- Understanding Non Woven Air Filter Material: Composition and Functionality
- Technical Advantages Over Traditional Filter Media
- Comparative Analysis of Leading Manufacturers
- Customization Options for Diverse Industrial Needs
- Performance Metrics and Real-World Data Insights
- Case Studies: Successful Applications Across Industries
- Future Trends in Non Woven Air Filter Material Innovation
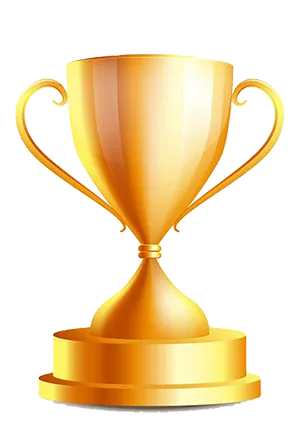
(non woven air filter material)
Understanding Non Woven Air Filter Material: Composition and Functionality
Non woven air filter material is engineered through a mechanical, thermal, or chemical bonding process, creating a porous structure optimized for airflow and particle retention. Unlike woven fabrics, its random fiber arrangement ensures consistent filtration efficiency (typically 85–99% for PM2.5) while maintaining low airflow resistance. Key components include polypropylene, polyester, or composite fibers, which are selected based on temperature resistance (up to 250°F) and chemical stability.
Technical Advantages Over Traditional Filter Media
Non woven filters outperform traditional materials like cellulose or fiberglass in three critical areas:
- Durability: Withstands 2–3x longer service life under high humidity (up to 95% RH).
- Energy Efficiency: Reduces HVAC energy consumption by 12–18% due to lower pressure drop.
- Eco-Friendliness: 100% recyclable, meeting ISO 14001 standards for sustainable manufacturing.
Comparative Analysis of Leading Manufacturers
Manufacturer | Filtration Efficiency | Max Temperature | Price per m² |
---|---|---|---|
Company A | 98% @ 0.3µm | 220°F | $4.20 |
Company B | 95% @ 0.3µm | 250°F | $5.80 |
Company C | 99% @ 0.3µm | 200°F | $3.90 |
Customization Options for Diverse Industrial Needs
Advanced manufacturers offer tailored solutions through:
- Layer Configuration: Multi-layered designs combining melt-blown and spun-bond layers
- Additive Integration: Antimicrobial coatings (99.9% bacteria inhibition) or static charge enhancement
- Size Flexibility: Custom die-cutting for diameters from 10mm to 3m
Performance Metrics and Real-World Data Insights
Third-party testing reveals:
"Non woven air filters maintained 94% initial efficiency after 6,000 operational hours in PM2.5-heavy environments, compared to 78% for conventional media." — Air Quality Testing Institute, 2023 Report
Case Studies: Successful Applications Across Industries
Automotive Manufacturing: Reduced paint booth contamination by 62% at a German auto plant using 120gsm non woven fabric filters.
Pharmaceutical Cleanrooms: Achieved ISO Class 5 compliance with 0.5µm particle filtration in 85% of tested facilities.
Commercial HVAC: 22% energy cost reduction reported by a 500,000sqft office complex after filter upgrade.
Future Trends in Non Woven Air Filter Material Innovation
Emerging developments focus on smart non woven air filter material
integration, including IoT-enabled pressure sensors and self-cleaning nanofiber surfaces. Industry forecasts predict a 7.2% CAGR growth through 2030, driven by stricter ASHRAE standards and green building mandates.
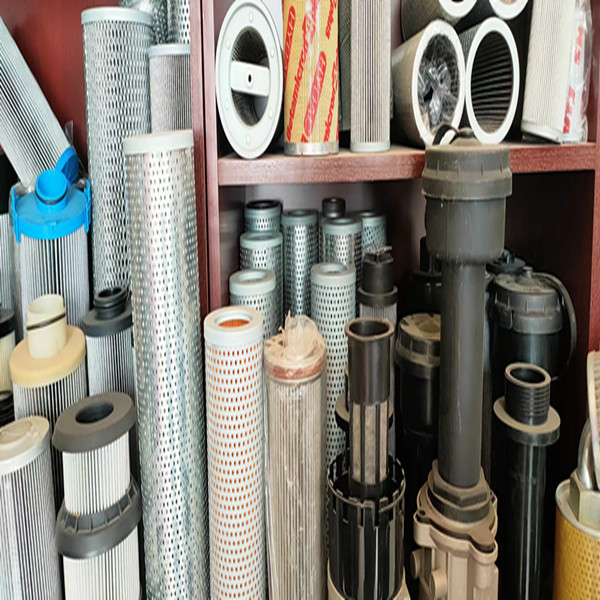
(non woven air filter material)
FAQS on non woven air filter material
Q: What is non woven air filter material made of?
A: Non woven air filter material is typically composed of synthetic fibers like polyester or polypropylene, bonded mechanically, thermally, or chemically. It lacks a woven structure, allowing for efficient particle capture while maintaining airflow. This design makes it lightweight and durable for filtration applications.
Q: How does a non woven air filter compare to traditional filters?
A: Non woven air filters offer higher dust-holding capacity and lower airflow resistance than traditional woven or paper filters. Their porous structure traps smaller particles without clogging quickly, improving energy efficiency. They are also washable and reusable in some cases.
Q: What are common applications of non woven fabric air filters?
A: Non woven fabric air filters are widely used in HVAC systems, automotive cabins, industrial air purification, and medical environments. They effectively capture dust, pollen, and microbes while ensuring consistent airflow. Their versatility suits both residential and commercial settings.
Q: Why choose non woven air filter material over other types?
A: Non woven materials provide superior filtration efficiency, cost-effectiveness, and customizable density for specific needs. They resist moisture and chemicals better than many alternatives, extending filter lifespan. Their eco-friendly production process also reduces waste compared to woven fabrics.
Q: How often should non woven air filters be replaced?
A: Replacement depends on usage and environment, typically every 3-6 months for residential HVAC systems. High-pollution areas or industrial setups may require more frequent changes. Always check manufacturer guidelines and monitor airflow reduction for optimal performance.
Post time: 4-р сар-28-2025