- Introduction to filter pleating machine
s and their industrial significance - Technological advancements and operational benefits
- Comparison of filter paper pleating machine manufacturers
- Custom solutions and design adaptations in filter pleating machinery
- Market trends and buying considerations
- Real-world case studies and application scenarios
- Conclusion: Why choosing the right filter pleating machine matters

(filter pleating machine)
Filter Pleating Machine: Transforming Filtration Manufacturing
In today's rapidly evolving industrial environment, the demand for fine-tuned filtration solutions continues to rise across sectors such as automotive, pharmaceutical, food processing, and water treatment. The filter pleating machine has established itself as an essential asset in optimizing filter element production by enabling precision, speed, and replicable quality standards for a diverse range of filter media. These machines are engineered to automate the process of folding, glue dispensing, trimming, and even hot-melt applications, vastly reducing manual labor and error.
Industries have witnessed substantial productivity increases through the integration of advanced pleating technology. According to the 2023 Global Filtration Report, pleated filter elements account for over 67% of all industrial filtration solutions, underlining the critical importance of pleating machines in current manufacturing processes. With capacities ranging up to 40 meters per minute, the latest pleating equipment allows manufacturers to meet high-output requirements while maintaining precise pleat heights and pitch tolerances as low as ±0.2mm.
Technical Breakthroughs and Performance Advantages
Technological enhancements in filter paper pleating machine design have dramatically improved both operation and maintenance. Contemporary systems are integrated with servo motors, PLC-controlled interfaces, and automated tensioning mechanisms that not only reduce set-up times but also guarantee consistent pleating across multiple filter media thicknesses and types. For instance, modern pleating equipment can seamlessly handle papers, woven mesh, synthetic nonwovens, and composite laminates.
Machines featuring automatic cutting and gluing modules achieve throughput efficiencies up to 15% higher than semi-automatic alternatives. Fault detection systems now minimize production downtime; leading manufacturers report line uptimes of 98.5% over 12-month periods—a significant improvement compared to older manual processes. Furthermore, these machines' modular designs facilitate easy upgrades and component replacements, contributing to lifecycle cost reductions averaging 23% in just five years of operation.
Comparative Analysis: Leading Filter Paper Pleating Machine Manufacturers
The global market offers a variety of filter pleating machines from a mix of established and emerging manufacturers. Selection standards primarily focus on build quality, automation levels, aftersales support, and adaptation for specific filter types. Below is a comparative table illustrating performance and service parameters among four prominent manufacturers:
Manufacturer | Pleat Speed (m/min) | Supported Media Types | Automation Level | Uptime (%) | Warranty (Years) | Global Service Centers |
---|---|---|---|---|---|---|
Precision Pleat Co. | 38 | Paper, Mesh, Nonwoven | Fully Automatic | 98.5 | 3 | 15 |
FiltraTech Industries | 32 | Paper, Synthetic | Semi-Automatic | 97.8 | 2 | 9 |
UltraPleat Systems | 40 | Paper, Mesh | Fully Automatic | 98.7 | 4 | 12 |
Springfield Filtration | 29 | Paper, Nonwoven, Synthetic | Manual/Semi-Automatic | 97.0 | 2 | 8 |
The comparison underscores not just speed or automation, but also real-world aspects such as uptime and warranty. This empowers potential buyers to match operational needs with the most suitable filter paper pleating machine manufacturers, considering factors that impact both upfront investment and ongoing productivity.
Customization: Tailoring Filter Pleating Machines to Specific Needs
No two filter manufacturing lines are identical. Customization options in filter pleating machine for sale offerings ensure a machine's features and functions align with unique production processes and final application demands. Leading manufacturers provide modular add-ons such as inline glue dispensers (for micro-pleat applications), synchronized slitting stations, and adjustable pleat-forming rollers for different pleat depths and geometries.
Bespoke programming for PLC controls can adapt pleating cycles, optimize for reduced material crumbs, or automatically integrate with cutting-edge Industry 4.0 production data systems for real-time analytics. Additionally, scalability options—ranging from single-line configurations to multi-web production setups—allow small businesses and large-scale manufacturers alike to future-proof their investments. For those requiring compliance, machines can be equipped with customizable quality control modules supporting ISO 16890 or ASHRAE 52.2 validation.
