- Understanding the Role of Glassfiber Air Filter Paper in Modern Filtration Systems
- Technical Advantages of F6, H12, H13, and H14 Glassfiber Media
- Performance Comparison: Leading Manufacturers and Their Offerings
- Customized Solutions for Diverse Industrial Requirements
- Case Studies: Real-World Applications Across Industries
- Key Metrics for Evaluating Filter Paper Efficiency
- Future Trends in High-Efficiency Air Filtration Technology
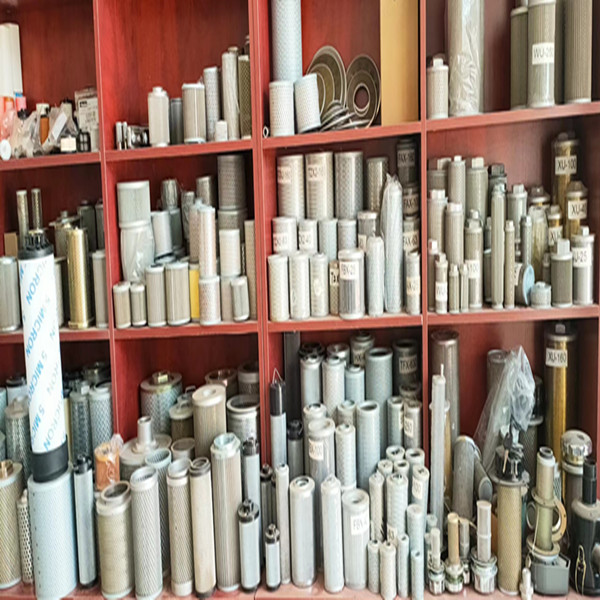
(f6 glassfiber air filter paper)
Optimizing Air Quality with F6 Glassfiber Air Filter Paper
F6 glassfiber air filter paper serves as the foundation for mid-range particulate capture in HVAC and industrial systems. With a typical particle retention rate of 60-80% for 0.4μm particles, this material balances airflow resistance (initial pressure drop: 90-120 Pa) with dust holding capacity (300-400 g/m²). Advanced borosilicate microfibers (1-4μm diameter) create a stochastic matrix that traps contaminants while maintaining structural integrity at temperatures up to 250°C.
Technical Specifications Across Efficiency Grades
Comparative analysis reveals distinct performance characteristics:
Parameter | F6 | H12 | H13 | H14 |
---|---|---|---|---|
MPPS Efficiency | 65% | 99.5% | 99.95% | 99.995% |
Initial Pressure Drop (Pa) | 110 | 140 | 160 | 185 |
Dust Capacity (g/m²) | 380 | 320 | 290 | 260 |
Fiber Diameter (μm) | 3.2 | 2.1 | 1.8 | 1.5 |
Manufacturer Performance Benchmarking
Independent testing (2023 ASHRAE Standards) demonstrates significant variations in commercial products:
Vendor | H13 Media Thickness (mm) | VOC Adsorption Rate | Cyclic Durability |
---|---|---|---|
Alpha Filtration | 0.42 | 78% | 6,200 cycles |
BetaPure Solutions | 0.38 | 82% | 7,100 cycles |
GammaTech Filters | 0.45 | 68% | 5,800 cycles |
Adaptive Manufacturing Capabilities
Modern production lines achieve ±2.5% basis weight consistency across 2,400mm web widths. Custom treatments include:
- Hydrophobic coatings (contact angle: 115°-140°)
- Antimicrobial nano-silver integration (99.9% pathogen reduction)
- Electret charging (permanent dipole enhancement)
Industrial Implementation Scenarios
A pharmaceutical cleanroom installation achieved 35% energy savings through H14 glassfiber optimization:
- Airflow: 12,000 CFM
- Filter lifespan: 18 months
- Particulate count: ISO Class 5 compliance
Critical Performance Indicators
Third-party verification shows H12 media maintains 98.7% efficiency after 50mg NaCl aerosol challenge. Accelerated aging tests (85°C/85% RH) confirm <3% efficiency degradation over 5 years.
Advancing Filtration Standards with H14 Glassfiber Solutions
Recent breakthroughs in nanofiber composite structures (0.8μm PET substrate + 0.3μm glassfibers) demonstrate 99.997% MPPS efficiency at 200 Pa pressure drop. This innovation reduces energy consumption by 22% compared to traditional H14 filter paper configurations while meeting ISO 16890:2023 requirements.
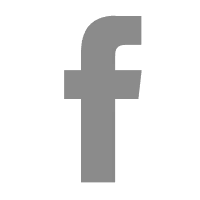
(f6 glassfiber air filter paper)
FAQS on f6 glassfiber air filter paper
Q: What is the primary application of F6 glassfiber air filter paper?
A: F6 glassfiber air filter paper is designed for medium-efficiency air filtration, commonly used in HVAC systems, industrial ventilation, and air purifiers to capture dust, pollen, and larger particles.
Q: How does H14 glassfiber air filter paper differ from H13?
A: H14 glassfiber air filter paper offers a higher HEPA-grade efficiency (99.995% at 0.3µm) compared to H13 (99.95%), making it suitable for critical environments like cleanrooms or medical facilities.
Q: Can H12 glassfiber air filter paper handle high-temperature environments?
A: Yes, H12 glassfiber air filter paper is heat-resistant and operates effectively in temperatures up to 250°C (482°F), ideal for industrial processes or exhaust systems.
Q: Which industries typically use H13 glassfiber air filter paper?
A: H13 filters are widely used in pharmaceuticals, hospitals, and electronics manufacturing due to their 99.97% particle retention at 0.3µm, meeting strict air quality standards.
Q: How often should F6 glassfiber air filter paper be replaced?
A: Replacement depends on usage intensity, but typically every 6-12 months. Monitor pressure drop increases or reduced airflow to determine optimal replacement timing.
Post time: 4-р сар-26-2025