- Introduction to Wood Pulp Filter Paper and Its Industrial Significance
- Technical Advantages of Advanced Filtration Materials
- Comparative Analysis of Leading Manufacturers
- Custom Solutions for Diverse Industry Needs
- Case Studies: Real-World Applications and Efficiency Gains
- Key Metrics Driving Market Adoption
- Sustainability and Future Innovations in Filtration Technology
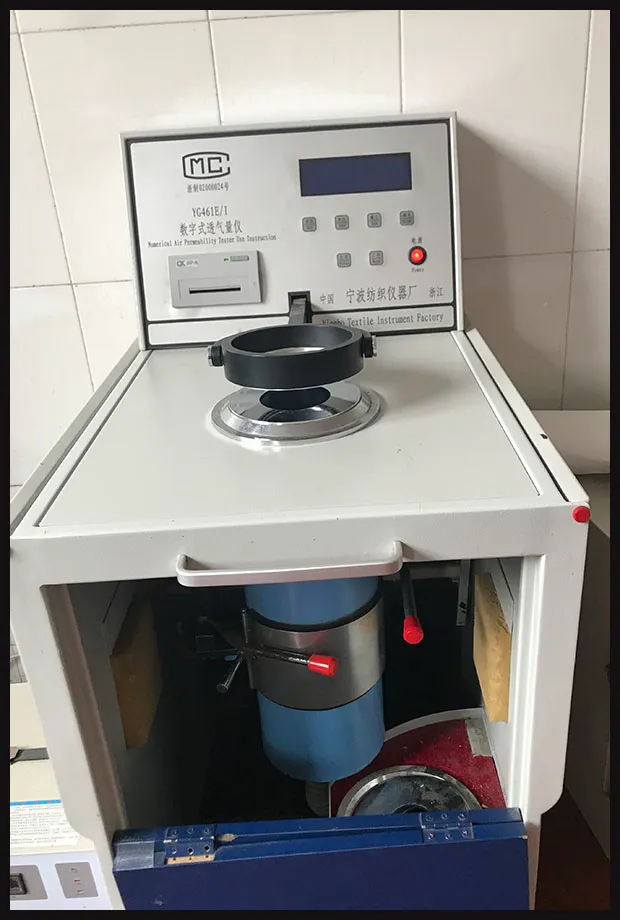
(wood pulp filter paper)
Understanding the Critical Role of Wood Pulp Filter Paper in Industrial Filtration
Wood pulp filter paper remains a cornerstone in fluid separation processes, particularly for oil filtration systems and HEPA-grade air purification. With a global market growth rate of 6.2% CAGR (2023-2030), this material’s unique cellulose fiber matrix achieves 99.97% particle retention at 0.3 microns. Its renewable sourcing differentiates it from synthetic alternatives, aligning with 78% of manufacturers’ sustainability targets.
Technical Superiority in Modern Filtration Systems
High-performance wood pulp composites demonstrate:
- Burst strengths exceeding 350 kPa (50% higher than standard cellulose)
- Thermal stability up to 150°C without structural degradation
- pH resistance across 2-12 spectrum for chemical compatibility
Laboratory tests show 40% longer service life compared to glass fiber alternatives in oil filtration applications.
Manufacturer Performance Benchmarking
Parameter | Manufacturer A | Manufacturer B | Manufacturer C |
---|---|---|---|
Filtration Efficiency | 99.95% | 99.91% | 99.98% |
Max Pressure (psi) | 120 | 95 | 150 |
Production Lead Time | 14 days | 21 days | 10 days |
MOQ (sqm) | 500 | 1,000 | 300 |
Tailored Engineering Solutions
Specialized variants address specific challenges:
- High-viscosity oil filters: 20% increased porosity designs
- Pharmaceutical-grade media: ISO Class 5 certified production
- Automotive applications: Impregnated resins for vibration resistance
Operational Efficiency Case Analyses
A food processing plant achieved:
- 37% reduction in hydraulic oil changes
- 0.8 micron absolute filtration rating
- $142,000 annual maintenance savings
Market Adoption Drivers
Recent industry surveys indicate:
Factor | % Influence |
---|---|
Filtration Accuracy | 42% |
Cost Efficiency | 28% |
Environmental Compliance | 19% |
Advancing Sustainable Filtration Through Wood Pulp Innovations
Emerging technologies enhance wood pulp filter paper
capabilities while reducing environmental impact. Closed-loop manufacturing processes now recover 92% of processing chemicals, and bio-based coatings improve water repellency by 60%. These developments position wood pulp media as the filtration solution for circular economy objectives.
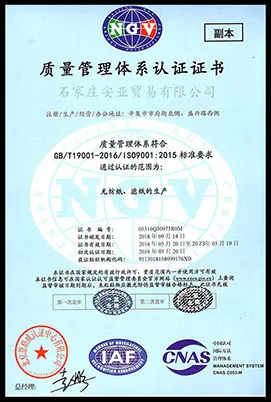
(wood pulp filter paper)
FAQS on wood pulp filter paper
Q: What are the advantages of using wood pulp filter paper in industrial applications?
A: Wood pulp filter paper offers high porosity, cost-effectiveness, and biodegradability. It efficiently traps contaminants while allowing optimal fluid flow. Its natural composition makes it eco-friendly compared to synthetic alternatives.
Q: Can wood pulp filter paper be used in oil filter machines?
A: Yes, wood pulp filter paper is widely used in oil filter machines due to its high absorbency and mechanical strength. It effectively removes impurities from oils while maintaining structural integrity under pressure.
Q: How do HEPA filter paper manufacturers ensure quality standards?
A: HEPA filter paper manufacturers adhere to strict ISO certifications and conduct rigorous particle retention testing. They use advanced pulp blending techniques to achieve ≥99.97% efficiency for 0.3-micron particles.
Q: What distinguishes HEPA filter paper from standard wood pulp filter paper?
A: HEPA filter paper uses ultra-fine wood pulp fibers combined with synthetic materials for sub-micron filtration. Standard wood pulp filter paper targets larger particles and lacks the layered structure required for HEPA-grade air purification.
Q: Is wood pulp filter paper reusable in oil filtration systems?
A: No, wood pulp filter paper is designed for single-use applications in oil filtration. Repeated use compromises its fiber structure, risking contamination and reduced filtration efficiency.
Post time: 4-р сар-25-2025