Market Dynamics and Buying Considerations
The global market for industrial pleated filters surpassed USD 6.2 billion in 2022, with continued annual growth forecast at 5.8% through 2029. Buying a filter pleating machine thus represents not only a capital investment but a strategic one that can directly influence a company's market position.
Among the factors influencing purchasing decisions are machine throughput, adaptability to evolving filter standards, energy efficiency, operator safety, and the availability of rapid-response technical support. Industry surveys indicate that 82% of buyers prioritize aftersales support and service reliability as much as the machine's capabilities. Total cost of ownership, not just initial purchase price, often provides a more accurate measure for return on investment, especially when considering energy-efficient models reduce plant energy consumption by up to 17% over legacy equipment.
Case Studies: Applications and Success Stories
To fully illustrate the impact of advanced pleating equipment, consider several real-world application cases:
- Automotive Filtration: A major Japanese automaker increased its air filter throughput by 28% and reduced defects below 0.5% after commissioning a fully automated pleating line with inline quality sensors.
- Pharmaceutical Cleanrooms: Implementing a custom pleating solution with hot-melt glue application, a European pharmaceutical supplier achieved ISO 8 compliance and cut filter assembly times in half.
- Water Filtration Plants: A municipal water authority in Brazil upgraded to a servo-driven filter paper pleating machine, resulting in 32% lower maintenance costs due to the robust, modular system design.
- HVAC Manufacturing: Transitioning from manual to automated pleating increased production consistency for a North American HVAC company, enabling successful expansion into the commercial building segment.
These examples demonstrate not just performance gains, but also elevated compliance, waste reduction, and new market opportunities that quality pleating machinery unlocks for filter producers.
Conclusion: The Critical Role of Filter Pleating Machine Selection
The long-term performance and market competitiveness of any filtration product are inextricably tied to the choice of filter pleating machine. With high-speed, automated, and customizable machinery, manufacturers can confidently ensure repeatable quality, sustained output, and rapid adaptation to future filtration standards and materials. Selecting a partner among leading filter paper pleating machine manufacturers, evaluating total ownership cost, and opting for scalable, future-ready designs together create the strategic foundation for success in the filtration industry. Thorough analysis, technical due diligence, and alignment with operational goals ultimately transform this investment from a simple equipment purchase into a key element of sustained industrial leadership.
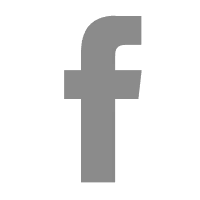
(filter pleating machine)
FAQS on filter pleating machine
Q: What is a filter pleating machine?
A: A filter pleating machine is equipment designed to fold filter media, such as paper or fabric, into pleats for filters. It automates the pleating process, ensuring consistent and precise folds. This machine is essential in the manufacturing of air, oil, and water filters.Q: How do I choose a reliable filter paper pleating machine manufacturer?
A: Look for manufacturers with strong experience, positive customer feedback, and certifications. Ensure they offer after-sales support and spare parts. Comparing several suppliers can help you find the best quality and value.Q: Are there filter pleating machines for sale for small-scale production?
A: Yes, many manufacturers offer both industrial-sized and compact filter pleating machines suitable for small-scale or laboratory use. These machines are typically more affordable and easy to operate. Contact suppliers for options tailored to your production scale.Q: What types of filter media can a filter paper pleating machine handle?
A: Filter paper pleating machines can process various filter media, including paper, non-woven fabric, and synthetic fibers. The machine setup can be adjusted to accommodate different thicknesses and materials. Always verify compatibility with the manufacturer.Q: What maintenance is required for a filter pleating machine?
A: Regular cleaning, lubrication, and inspection of moving parts are necessary to ensure smooth operation. Follow the maintenance checklist provided by the manufacturer. Proper maintenance extends the life and efficiency of your pleating machine.Post time: 7월-07-2025