- Introduction to cement silo filter bags
: market overview and importance - Technical structure and innovations in silo filtration solutions
- Comparing silo filter bags and silo filter cartridge: performance and cost
- Customization options according to industrial demands
- Main manufacturers: a comparative data table
- Real-world applications and success stories
- Future trends for cement silo filter bags and industry impact
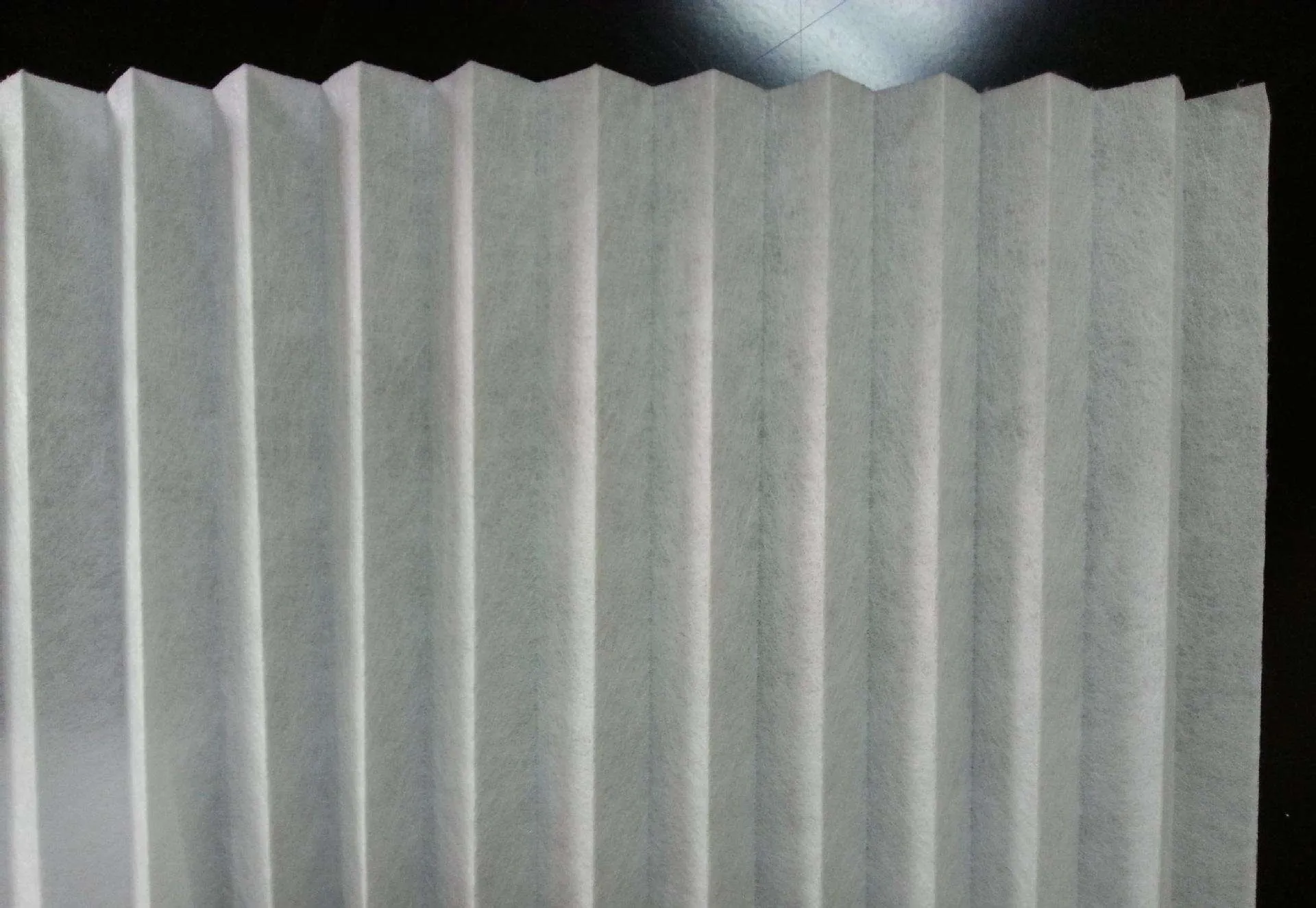
(cement silo filter bags)
Understanding Cement Silo Filter Bags in Modern Industry
In contemporary cement production and material storage industries, cement silo filter bags have emerged as a critical solution for dust filtration and environmental protection. With the global cement industry projected to grow at a 3.7% CAGR from 2024 to 2030 and compliance standards tightening, the choice and maintenance of filtration equipment such as silo filter bags are pivotal to operational efficiency and regulatory conformity. Reports indicate that effective dust collection systems can reduce particulate emissions by up to 99.97%, highlighting their substantial role in sustainable operations. The central function of these filtration systems is to capture fines and pollutants, ensuring workplace safety, machinery longevity, and reduced environmental impact. Against the backdrop of increasing automation and green initiatives, industry demand for high-performance filter bags and cartridges continues its steady rise, with innovations catering to diverse silo configurations and particulate characteristics.
