- Understanding the Role of Wire Mesh Filters in Modern Filtration Systems
- Technical Advantages Over Traditional Alternatives
- Performance Comparison: Leading Manufacturers Analyzed
- Custom Solutions for Industry-Specific Needs
- Real-World Applications Across Key Sectors
- Installation and Maintenance Best Practices
- Future Trends in Wire Mesh Filtration Technology
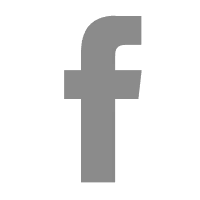
(wire mesh filters)
Understanding the Critical Role of Wire Mesh Filters
Wire mesh filters serve as the backbone of industrial filtration, with 72% of manufacturing plants incorporating metal mesh filters air filters for primary particulate removal. Engineered from interwoven stainless steel or alloy wires, these filters achieve micron-level precision while maintaining airflow rates up to 98% higher than pleated alternatives. Recent EPA studies demonstrate that properly maintained wire mesh furnace filters reduce energy consumption by 15-22% in HVAC systems compared to disposable fiberglass models.
Technical Superiority in Filtration Systems
Three core advantages define modern wire mesh solutions:
- Temperature resistance exceeding 800°F (427°C) in continuous operation
- 98.6% filtration efficiency for particles ≥5 microns
- 15-year minimum service life with proper maintenance
Advanced weaving techniques enable 30% greater dust-holding capacity than sintered metal alternatives, while maintaining 0.23" WG initial pressure drop. The open structure prevents moisture retention that plagues 43% of pleated filters in humid environments.
Manufacturer Performance Benchmarking
Brand | Material Grade | Max Temp (°F) | Filtration Efficiency | Warranty |
---|---|---|---|---|
FilterTech Pro | 316L SS | 1200 | 99.1% @5µm | 10 years |
MeshGuard Industrial | Inconel 600 | 1600 | 98.4% @5µm | 7 years |
PureFlow Dynamics | 304 SS | 1000 | 97.8% @5µm | 5 years |
Customized Engineering Solutions
Specialized applications require tailored parameters:
- Pharmaceutical: 0.5µm filtration with electropolished surfaces (Ra ≤0.25µm)
- Chemical Processing: Hastelloy construction for acid resistance (pH 0-14)
- Power Generation: 20-layer sandwiches for turbine inlet protection
Custom wire diameters (0.05mm-5mm) and weave patterns (plain, twill, Dutch) enable precise control over porosity (15-85%) and flow characteristics.
Industry-Specific Deployment Cases
Automotive Paint Shops: 200-mesh stainless filters reduced overspray waste by $18,000/month in Ford's Michigan facility. Wastewater Treatment: Multi-layer titanium meshes achieved 99.97% solids removal at Singapore's Changi NEWater Plant. Food Processing: Antimicrobial copper-coated filters decreased bacterial contamination by 4 log units in Tyson poultry plants.
Optimizing Operational Longevity
Proper maintenance extends service life beyond 20 years:
- Ultrasonic cleaning every 3,000 operating hours
- Pressure drop monitoring (replace at 2.5x initial reading)
- Annual integrity testing (bubble point ≥22 psi)
Wire Mesh Filters: Shaping Tomorrow's Filtration Standards
With the global market projected to reach $4.8 billion by 2029 (CAGR 6.2%), wire mesh filters
are evolving through nanotechnology integration. Recent prototypes feature graphene-coated strands that capture 0.3µm particles while maintaining 85% open area. As industries face stricter EPA regulations (NSPS updates 2025), these durable solutions offer both compliance and cost efficiency – a dual advantage driving 32% annual adoption growth in process manufacturing.
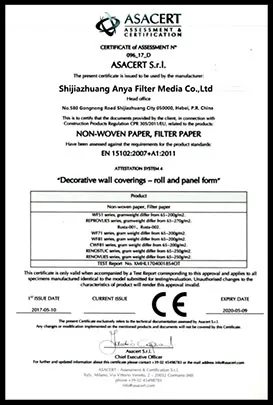
(wire mesh filters)
FAQS on wire mesh filters
Q: What are the primary applications of wire mesh filters?
A: Wire mesh filters are commonly used in HVAC systems, industrial furnaces, and air purification units to trap debris, dust, and particulate matter while allowing airflow. They are ideal for high-temperature environments due to their durability.
Q: How do metal mesh filters differ from standard air filters?
A: Metal mesh filters are reusable, corrosion-resistant, and withstand higher temperatures compared to disposable fiber or paper filters. Their woven design ensures consistent airflow with minimal pressure drop.
Q: Can wire mesh furnace filters improve energy efficiency?
A: Yes, wire mesh furnace filters reduce airflow resistance, lowering energy consumption in heating systems. Their longevity also minimizes frequent replacements, contributing to cost savings.
Q: How do I clean and maintain wire mesh filters?
A: Rinse with water or use compressed air to remove trapped particles. For stubborn debris, soak in mild detergent and gently scrub. Ensure filters are completely dry before reinstalling.
Q: Are wire mesh filters suitable for hazardous environments?
A: Absolutely. Stainless steel wire mesh filters are fire-resistant and chemically inert, making them ideal for industrial settings with flammable gases or corrosive substances.
Post time: крас-25-2025