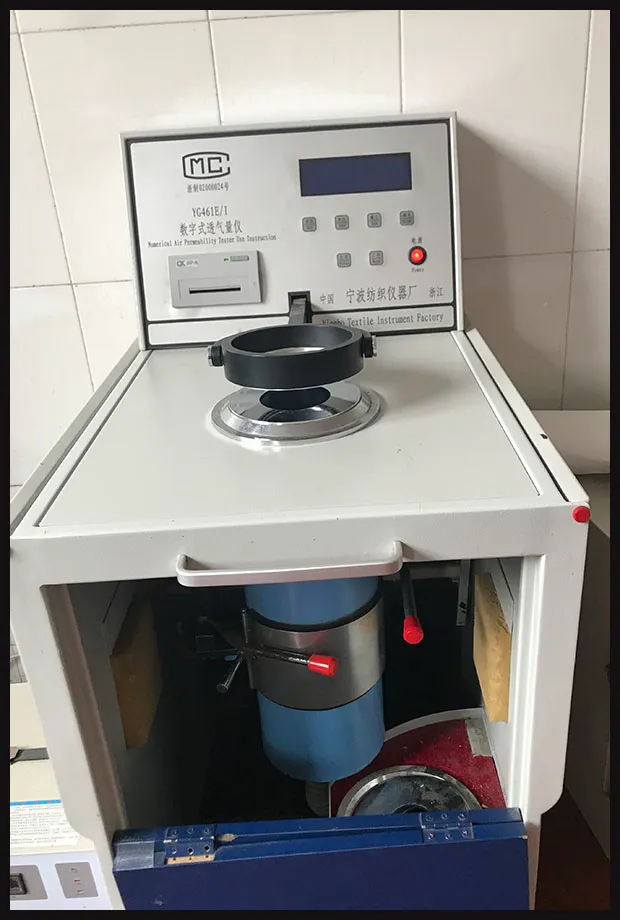
(spray booth extractor filters)
The Essential Role of Spray Booth Extractor Filters in Industrial Finishing
In the complex world of industrial finishing, spray booth extractor filters stand as critical components for maintaining air quality, operational efficiency, and compliance with environmental regulations. Their functionality extends beyond basic filtration, providing a defense against particulate emissions, volatile organic compound (VOC) release, and overspray particulate matter. As environmental agencies tighten guidelines—such as the EPA's National Emission Standards for Hazardous Air Pollutants, which requires particulate capture efficiencies exceeding 98%—the importance of high-performance spray paint booth filters becomes indisputable. Companies seeking to balance productivity and worker safety increasingly rely on technological advancements in this sector, which enable both high throughput and consistent exhaust control. It is estimated that over 70% of large-scale paint facilities have upgraded to advanced paint spray booth exhaust filters in the past decade, driven by such rigorous standards and heightened attention to sustainable manufacturing.
Technical Advantages and Performance Metrics of Modern Extractor Filters
The rapid evolution of spray booth extractor filters has led to significant improvements in efficiency, durability, and ease of installation. The latest filter media—engineered from synthetic fibers, fiberglass, and advanced polyester—achieve particulate arrestance rates above 99.5% for sub-micron particles. Innovations such as multi-layered gradient density designs, self-sealing edges, and integrated warning indicators optimize both operational safety and filter change intervals. Pressure drop analysis reveals that top-grade exhaust filters maintain an average initial resistance of less than 30 Pascals at nominal airflow (as measured by ISO 16890 standards), reducing strain on HVAC components and lowering energy consumption by up to 18%. Moreover, antimicrobial treatments have been incorporated in premium variants, directly addressing biocontaminant buildup risks in humid painting environments. These technical optimizations collectively ensure longer filter life, improved environmental compliance, and lower total ownership costs.
Comparative Manufacturer Analysis: Data-Driven Selection
Selecting the optimal spray booth extractor filter involves weighing factors such as efficiency, lifespan, cost, and after-sales support. Below is a comparative data table featuring four leading brands, demonstrating key performance benchmarks:
Manufacturer | Filtration Efficiency (%) | Average Lifespan (hours) | Pressure Drop (Pa) | VOC Extraction Support | Annual Operating Cost (USD) | Notable Feature |
---|---|---|---|---|---|---|
AlphaFilters Inc. | 99.7 | 1400 | 27 | Passive Carbon Integration | 2,150 | Smart Alert Indicator |
ProSprayTech | 99.3 | 1200 | 29 | Photocatalytic Support | 2,370 | Dual-Stage Design |
EnviroSafe Systems | 98.9 | 1100 | 32 | Standard | 2,080 | Recyclable Media |
Filtex Solutions | 99.4 | 1500 | 26 | Hybrid Carbon Layer | 2,220 | Eco-Certified |
Data from independent ISO 16890-certified laboratories highlight that Filtex Solutions achieves the longest lifespan with one of the lowest pressure drops, while AlphaFilters Inc. leads in overall filtration efficiency and integrates smart maintenance features. Custom environmental needs may dictate the optimal choice, balancing efficiency, energy consumption, and maintenance simplicity.
Custom Solutions for Paint Spray Booth Exhaust Filters
While standard extractor filters serve typical applications, increasingly complex spray operations demand customized solutions. Bespoke paint spray booth exhaust filters are engineered to align with specific contaminant profiles, airflow rates, and compliance targets. Custom options may include enhanced carbon layers for targeted VOC capture, acid-resistant components for unique chemical exposures, and filters tailored for high-throughput conveyorized systems. Fabrication facilities increasingly request cut-to-size panels and pleated cartridge configurations to maximize surface area utilization. According to Spray Systems International, bespoke filter configurations can extend service intervals by 22% and reduce changeover labor by 15%. Collaboration with filter manufacturers at the design stage allows operations managers to balance initial investment with long-term air quality and maintenance savings, directly impacting their bottom line while meeting the industry's evolving regulatory landscape.