Technical Advances in Silo Filtration Solutions
The technical evolution of silo filter bags and cartridges has transformed industrial dust management. Modern filter bags are fabricated from advanced synthetic fibres such as polyester, aramid, and PTFE, providing excellent chemical resistance, mechanical strength, and high operational temperatures—up to 240°C. Multilayer felt and membrane laminates have improved efficiency and extended filter life by minimizing blinding and ensuring uniform airflow. Recent innovations include antistatic surfaces, nanofibre coatings for submicron particle capture, and self-cleaning designs compatible with pulse-jet systems. Filtration efficiency metrics now routinely exceed 99.9% for most industrial dust profiles, while optimized sewing technologies reduce leakage below 2 mg/Nm³. These advances translate into lower downtime, reduced maintenance costs, and consistent compliance with environmental regulations across diverse industrial processes.
Performance and Cost: Silo Filter Bags vs Silo Filter Cartridge
When selecting between traditional silo filter bags and modern cartridge filters, decision-makers balance factors including cost, maintenance, filter area, pressure drop, and capture efficiency. Bags generally offer high dust-holding capacity, simple rehabilitation, and adaptability to large-diameter silos. Cartridges provide easy installation, compactness, and superior pulse cleaning, making them suitable for limited-space retrofits or demanding process conditions. The following table presents a comparative breakdown based on prominent technical parameters and operational data:
Feature | Silo Filter Bags | Silo Filter Cartridge |
---|---|---|
Typical Filtration Efficiency | 99.7% (PM2.5) | 99.95% (PM1) |
Pressure Drop (Initial) | 100-120 Pa | 90-110 Pa |
Operating Life | 12-36 months | 18-48 months |
Cost (per sqm effective area) | USD 14–22 | USD 17–28 |
Maintenance Complexity | Medium | Low |
Max Operating Temperature | 220–240°C | 135°C (standard polyester) |
Typical Applications | Cement, lime, minerals | Pharmaceutical, fine powders, food batching |
The above data highlights the importance of aligning technology choice with process requirements, balancing upfront investment with lifecycle performance and compliance needs.
Customization: Tailoring Filtration to Process Needs
Each industrial installation presents unique challenges—dust particle size, humidity, chemical reactivity, temperature fluctuations, and cleaning interval expectations. Manufacturers offer a broad spectrum of customization for silo filter bags and cartridges, focusing on materials (polyester, polyamide, PPS, PTFE), surface treatment (water and oil repellency, antistatic finish), geometries (flat, star, pleated), and reinforcement features (snap bands, top/bottom flanges). State-of-the-art bag design can accommodate variances in silo diameter and air-to-cloth ratio (typically between 1.2–1.8 m³/min/m²), maximizing airflow while minimizing pressure drop. In sectors handling explosive dusts, antistatic and flame-retardant configurations mitigate risk and fulfill ATEX compliance. Furthermore, filter cartridge pleating increases usable surface area by 35–55% over equivalent bag units, optimizing cleaning cycles. Customization thus empowers facilities to both align precisely with regulatory requirements and reduce total cost of ownership.
