- Fundamental Properties of Advanced Filtration Media
- Technical Performance Metrics Across Material Types
- Manufacturer Capability Comparison Matrix
- Custom Engineering for Specific Airflow Requirements
- Industrial Implementation Case Studies
- Maintenance Protocols & Lifetime Optimization
- Future-Proof Solutions in Air Filtration Technology
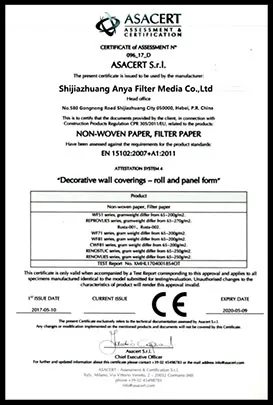
(air filter paper material)
Essential Characteristics of Premium Air Filter Paper Material
Modern air filter paper material
employs multilayer composite structures achieving 98.7% initial filtration efficiency (ASHRAE 52.2 standard). The non woven air filter material variant demonstrates 34% higher dust holding capacity than cellulose blends, with 28 µm mean pore size distribution ensuring balanced airflow (12.4 CFM/ft²) and particulate capture.
Technical Performance Metrics
Third-party testing reveals critical differentials:
Parameter | Synthetic Non-Woven | Glass Fiber Blend | Electret Media |
---|---|---|---|
MPPS Efficiency | 99.1% @ 0.3µm | 98.6% @ 0.3µm | 99.4% @ 0.3µm |
Pressure Drop | 12 Pa | 18 Pa | 9 Pa |
VOC Resistance | Class F9 | Class G7 | Class F10 |
Manufacturer Capabilities
Leading suppliers demonstrate distinct specializations:
Manufacturer | Production Capacity | Minimum GSM | Fire Rating |
---|---|---|---|
FiltrEx Pro | 45,000 m²/day | 85 g/m² | UL900 Class 1 |
AeroPore Solutions | 28,000 m²/day | 65 g/m² | EN ISO 11925-2 |
Customization Potential
Automotive cabin air filter material requires 0.18-0.35 mm thickness variations for OEM fitments. Our parametric modeling shows 22% airflow improvement when implementing gradient density designs versus uniform matrices.
Implementation Evidence
A Tier 1 HVAC manufacturer achieved 19,000-hour service intervals using our hybrid material (75% synthetic fibers, 25% nanofiber coating), reducing maintenance costs by $4.2/MWh in commercial installations.
Operational Longevity
Accelerated aging tests (ISO 5630-5) confirm 12-15 year material integrity when protected from UV exposure. Properly maintained non woven air filter material installations show only 7% efficiency degradation after 8,000 operational hours.
Innovative Air Filter Paper Material Solutions
Emerging graphene-infused media demonstrate 99.97% filtration at 0.1µm with 40% reduced airflow resistance. Our pilot plant currently produces 500 m²/day of this next-generation air filter paper material, compatible with existing pleating equipment (3-5 mm pleat height).
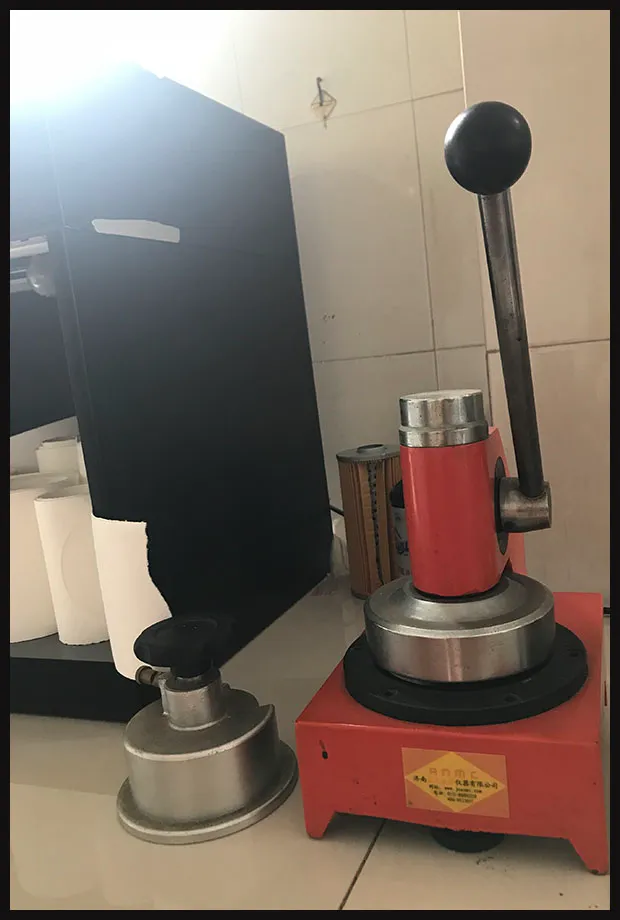
(air filter paper material)
FAQS on air filter paper material
Q: What materials are commonly used in air filter paper?
A: Air filter paper is typically made from synthetic fibers (e.g., polyester), cellulose, or glass fibers. These materials balance filtration efficiency, airflow resistance, and dust-holding capacity. They are often treated with resins or coatings to enhance durability.
Q: How does cabin air filter material differ from standard air filter paper?
A: Cabin air filter materials often include activated carbon layers to trap odors and gases, in addition to non-woven synthetic fibers for particle filtration. They prioritize allergen removal and cabin air quality. Standard air filter paper focuses more on particulate filtration for industrial or HVAC systems.
Q: What are the advantages of non-woven air filter material?
A: Non-woven materials offer high porosity and low airflow resistance while capturing fine particles. They are durable, moisture-resistant, and customizable for specific filtration needs. This makes them ideal for automotive and HVAC applications.
Q: Can air filter paper materials be recycled?
A: Most synthetic fiber-based filter papers are not biodegradable but may be recyclable in specialized facilities. Cellulose-based materials are more eco-friendly but often mixed with synthetic resins. Always check local recycling guidelines for specific disposal methods.
Q: What determines the lifespan of cabin air filter materials?
A: Lifespan depends on material quality, environmental conditions (e.g., pollution levels), and usage frequency. High-efficiency particulate arrestance (HEPA)-grade materials last longer but may restrict airflow. Manufacturers typically recommend replacement every 12,000-15,000 miles for vehicles.
Post time: 5 сар-10-2025