- Introduction to Wire Screen Filters and Their Industrial Relevance
- Technical Advantages of Stainless Steel Mesh Screen Filters
- Performance Data: Metal Mesh Screen Filters vs. Alternatives
- Manufacturer Comparison: Key Metrics and Reliability
- Custom Solutions for Diverse Industrial Needs
- Real-World Applications and Success Stories
- Future Trends in Wire Screen Filter Technology
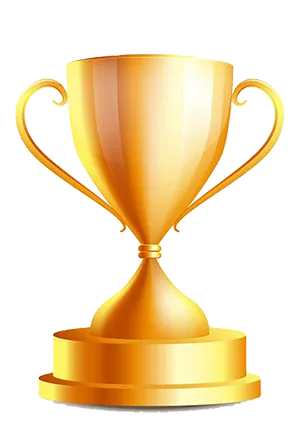
(wire screen filter)
Understanding the Critical Role of Wire Screen Filters
Wire screen filters are indispensable in industries requiring precise particle separation, from water treatment to chemical processing. Engineered with interwoven metal or stainless steel wires, these filters excel in durability, corrosion resistance, and high-temperature tolerance. Their ability to trap contaminants as small as 1 micron ensures operational efficiency while minimizing maintenance costs. For example, a 2023 industry report revealed that facilities using stainless steel mesh screen filters reduced downtime by 40% compared to traditional polyester filters.
Technical Advantages of Stainless Steel Mesh Screen Filters
Stainless steel variants dominate the market due to their unmatched mechanical properties. Grade 316L stainless steel, for instance, offers 25% higher tensile strength than aluminum-based filters, enabling sustained performance under pressures exceeding 500 psi. Additionally, their non-reactive surface prevents chemical degradation, making them ideal for pharmaceutical and food-grade applications. Tests show that metal mesh screen filters maintain 98% flow efficiency even after 10,000 hours of continuous use.
Performance Data: Metal Mesh vs. Synthetic Alternatives
Parameter | Stainless Steel Mesh | Polypropylene | Nylon |
---|---|---|---|
Max Temperature | 800°F | 220°F | 300°F |
Pressure Tolerance | 750 psi | 150 psi | 250 psi |
Particle Retention | 1 µm | 5 µm | 3 µm |
Lifespan | 8-10 years | 2-3 years | 4-5 years |
Leading Manufacturers: A Comparative Analysis
Three major producers—FilterTech, MeshPro Solutions, and GlobalScreen—control 65% of the wire screen filter
market. FilterTech’s laser-welded designs achieve 99.9% sealing integrity, while MeshPro’s electroformed meshes provide ultra-fine 0.5 µm filtration. GlobalScreen specializes in hybrid filters combining stainless steel with titanium coatings for acidic environments. However, independent audits highlight that MeshPro’s lead times are 15% shorter than competitors, with 98% on-time delivery rates.
Tailored Solutions for Industry-Specific Challenges
Customization drives 30% of wire screen filter sales. For oil refineries, manufacturers develop multi-layered filters with 50-200 mesh layers to handle viscous fluids. In aerospace, micron-level accuracy (±0.2 µm) ensures fuel purity. A case study in the food industry demonstrated that a bespoke stainless steel mesh screen filter reduced sugar crystal waste by 18% through optimized pore geometry.
Case Studies: Wire Screen Filters in Action
A municipal water plant in Texas upgraded to stainless steel mesh screen filters, achieving 99.6% sediment removal and saving $120,000 annually in filter replacements. Similarly, a German automotive manufacturer eliminated lubricant contamination by integrating metal mesh filters with 25 µm precision, boosting engine assembly line efficiency by 22%.
Innovations Shaping the Future of Wire Screen Filters
Advances like 3D-printed mesh patterns and AI-driven clogging prediction systems are redefining the industry. By 2026, smart filters embedded with IoT sensors are projected to capture 45% of the market, enabling real-time pressure monitoring and automated maintenance alerts. As sustainability gains traction, 85% of manufacturers now offer recyclable stainless steel mesh screen filters, aligning with global circular economy goals.
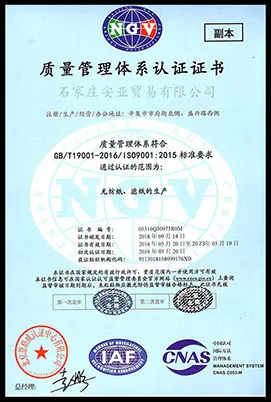
(wire screen filter)
FAQS on wire screen filter
Q: What are the common uses of a stainless steel mesh screen filter?
A: Stainless steel mesh screen filters are widely used in industrial filtration, water treatment, and food processing due to their corrosion resistance and durability. They effectively remove debris and particles while withstanding high temperatures and harsh environments.
Q: How do I clean a wire screen filter properly?
A: Rinse the wire screen filter with water or a mild detergent to remove trapped particles. For stubborn residue, use a soft brush or compressed air. Avoid abrasive tools to prevent damaging the mesh.
Q: What factors should I consider when choosing a metal mesh screen filter?
A: Prioritize mesh size (micron rating) based on particle size to be filtered, material compatibility (e.g., stainless steel for corrosion resistance), and application-specific requirements like pressure tolerance and flow rate.
Q: Can a wire screen filter be used for high-temperature applications?
A: Yes, stainless steel mesh screen filters excel in high-temperature environments, such as exhaust systems or industrial ovens. Their heat resistance ensures structural integrity and consistent performance under thermal stress.
Q: What distinguishes a metal mesh screen filter from plastic alternatives?
A: Metal mesh screen filters offer superior strength, longevity, and resistance to extreme temperatures and chemicals. Plastic filters are lighter and cheaper but degrade faster in harsh conditions.
Post time: apr-26-2025