Major Manufacturers: Data-Driven Comparison
Choosing a supplier can significantly influence filter lifespan, support quality, and total operating costs. The table below compares leading global manufacturers based on market share, innovation index, and after-sales service metrics as of 2024:
Manufacturer | Market Share (%) | Key Products | Innovation Score (0-10) | Global Distribution | After-sales Rating (1-5) |
---|---|---|---|---|---|
Donaldson Company | 16.5 | Filter Bags, Cartridges, Custom Systems | 9.2 | 80+ countries | 4.8 |
Parker Hannifin | 13.1 | Silo Filter Cartridge, HEPA Systems | 8.7 | 70+ countries | 4.6 |
BWF Group | 11.3 | High-temp Bags, Antistatic Bags | 8.9 | 60+ countries | 4.5 |
Junker Filter | 7.5 | PTFE Bags, Modular Cartridges | 8.5 | 40+ countries | 4.3 |
WAMGROUP | 6.4 | Silo Filter Bags, Bin Vent Systems | 7.6 | 60+ countries | 4.1 |
These metrics can inform procurement strategies, particularly where technical support, rapid delivery, and international compliance documentation are priorities.
Application Cases: Proven Performance in the Field
Successful real-world implementations of silo filter bags enhance trust and underscore measurable impact. For example, a leading cement plant in India upgraded its dust collection with aramid filter bags featuring PTFE membranes—reducing emission levels from 38 mg/Nm³ to just 9 mg/Nm³ and cutting maintenance downtime by 25% annually. In Europe, a precast concrete manufacturer adopted pleated filter cartridges, decreasing energy consumption in their reverse air system by 17% and extending change-out intervals to over three years. Another case in Southeast Asia saw the implementation of antistatic bags in a facility handling highly explosive rice-husk ash; this resulted in a zero-incident record for 48 months. These applications illustrate the synergy between technical specifications and operational context, emphasizing the value of data-driven selection and ongoing monitoring.
Outlook: Trends and Opportunities for Cement Silo Filter Bags
The future of cement silo filter bags is defined by sustainability, digitalization, and industry-wide regulatory shifts. As particulate emission limits grow more stringent—falling below 5 mg/Nm³ in many regions—ongoing material science breakthroughs and smart sensor integration enable predictive maintenance, further slashing costs by up to 30%. The rise of circular economy initiatives prompts the adoption of recyclable materials and end-of-life reclamation schemes. Automated monitoring and AI-optimized cleaning cycles provide unprecedented operational transparency, driving down unplanned downtime. In essence, the sector's trajectory leans toward adaptive solutions that meet stringent environmental mandates while advancing manufacturing efficiency. For operators and procurement specialists, staying ahead necessitates vigilant evaluation of filter bag and cartridge technologies, ensuring both compliance and operational excellence in the evolving industrial landscape.

(cement silo filter bags)
FAQS on cement silo filter bags
Q: What are cement silo filter bags used for?
A: Cement silo filter bags are used to capture dust and fine particles generated during cement handling and storage. They help maintain air quality and comply with environmental standards. Proper filtration ensures efficient silo operation.Q: How often should silo filter bags be replaced?
A: Silo filter bags should typically be replaced every 6 to 12 months, depending on usage and dust load. Routine inspections can help determine if bags are clogged or damaged. Timely replacement maintains optimal filtration efficiency.Q: What is the difference between silo filter bags and a silo filter cartridge?
A: Silo filter bags are flexible fabric filters, while silo filter cartridges are usually rigid, pleated cylinders. Cartridges often provide higher filtration area in a compact space. Both are designed for dust collection but may suit different systems.Q: Can cement silo filter bags be cleaned and reused?
A: Some cement silo filter bags can be cleaned and reused if they're designed for it and not severely worn or damaged. Regular cleaning extends the lifespan and efficiency. Always follow the manufacturer's recommendations.Q: Are all silo filter bags compatible with any silo system?
A: Not all silo filter bags suit every silo system; they vary by size, material, and fitting method. Always verify compatibility with your equipment's specifications. Using the wrong type can reduce filtration performance.Post time: ജുലാ-06-2025