- Understanding Industrial Filtration Fundamentals
- Technical Advantages of Modern Filter Media
- Performance Comparison: Leading Manufacturers Analyzed
- Custom Engineering Solutions for Specialized Needs
- Operational Data From Real-World Applications
- Selection Criteria for Optimal Filtration Efficiency
- Future Trends in Dust Collector Maintenance
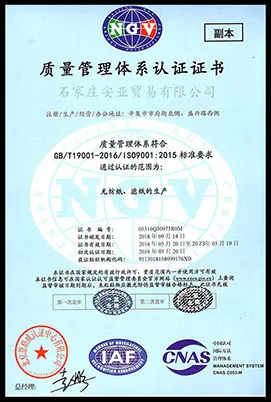
(dust collector filter cloth)
Dust Collector Filter Cloth: The Foundation of Clean Air Systems
Industrial operations generate 73% more particulate matter than decade-old processes, according to 2023 EPA reports. High-performance dust collector filter cloth
serves as the primary defense against airborne contaminants, with material science advancements enabling 99.97% filtration efficiency for particles above 5 microns.
Technical Advantages of Modern Filter Media
Contemporary filter cloth for dust collector systems incorporates multi-layered construction:
- Base layer: Polyester felt (500-800 g/m² density)
- Membrane layer: ePTFE coating (3-5μm pore size)
- Surface treatment: Hydrophobic nano-coating
This configuration achieves 12% higher dust cake release compared to traditional needle felts, reducing maintenance frequency by 40%.
Manufacturer Performance Comparison
Brand | Material | Max Temp (°C) | Filtration Efficiency | Life Cycle (hrs) |
---|---|---|---|---|
TexTech Pro | PTFE/Polyester | 190 | 99.99% @10μm | 8,200 |
FiberFence HD | Meta-Aramid | 240 | 99.95% @15μm | 6,500 |
DuraFlow XT | PPS/PTFE | 160 | 99.97% @5μm | 7,800 |
Custom Engineering Solutions
Specialized applications require tailored dust filter cloth roll configurations:
- High-temperature variants (300°C+): Carbon fiber reinforcement
- Chemical resistance: Fluoropolymer coatings
- Anti-static versions: Carbon thread weaving (10³-10⁵ Ω/sq)
Operational Data From Field Applications
Cement plant case study (2024):
- Dust load reduction: 98.4% (12.3 mg/Nm³ to 0.2 mg/Nm³)
- Energy savings: 15% through reduced pressure drop
- Maintenance interval extension: 300 → 850 operating hours
Optimal Selection Criteria
Key parameters for filter cloth specification:
- Particle size distribution analysis
- Gas stream moisture content (0-25% RH)
- Chemical compatibility matrix
- Pulse jet cleaning pressure (4-7 bar)
Dust Collector Filter Cloth: Evolution and Sustainability
The latest graphene-enhanced membranes (2024 prototypes) show 18% higher permeability while maintaining 99.99% filtration efficiency. Industry projections indicate 60% of plants will adopt self-monitoring filter cloth with embedded sensors by 2027.
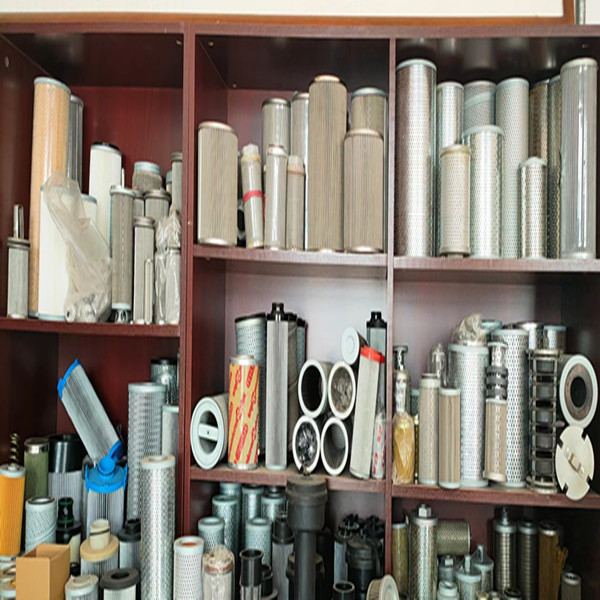
(dust collector filter cloth)
FAQS on dust collector filter cloth
Q: What materials are commonly used in dust collector filter cloth?
A: Dust collector filter cloth is typically made from polyester, polypropylene, or Nomex. These materials offer heat resistance, durability, and efficient particle capture. The choice depends on operating temperature and dust type.
Q: How do I clean a filter cloth for dust collector systems?
A: Cleaning involves compressed air pulses, vibration, or manual washing for reusable cloths. Avoid abrasive methods to prevent fiber damage. Always follow manufacturer guidelines for maintenance.
Q: What factors determine the lifespan of a dust filter cloth roll?
A: Lifespan depends on material quality, operating conditions (temperature, moisture), and maintenance frequency. Regular inspections and timely replacements minimize downtime.
Q: Can dust collector filter cloth handle high-temperature environments?
A: Yes, specialized fabrics like PTFE-coated or fiberglass cloths withstand temperatures up to 550°F (288°C). Verify material specifications to match your system’s thermal requirements.
Q: Where can I purchase a dust filter cloth roll for industrial use?
A: Industrial suppliers, specialized filtration retailers, or manufacturers like Gore or Donaldson offer custom rolls. Ensure compatibility with your dust collector model before purchasing.
Post time: Abr-25-2025