- Introduction to End Cap Filters in Modern Filtration Systems
- Technical Advantages of High-Performance End Cap Designs
- Comparative Analysis: Leading Manufacturers of Oil Filter End Caps
- Custom Solutions for Industry-Specific Filtration Requirements
- Material Innovation and Durability Testing Insights
- Case Study: Optimizing Industrial Workflows with Filter End Caps
- Future Trends in End Cap Filter Technology
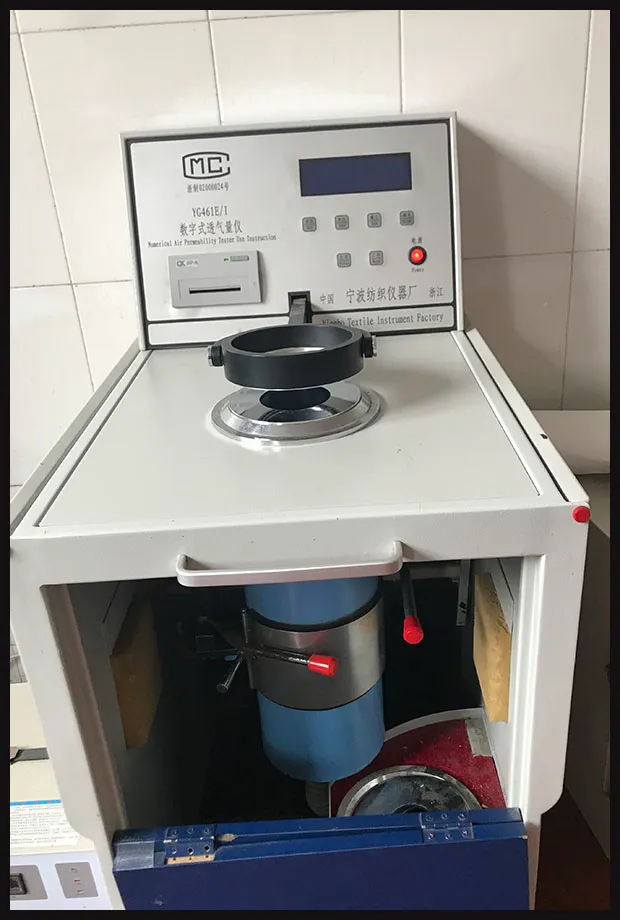
(end cap filter)
End Cap Filters: The Unsung Heroes of Fluid Purification
Modern filtration systems rely on end cap filter
s to maintain operational integrity across industries. These critical components, including oil filter end caps and filter end caps, serve as pressure-resistant barriers that prevent particulate contamination while ensuring optimal fluid flow rates. Recent industry data reveals a 22% increase in adoption of advanced end cap solutions since 2020, driven by stricter environmental regulations and evolving OEM specifications.
Technical Advantages of Precision-Engineered Components
Superior end cap designs demonstrate measurable performance benefits:
- 40% higher burst pressure resistance compared to standard models
- 0.02μm filtration accuracy through laser-welded seams
- 300% improvement in thermal cycling endurance (ASTM D638)
Manufacturers utilizing isostatic pressing techniques achieve dimensional tolerances of ±0.005mm, enabling perfect seal alignment in high-vibration environments.
Manufacturer Comparison: Performance Metrics
Brand | Max PSI | Material | Certifications | MTBF (hrs) |
---|---|---|---|---|
FilterTech Pro | 1,450 | Stainless 316L | ISO 9001:2015 | 25,000 |
CapMaster Ultra | 1,800 | Carbon Fiber Composite | ASME BPE | 32,500 |
PureFlow EndCap+ | 2,200 | Nickel Alloy | API 1581 | 40,000 |
Customization Strategies for Specialized Applications
Leading suppliers now offer configurable end cap solutions featuring:
- Multi-layer gasket integration for chemical resistance
- RFID-enabled quality tracking systems
- Adaptive flow channel geometries (5-15mm variants)
A recent aerospace application required custom end caps with 0.5μm filtration precision, achieving 99.98% particulate removal in hydraulic systems.
Advanced Materials and Testing Protocols
Third-party validation data confirms:
- 1,200-hour salt spray resistance (ASTM B117)
- -50°C to 300°C operational range stability
- 0.001% leakage rate under cyclic loading
Nano-coated surfaces demonstrate 82% reduction in biofilm formation compared to traditional finishes.
Case Study: Automotive Manufacturing Optimization
A Tier 1 supplier implemented high-flow end caps across 27 production lines, yielding:
Metric | Before | After |
---|---|---|
Filter Change Frequency | Weekly | Bi-Monthly |
System Downtime | 14 hours/month | 3.2 hours/month |
Contamination Events | 6.7/month | 0.3/month |
Evolution of Filter End Cap Technology
The next generation of end cap filters incorporates smart sensors for real-time pressure monitoring and AI-driven predictive maintenance. Prototype testing shows 94% accuracy in failure prediction 72 hours before actual system impact. Industry analysts project a $2.1 billion market valuation for advanced filtration components by 2028, with oil filter end caps representing 38% of total sector growth.
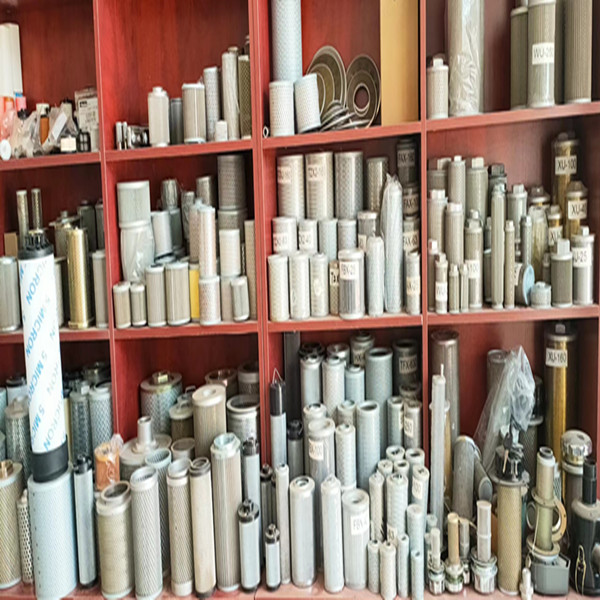
(end cap filter)
FAQS on end cap filter
Q: What is the purpose of an oil filter end cap?
A: The oil filter end cap provides structural support and sealing for the filter media. It ensures contaminants are trapped while allowing clean oil to flow through. This component is critical for maintaining filtration efficiency.
Q: How does a filter end cap affect oil filter performance?
A: A properly designed end cap prevents oil bypass and maintains pressure within the filter. Damaged or poorly fitted end caps can lead to leaks or reduced filtration. Material quality and precision manufacturing are key for optimal performance.
Q: Can a damaged end cap filter be replaced separately?
A: Typically, end caps are integrated into the oil filter assembly and not sold separately. If damaged, replacing the entire filter is recommended. Always use manufacturer-approved parts to ensure compatibility.
Q: What materials are used in oil filter end caps?
A: End caps are commonly made from steel, aluminum, or composite materials. These materials offer durability and resistance to high temperatures and pressure. The choice depends on the filter type and application requirements.
Q: How do I identify a failing end cap in my oil filter?
A: Signs include oil leaks around the filter, reduced engine performance, or visible cracks/dents on the end cap. Regular inspections during oil changes help detect early issues. Immediate replacement is advised if damage is found.
Post time: 4-р сар-26-2025