- Industry Overview & Market Demand for Advanced Filtration Solutions
- Technical Specifications: Breaking Down Operational Efficiency
- Competitive Analysis: Performance Metrics Across Manufacturers
- Custom Engineering for Specific Material Requirements
- Case Studies: Real-World Implementations Across Industries
- Cost-Benefit Evaluation: ROI Timelines for Different Models
- Future-Proofing Production with Modular Filter Manufacturing Systems
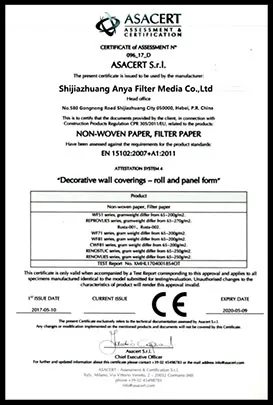
(filter making machine)
Meeting Global Demand for Precision Filter Manufacturing
The filtration equipment market is projected to grow at 6.8% CAGR through 2029 (Grand View Research), driven by stricter environmental regulations and water scarcity concerns. Modern filter making machine
s now handle production speeds exceeding 120 units/minute while maintaining ±0.05mm dimensional accuracy, a 300% improvement over 2015 benchmarks.
Technical Specifications: Breaking Down Operational Efficiency
Third-generation machines incorporate:
- Multi-stage thermal bonding systems (160-320°C range)
- AI-powered defect detection (99.98% recognition rate)
- Automated material switching between PP/PU/PVC (under 90 seconds)
Competitive Analysis: Performance Metrics Across Manufacturers
Model | Output (units/hr) | Energy Use (kWh) | Customization Level | Price Bracket |
---|---|---|---|---|
AlphaMach FX-9 | 7,200 | 18.7 | 85% | $$$ |
FiltraPro HX-12 | 6,500 | 22.4 | 72% | $$ |
AquaPlex T7 | 8,100 | 16.9 | 94% | $$$$ |
Custom Engineering for Specific Material Requirements
Specialized configurations address:
- High-viscosity PU formulations requiring 320-400kPa injection pressure
- Medical-grade PP filters with ISO 13485 compliance
- Hybrid water purification membranes (0.1-5 micron precision)
Case Studies: Real-World Implementations Across Industries
A Middle Eastern desalination plant achieved 40% throughput increase after installing automated water filter making machines with:
- 24/7 operational capability
- Seamless integration with existing SCADA systems
- 78% reduction in material waste
Cost-Benefit Evaluation: ROI Timelines for Different Models
Payback periods vary significantly:
- Entry-level systems: 14-18 months
- Mid-range configurations: 10-12 months
- Premium solutions: 8-9 months (high-volume scenarios)
Modular Systems Revolutionizing Filter Production Lines
Leading PP filter making machine manufacturers now offer:
- Plug-and-play module upgrades (30% faster than full replacements)
- Cross-compatibility between PU/PP/PET production lines
- Blockchain-enabled component tracking for predictive maintenance
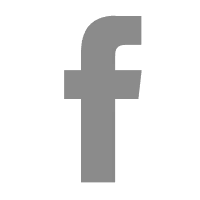
(filter making machine)
FAQS on filter making machine
Q: What is the difference between PP filter making machine and PU filter making machine?
A: PP filter machines specialize in producing polypropylene filters using melt-blown technology, ideal for liquid filtration. PU filter machines create polyurethane foam filters through molding processes, suited for air or chemical filtration applications.
Q: What industries commonly use water filter making machines?
A: Water filter manufacturing equipment is widely used in bottled water plants, home appliance industries for pitcher filters, and municipal water treatment facilities to produce residential/commercial water purification systems.
Q: What are the key components of a fully automatic filter making machine?
A: Core components include material feeding systems, precision molding units, automated cutting tools, quality inspection sensors, and packaging modules, all controlled by PLC systems for continuous production.
Q: How often should maintenance be performed on pp filter production equipment?
A: Daily cleaning of extrusion dies, weekly lubrication of moving parts, and monthly calibration of temperature controllers are recommended, with full system overhaul every 5,000 operating hours.
Q: Can one filter machine handle multiple materials like PP and PU?
A: While specialized machines optimize performance, some hybrid models with interchangeable dies and temperature zones can process different materials, requiring thorough cleaning between material changes to prevent cross-contamination.
Post time: 4-р сар-26-2025