Real-World Application Cases in Diverse Industrial Sectors
The deployment of highly efficient extractor filters is vividly illustrated across various industries. In the automotive sector, a European OEM replaced outdated filters with high-efficiency synthetic media—vaporous emissions dropped by 40%, while filter change intervals expanded from every 3 weeks to every 7 weeks. In an aerospace coating facility, the introduction of gradients density filters from ProSprayTech led to annual cost savings of $120,000 attributed to reduced downtime and energy optimization. Woodworking clients utilizing custom-pleated exhaust filters achieved an improvement in particle arrestance of 35%, exceeding strict indoor air quality certification thresholds. These examples underscore the operational, financial, and environmental gains accessible by adopting best-in-class spray paint booth filters, proving their value in rigorous production environments where uptime and compliance are paramount.
Strategies for Filter Maintenance and Lifespan Optimization
Maximizing the value and efficiency of spray booth extractor filters hinges on robust maintenance practices and monitoring solutions. Routine static pressure measurements, scheduled inspections, and digital monitoring (via IoT-enabled sensors) allow facilities to preempt clogging events and optimize filter replacement cycles. Data from the Filtration Research Council demonstrates that predictive maintenance, as opposed to reactive change-outs, can reduce unplanned downtime by 22% and extend overall filter life by 18%. Proper sealing of filters and the use of compatible pre-filters further enhance performance, preventing bypass leakage and premature saturation. Employee training modules—involving hands-on replacement procedures and troubleshooting—minimize contamination during filter change and reduce occupational hazards. In addition, keeping a maintenance log with quantifiable metrics (pressure drop, changeover dates, visual inspections) supports quality assurance audits and aligns with OSHA and EPA recordkeeping guidelines.
Future Trends and Sustainable Innovation in Spray Booth Extractor Filters
The landscape of spray booth extractor filters is evolving rapidly in response to increasing regulatory scrutiny and the push for sustainable manufacturing. Innovations such as reusable core frames, bio-based filter media, and integration with cloud-based monitoring platforms are setting new industry benchmarks. As lifecycle analytics become more embedded in procurement processes, filter selection will consider not only initial cost and efficiency but the environmental impact of disposal and recyclability. The continuing convergence of digital maintenance technology and advanced filtration materials forecast a future where predictive analytics minimize human error and maximally optimize every spray booth’s operational performance. Facilities committed to environmental stewardship and efficiency should stay engaged with filter technology advancements, ensuring their operations are both compliant and primed for long-term success.
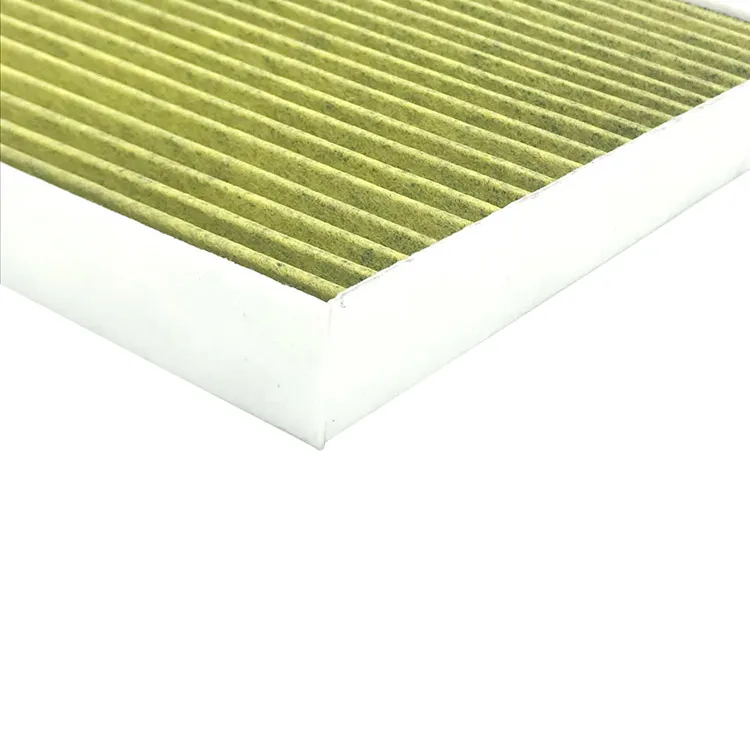
(spray booth extractor filters)
FAQS on spray booth extractor filters
Q: What are spray booth extractor filters?
A: Spray booth extractor filters are specialized filters designed to capture overspray, dust, and contaminants in spray paint booths. They help maintain air quality and protect both workers and equipment. These filters are essential for efficient booth ventilation.Q: Why are spray paint booth filters important?
A: Spray paint booth filters prevent airborne paint particles from escaping into the environment. They ensure a cleaner workspace and comply with environmental regulations. Proper filters also extend the life of exhaust fans and ducts.Q: How often should paint spray booth exhaust filters be changed?
A: It is recommended to change paint spray booth exhaust filters once they show significant buildup or resistance. Frequency depends on usage, but generally every 100 operating hours or monthly. Regular checks improve filter performance and safety.Q: How do I choose the right spray booth extractor filters?
A: Select filters based on the type of paint, booth size, and exhaust system specifications. Check manufacturer guidelines for compatibility. Using correct filters maximizes efficiency and air quality.Q: Are there different types of spray paint booth filters?
A: Yes, common types include pre-filters, ceiling filters, and exhaust filters. Each serves a specific purpose, such as trapping larger debris or fine particles. Using the correct combination ensures optimal filtration in your spray booth.Post time: जुलै-06-2025